Al-Si alloys, due to their excellent casting performance, low density, and good mechanical properties, are widely used in the aerospace and vehicle manufacturing fields. Gravity sand casting is an essential process in the casting industry due to its low cost, simple procedures, and short cycle. However, there is limited research on the effects of antimony (Sb) on the primary α-Al grains and eutectic Si of hypoeutectic Al-7Si alloys under gravity sand casting conditions. This article aims to fill this research gap and provide some references for the industrial application of Sb in hypoeutectic Al-Si alloys and the modification and upgrading of Al-7Si alloys.
1. Introduction
Al-Si alloys have been widely used in various applications due to their desirable properties. Modifying the eutectic Si is a common method to improve the mechanical properties of Al-Si alloys, and Sb is known to be an effective modifier. However, the mechanism of Sb modifying eutectic Si is still not fully understood, and there is a need for further research. In this study, we investigate the effects of Sb on the grains and eutectic Si of hypoeutectic Al-Si alloys under gravity sand casting conditions.
2. Experimental Materials and Methods
The experiment was conducted by melting and stirring pure aluminum, Al-12Si, and Al-4Sb in a furnace, and adding Mg at 710 – 720°C after controlling the temperature. The samples were then poured after refining. The actual composition of the alloy was determined using a direct reading spectrometer, and the results are shown in Table 1.
Number | Si | Mg | Ti | Fe | B | Sb | Al |
---|---|---|---|---|---|---|---|
1# | 6.80 | 0.48 | 0.12 | <0.05 | <0.05 | – | allowance |
2# | 6.90 | 0.50 | 0.14 | <0.05 | <0.05 | 0.09 | allowance |
The solidification temperature – time curves were collected using a FLUKE2638A data acquisition instrument and a K-type thermocouple, and each curve was collected three times. The samples for observing the primary α-Al grains were prepared by anodic coating in 1% fluoroboric acid at 25V for 5.5 minutes, and the grains were observed using a BX53MRF – S type polarized light microscope. The samples for observing the eutectic Si were ground using the standard metallographic sample preparation method, and the Al matrix around the eutectic Si was removed by soaking the samples in 20% NaOH solution for 5 minutes. The eutectic Si was observed using a TESCAN MIRA LMS type scanning electron microscope, and the nucleation cores of the eutectic Si were observed by electron backscattered diffraction (EBSD), with the samples thinned by ion milling. The grain size was statistically analyzed using the random line cutting method, and the length and width of the eutectic Si were statistically analyzed using the Image – Pro Plus software, with more than 40 grains and 120 eutectic Si being statistically analyzed. The samples for observing the twins of the eutectic Si were also thinned by ion milling, and the twins were observed using a FEI Tecnai F20 type transmission electron microscope, and the chemical composition of the eutectic Si was analyzed using the energy dispersive spectrometer attached to the microscope.
3. Results and Discussion
3.1 Effects of Sb on Primary α-Al Grains
The solidification temperature – time curves of 1# and 2# alloys are shown in Figure 1. The nucleation temperature of the primary α-Al grains (TAlN) and the nucleation temperature of the eutectic Si (TSiN) can be determined from the curves. As shown in Figure 1(a), without the addition of Sb, the TAlN of the Al – 7Si alloy is 619.5°C, and the TSiN is 578.1°C. However, as shown in Figure 1(b), after adding 0.09% Sb, the TAlN decreases to 611.8°C, and the TSiN decreases to 572.6°C.
The images of the primary α-Al grains in the Al – 7Si alloy are shown in Figure 2. As shown in Figure 2(a), without the addition of Sb, most of the primary α-Al grains in the Al – 7Si alloy are dendritic, and a few are equiaxed, with an average size of 319 μm. As shown in Figure 2(b), after adding 0.09% Sb, the morphology of the primary α-Al grains in the Al – 7Si alloy changes little, but the average size increases to 353 μm.
The nucleation of primary α-Al grains requires a certain degree of undercooling, which is the difference between the theoretical nucleation temperature and the actual nucleation temperature. The lower the actual nucleation temperature, the greater the undercooling required for nucleation, and the more difficult the nucleation of the grains, resulting in an increase in the grain size. From Figure 1, it can be seen that after adding 0.09% Sb, the actual nucleation temperature of the primary α-Al grains in the Al – 7Si alloy decreases, indicating that the undercooling required for nucleation increases, and the nucleation of the grains becomes more difficult, thus leading to an increase in the grain size.
3.2 Effects of Sb on Eutectic Si
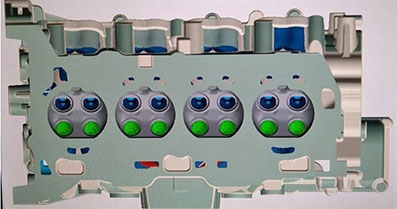
The morphology, length, and width of the eutectic Si in the Al – 7Si alloy are shown in Figure 3. As shown in Figure 3(a), without the addition of Sb, the eutectic Si in the Al – 7Si alloy is plate – like, with an average length of 19.7 μm and an average width of 8.1 μm. As shown in Figure 3(b), after adding 0.09% Sb, the eutectic Si in the Al – 7Si alloy becomes shorter and narrower, with the average length decreasing to 13.3 μm and the average width decreasing to 5.4 μm. This shows that Sb has a good modifying effect on the eutectic Si of the Al – 7Si alloy.
According to the Al – Si binary alloy phase diagram, the lower the temperature, the smaller the solid solubility of Si in α – Al. During the solidification process, the driving force for Si atoms to leave α – Al is the chemical potential of the Si atoms. The greater the chemical potential, the faster the rate at which the Si atoms leave, and this chemical potential is the difference between the content of the Si atoms and the solid solubility. From Figure 1, it can be seen that after adding Sb, the nucleation temperature of the eutectic Si (TSiN) decreases, resulting in a decrease in the solid solubility of Si in α – Al. However, the designed content of the Si atoms is the same, which means that the chemical potential increases, and the rate at which the Si atoms are squeezed to the front of the solid – liquid interface increases, leading to an increase in the growth rate of the eutectic Si. At the same time, the growth rate of the eutectic Al also increases, resulting in the shortening and narrowing of the eutectic Si.
3.3 Mechanism of Sb Modifying Eutectic Si
The modification of eutectic Si is closely related to its nucleation cores and the number of twins. The EBSD images of the nucleation cores of the eutectic Si are shown in Figure 4. If the eutectic Si grows from the same nucleation core, the orientation is the same, that is, the color on the EBSD image is the same; if the nucleation cores are different, the color on the EBSD image is different, that is, the more colors in the eutectic Si region on the EBSD image, the more nucleation cores of the eutectic Si. From Figure 4, it can be seen that after adding Sb, the color types in the eutectic Si region on the EBSD image change little, indicating that under the gravity sand casting conditions, Sb does not modify the eutectic Si by increasing the number of nucleation cores.
The TEM images of the 2# alloy are shown in Figure 5. As shown in Figure 5(a), after adding Sb, no twins are observed in the eutectic Si. The energy spectrum shown in Figure 5(b) indicates that there is no Sb element in the eutectic Si (the Cu atoms come from the Cu grid supporting the sample). In Figure 5(c), no characteristic spots of twins are observed, indicating that no twins are formed in the eutectic Si. If the modifier modifies the eutectic Si by acting on the twins, the modifier atoms will be enriched at the twins of the eutectic Si. Therefore, it can be seen that under the gravity sand casting conditions, Sb does not modify the eutectic Si by acting on the twins. If the modifier atoms can induce the formation of twins in the eutectic Si, the diameter ratio of the modifier atoms to the Si atoms is close to 1.65, while the diameter ratio of the Sb atoms to the Si atoms is 1.32. Therefore, after adding Sb, no more twins appear in the eutectic Si. In summary, Sb does not play its role of modification by acting on the nucleation cores and twins of the eutectic Si.
4. Conclusion
- After adding Sb, the nucleation temperatures of the primary α – Al grains and the eutectic Si in the gravity sand casting Al – 7Si alloy both decrease; the nucleation of the primary α – Al grains becomes more difficult, and the average particle size increases from 319 μm to 353 μm.
- The mechanism of Sb modifying the eutectic Si in the gravity sand casting Al – 7Si alloy is that the addition of Sb reduces the nucleation temperature of the primary α – Al grains, decreases the solid solubility of Si in α – Al, increases the chemical potential, increases the rate at which the Si atoms are discharged from α – Al, increases the growth rate of the eutectic Si, and finally leads to the shortening and narrowing of the eutectic Si. Sb does not play its role of modification by acting on the nucleation cores and twins of the eutectic Si.
In conclusion, this study provides valuable insights into the effects of Sb on the grains and eutectic Si of hypoeutectic Al – Si alloys under gravity sand casting conditions. Further research is needed to fully understand the mechanism of Sb modification and to explore its potential applications in the improvement of the properties of Al – Si alloys.
5. Further Discussion on Gravity Sand Casting
Gravity sand casting is a widely used casting process in the manufacturing industry. It offers several advantages, such as low cost, simplicity, and the ability to produce complex shapes. However, it also has some limitations that need to be considered.
One of the key factors in gravity sand casting is the quality of the sand mold. The sand should have appropriate properties, such as good permeability, strength, and collapsibility, to ensure proper filling and solidification of the molten metal. Additionally, the preparation of the sand mold requires careful control of parameters like moisture content and compaction to achieve consistent results.
In the context of Al-Si alloys, the solidification behavior during gravity sand casting can have a significant impact on the microstructure and properties of the final product. The cooling rate during solidification plays a crucial role in determining the size and morphology of the primary α-Al grains and the eutectic Si. Slower cooling rates may lead to larger grains and coarser eutectic structures, which can affect the mechanical properties of the alloy.
To improve the quality of gravity sand castings, various techniques and modifications can be employed. For example, the use of inoculants or modifiers, such as Sb in this study, can help refine the grain structure and modify the eutectic Si. Additionally, optimizing the casting parameters, such as pouring temperature and mold temperature, can also have a positive effect on the casting quality.
Another aspect to consider is the post-casting processing of the gravity sand castings. Heat treatment can be used to further modify the microstructure and improve the mechanical properties of the alloy. For instance, solution treatment and aging can be applied to enhance the strength and hardness of the Al-Si alloy.
In terms of industrial applications, gravity sand casting is commonly used in the production of various components, including engine blocks, cylinder heads, and pump housings. The ability to produce large and complex parts makes it suitable for many industries, such as automotive, aerospace, and machinery.
However, it is important to note that gravity sand casting may not be suitable for all applications. In cases where high precision or tight tolerances are required, other casting processes may be more appropriate. Additionally, the surface finish of gravity sand castings may need further improvement through machining or other surface treatment methods.
In conclusion, gravity sand casting is a valuable casting process that offers advantages in terms of cost and versatility. Understanding the effects of various parameters, such as the addition of modifiers like Sb, on the microstructure and properties of Al-Si alloys is crucial for optimizing the casting process and obtaining high-quality castings. Further research and development in this area can lead to improved performance and expanded applications of gravity sand castings in the future.