Lost foam casting is considered a “green and environmentally friendly casting” in the entire casting industry. Due to its advantages such as high dimensional precision of castings and low production costs, it is recognized by more and more casting enterprises in China. However, while developing, due to the imperfect performance of the pattern materials, the lost foam (full mold) casting process can cause defects such as carburization, porosity, and back-spurt when pouring steel products, which greatly limits the promotion of this technology. This seriously restricts the application of lost foam (full mold) casting in steel casting. Without the support of complete and improved raw and auxiliary materials, steel casting enterprises have sought another hollow shell pouring process of “pour after burning off the polystyrene foam pattern”. However, they do not realize that this method can only be used in experimental and small-scale production. When it comes to mass production of steel castings, it will cause many problems.
1. The Sources of Gas and Carbon in the Pattern Material
The main raw materials of the pattern material are: acrylate, styrene, and pentane. EPS contains 100% styrene. Ordinary copolymer contains 70% MMA and 30% styrene. EMB contains 90% acrylate and 10% styrene. The raw material of acrylate (or MMA) belongs to the open-link type, which decomposes into small organic gaseous molecules, CO2, and H2O during combustion. This is one of the gases generated during the pyrolysis of the pattern. Styrene contains a benzene ring structure and decomposes into a charred polycondensate during combustion, which is commonly known as carbon tar. This is the main reason for the generation of carbon during the pyrolysis of the pattern. Pentane is a hydrocarbon, similar to gasoline, and decomposes into gas and micro-carbon during combustion.
2. Comparison of the Casting Application Methods, Costs, etc. between Full Mold Pouring and Pour after Burning Off
The lost foam (full mold) casting method is the simplest casting operation method in which various patterns are brushed with a coating and directly placed in the sand box for pouring.
The lost foam casting method of pouring after burning off is to first place the made white mold, with a certain strength of coating, into the sand box, and then use an open flame to burn it first before injecting the molten iron.
The comparisons between the two operating processes are as follows:
The reasons for back-spurt and entrained air: It is caused by the rapid pyrolysis of the pattern material when encountering the molten iron. Firstly, the pentane content in the pattern material is too high. When the product is produced by one-step polymerization, its pentane content is wrapped in the core of the sphere. At the same time, due to the higher molecular weight, more pentane is required for pre-expansion and molding, and the skin is thicker, which will cause the pentane in the pattern to not run out completely, resulting in internal entrained air and back-spurt problems. At present, the EMB product has improved this performance. We have added a special locking agent. When the sphere is not pre-expanded, it can firmly lock the pentane. Once pre-expanded, it can run fast without affecting the molding conditions, thereby reducing the pentane content to less than 3% during pouring to reduce internal entrained air and back-spurt phenomena. Since EMB is a low-carbon product and the content of acrylate is higher than that of ordinary copolymers, the gas volume is 904.14 mL/g. When we cannot change the total gas volume of the pattern material, we can only reduce the back-spurt by making the pattern material generate gas evenly during the instantaneous combustion through uniform burning.
Compared to the two casting methods, for the cost of the coating, the full mold casting method saves more coating costs than the pour after burning off method because the thickness of the coating layer is reduced by 40%, thereby reducing the cost.
In the entire operation, since the pour after burning off method requires the coating to be made to a certain strength, the process, cycle, time, and energy consumption of applying the coating are more complex and costly than the full mold casting. Generally, the number of coating applications will be 2 to 4 times more, and the time will be 2 to 5 days longer.
The lost foam casting method of pouring after burning off is to burn the white mold pattern completely through various methods. However, EPS contains 100% styrene, and styrene contains a benzene ring structure. After combustion, it will form carbon tar, which cannot be burned completely. At the same time, when the carbon tar forms a hard lump, even high-temperature molten steel cannot burn it completely, but will instead cause carburization.
3. Technical Analysis of Gas and Carbon in the New Pattern Material EMB
When using the lost foam (full mold) casting technology to pour steel castings, high-quality pattern materials are required: the appearance quality of the pattern, low carbon point, and no back-spurt and entrained air phenomena are very critical technical points.
Appearance: The original intention of the EMB design is to learn from the pattern surface of Japanese JSP. After the pre-expanded sphere has a certain melting solubility, we can obtain a more beautiful and smooth pattern surface during molding.
Low carbon point: EMB only contains 10% styrene, and the calculated carbon increase from the styrene content is 3.2 carbon atoms.
4. Application Feedback of the Third-generation EMB Product in the Direct Pouring of 25Mn Steel Casting Brackets
Compared to the full mold pouring, the pour after burning off process has more and more complex procedures. When the number of production processes increases, there will be more production variable factors.
4.1 Preparation of the White Mold
During the burning process of the pour after burning off method, a certain amount of negative pressure value of the sand box system will be lost. This requires that the vacuum system maintains a stable negative pressure in the sand box during the pouring process. This will cause certain instability factors for the process control.
After comparing the above two process schemes, we can clearly understand the superiority of the full mold casting method. However, the only fatal point of the full mold casting method is the low carbon and micro-back-spurt of the pattern material. Currently, in the global pattern material market, it is of the utmost importance to find this kind of low-carbon and micro-back-spurt material that meets the production requirements of the full mold casting. Based on this, we have developed an expandable acrylate pattern material (referred to as “EMB”) to solve the quality problems required by the full mold casting method.
4.2 Coating Application
The coating used is the special coating for steel lost foam casting (for the research of the third-generation EMB).
4.3 Melting, Molding, and Pouring
The melting material is 25Mn steel casting, with a carbon content requirement of 0.25%, and the pouring temperature is 1580 – 1610 °C. The molding is done by using a rain-type sand addition and vibration compaction. EMB302 is poured directly, with a pouring negative pressure of 0.05 – 0.07 MPa, and the actual pouring time for each piece is 55 s, with occasional slight back-spurt phenomena. The ordinary copolymer is also poured directly, with a pouring negative pressure of 0.05 – 0.07 MPa, and the actual pouring time for each piece is 55 s, with occasional larger back-spurt phenomena. The sampling positions for the sampling and analysis are taken from the upper, middle, and lower parts of the casting according to the pouring position. The results of the spectral analysis are listed in Tables 2, 3, and 4.
The final product physical photo is shown in Figure 4. It can be seen that after heat treatment and tempering, the performance is qualified, and the EMB-poured product has no cracks or other casting defects during flaw detection.
The above analysis results show that the carbon increase in the upper, middle, and lower positions of the casting body is relatively uniform, ranging from 0.002% to 0.038%, which fully meets the carbon content requirement of 0.25% of the material. The carbon increase in the upper, middle, and lower positions of the conventionally copolymer bead-poured product body is within the range of 0.044% to 0.100%, exceeding the required range.
The results show that the castings produced using the new third-generation EMB polymer beads have a lower carbon increase, and the carbon content of the castings is more controllable.
5. Conclusion
Using the full mold pouring method and the third-generation new pattern material EMB, the 25Mn steel castings have been successfully cast. Lost foam casting is a seemingly simple but actually complex process, belonging to a systematic engineering. Every link in the entire production chain requires strict attention and cannot be ignored. Although we have obtained qualified castings in this experiment, we will conduct batch and gradual industrial-scale tracking and production tests. We hope to promote the development of lost foam (full mold) casting in high-end casting products with this successful case.
In conclusion, the application of the new pattern material EMB in lost foam casting has effectively solved the problems of carburization and back-spurt in steel castings, improving the production yield and the quality of the castings. However, further research and optimization are still needed to fully realize the potential of lost foam casting in the steel casting industry.
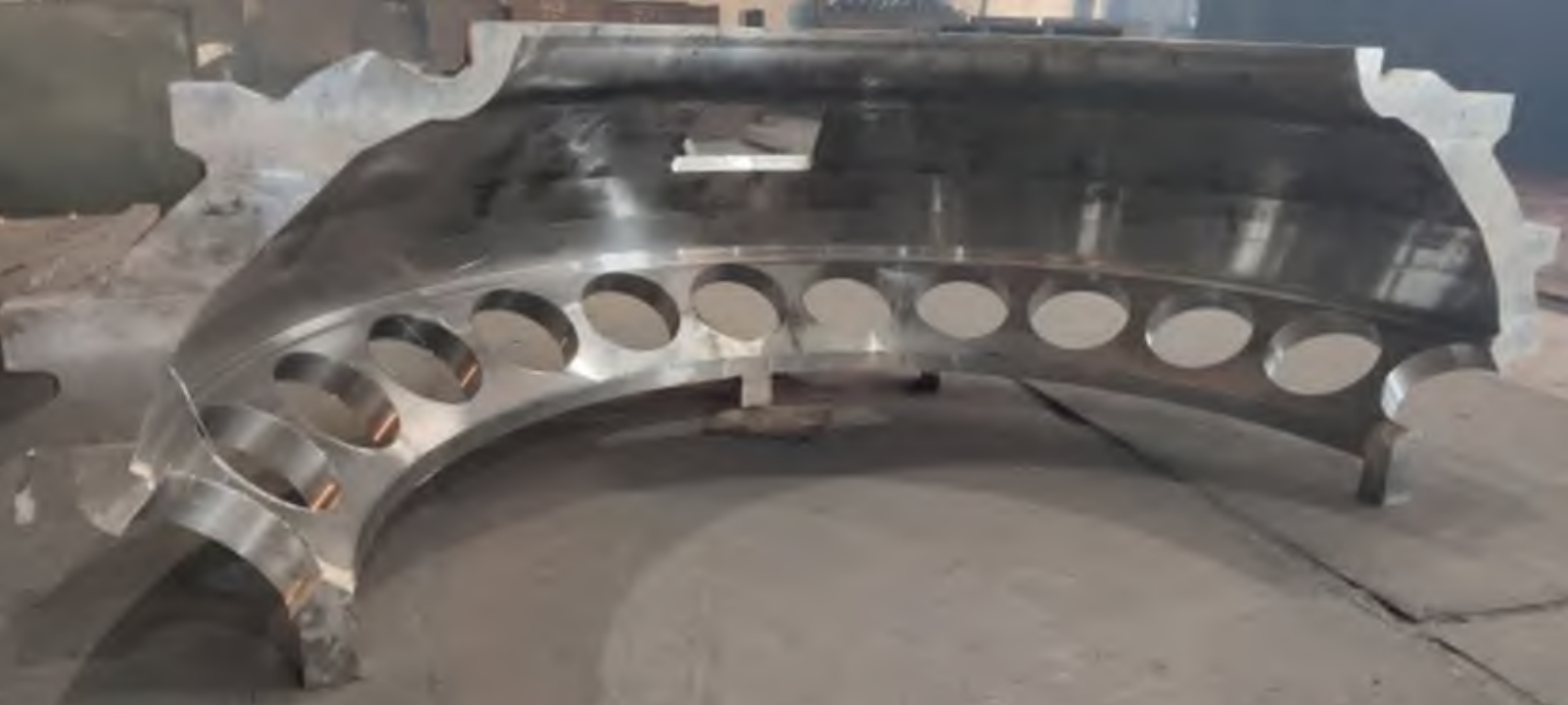