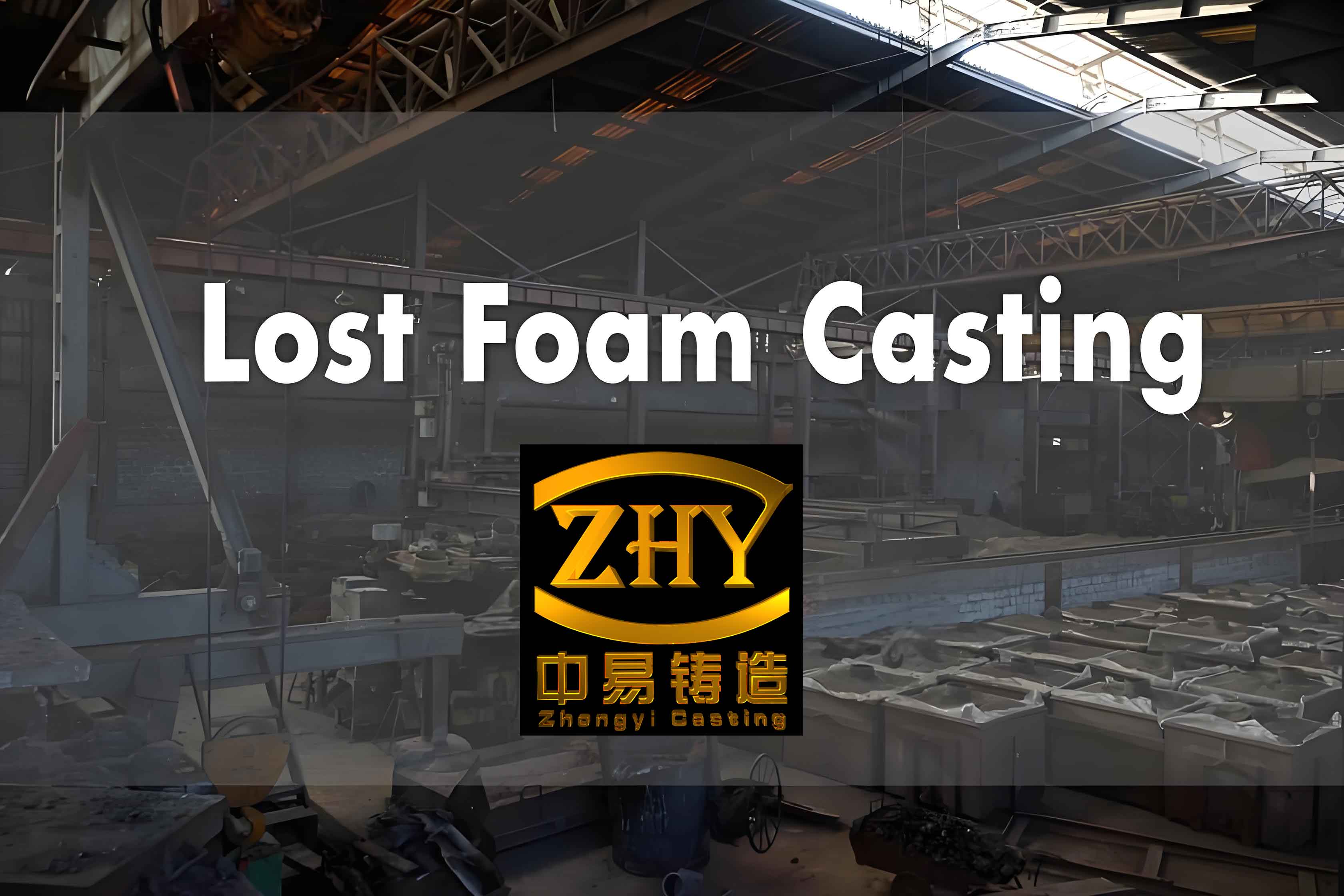
1. Introduction
Lost foam casting has emerged as a significant casting process with numerous advantages over traditional methods. In the context of machine tool spindle box castings, which have complex structures and high-quality requirements, the application of lost foam casting presents both opportunities and challenges. This article delves into the details of this application, exploring various aspects such as process design, defect prevention, and quality control.
1.1 Background of Machine Tool Castings
Machine tool castings, especially spindle box castings, play a crucial role in the performance of machine tools. Traditionally, methods like the furan resin sand process have been commonly used. However, this process has several drawbacks, including a harsh production environment due to the irritating smell of the furan resin binder, complex molding and boxing operations, and difficulties in recycling the sand.
1.2 Advantages of Lost Foam Casting
Lost foam casting offers several benefits in comparison. It provides a better production environment, with reduced odors and emissions. The resulting castings have excellent surface quality and high dimensional accuracy. Additionally, the process eliminates the need for parting and core assembly, reducing the skill requirements for workers and minimizing the post-casting cleaning and grinding workload.
2. Product Introduction and Process Planning
2.1 The Spindle Box Casting
The 1165 spindle box for a vertical machining center is a key component. It has a part size of 910mmX650mmX520mm after machining and is made of HT300 material. Its structure is complex, with specific requirements for various surfaces and interfaces, such as the spindle hole, motor mounting surface, and guide rail surface, which must be free of casting defects and not allow for welding repairs.
2.2 Process Analysis and Design
Before manufacturing the lost foam mold, a detailed process analysis and casting process scheme design are essential. This involves considering factors such as the direction of negative pressure and the flow of sand. By communicating with the designers of the host factory, six 40mm holes were added to optimize the process. The spindle hole end was placed upward, the slider installation surface downward at 30° angle, and risers were placed at both ends for pouring.
3. Casting Process Design and Defect Prevention Control
3.1 White Model Process
The white model is made of EPS material. After foaming, it undergoes a drying process at different temperatures and durations: 25°C for 2 hours, 30°C for 2 hours, 35°C for 2 hours, and 40°C for 30 hours. After leaving the baking room, the white model, runner, and riser are glued together. The bonding seams of the white model are sealed with masking tape to prevent paint infiltration. The runner is fixed with fiber rods, and ceramic tiles are attached to the parts of the white model on the baking rack to protect the coating.
3.2 Coating Process
After the white model is bonded, a lost foam special coating with a Baume degree of 70 – 75 is applied to its surface. The coating process can be either spraying or dipping, and it is applied in three layers, with each layer having a thickness of at least 0.5mm and a total thickness of at least 1.8mm . After each coating application, a drying process is carried out at different temperatures: 35°C for 2 hours, 40°C for 2 hours, 45°C for 2 hours, 50°C for 3 hours, and 55°C for 6 hours.
3.3 Burying Box Process
After the spindle box lost foam is dried, it is buried in a box. The total vertical runner is placed vertically according to the process requirements. During the sand filling process, the sand in the corners and cavities is tamped down. After covering with a film, a pouring cup is placed, waiting for pouring.
3.4 Pouring Trial Production
3.4.1 Charge and Chemical Composition
To reduce costs, a medium-frequency electric furnace and a blast furnace hot metal short-process technology are used. The blast furnace hot metal accounts for 35%, scrap steel for 45%, and the rest is the same material return material. The specific chemical composition is shown in Table 1.
Element | C | Si | Mn | S | P | Cr |
---|---|---|---|---|---|---|
Content | 3.1 – 3.2 | 1.7 – 1.9 | 0.8 – 1.0 | 0.06 – 0.08 | ≤0.06 | ≤0.02 |
3.4.2 Melting and Pouring
A large amount of blast furnace hot metal requires an increase in melting temperature and high-temperature standing. The iron liquid is sampled for furnace-front analysis at 1450°C, then heated to 1520 – 1550°C for high-temperature standing for 8 – 10 minutes. The functions of high-temperature standing include refining the graphite and matrix, generating a self-deoxidation reaction to reduce oxygen content and oxidation slag, and improving the inoculation effect. After high-temperature standing, the iron liquid is poured using methods such as ladle cooling, ladle inoculation, and stream inoculation. The ladle inoculant uses a silicon-barium-calcium long-acting inoculant with an inoculation amount of 0.4%, and the stream inoculant uses a sulfur-oxygen inoculant with a particle size of 0.2 – 0.7mm and an inoculation amount of 0.1%. The pouring temperature is 1420 – 1460°C, the negative pressure is 0.06 – 0.07MPa, and the holding time is 15 minutes. After casting and machining, the spindle hole, motor mounting surface, and guide rail surface have no casting defects, and the casting qualification rate is above 98%.
3.5 Defect Prevention Control
3.5.1 Collapse of the Mold (Collapsing Box)
Collapsing box is a defect where the mold collapses downward during pouring, preventing the metal liquid from flowing directly into the cavity and resulting in pouring failure. The main reasons for this defect include slow pouring speed (especially in the case of interrupted pouring, where the metal liquid cannot seal the sprue, causing a sharp drop in the vacuum degree in the sand box), an 不合理的浇注系统设计 (unreasonable pouring system design), and a low pumping capacity of the vacuum system. To prevent this defect, measures such as controlling the pouring speed to ensure the pouring cup is always filled with metal liquid and avoiding interrupted pouring, designing a reasonable pouring system (especially the position of the ingate), and using a vacuum pump with a large pumping capacity and a sand box structure with multi-sided pumping are taken.
3.5.2 Sand Adhesion
Sand adhesion refers to the casting defect where the casting surface adheres to the molding material and is difficult to clean. It can be divided into mechanical sand adhesion (permeation sand adhesion) and chemical sand adhesion (sintering sand adhesion). It usually occurs on the bottom or lower side of the casting, as well as in hot spots and areas where the sand mold is not compact. The main reasons for this defect include a too-thin coating layer or a low refractory degree of the coating layer, an uncompacted or uneven sand mold, and a too-high pouring temperature. To prevent this defect, measures such as increasing the coating thickness and layers to improve the refractory degree of the coating layer, pre-filling resin sand in the dead corners of the casting, and reasonably controlling the pouring temperature and vacuum degree are taken.
3.5.3 Gas Holes and Slag Inclusions
Gas holes and slag inclusions exist beneath the surface of the casting, usually in the upper part or dead corners. These defects are visible after the casting is machined, and in most cases, both exist simultaneously. The main reasons for these defects include a large amount of gas and a certain amount of residue generated after the foaming plastic is gasified (which is the main source of gas and slag inclusions), an unreasonable pouring system or an unreasonable structure of the ingate (where the sprue cannot be filled, making it easy for gas and residue to be trapped in the metal liquid, forming gas holes and slag inclusions), a too-low pouring temperature (which cannot make the gas and residue fully excluded and floated to the top of the casting, easily generating gas holes and slag inclusions), and in the case of thick-section castings, if the metal liquid advances too fast under the negative pressure, a part of the foaming plastic will be surrounded by the metal liquid, forming gas holes. To prevent these defects, measures such as 合理埋箱 (reasonable burying of the box) to suppress the gas generation of the plastic foam, improving the permeability of the coating layer and the pumping capacity of the vacuum system to make the gasified gas timely removed from the cavity, designing a reasonable pouring system to make the filling direction of the metal liquid consistent with the floating direction of the gasified gas and residue, choosing the best pouring temperature and slowing down the pouring speed appropriately when the pouring is about to end to make the gasified gas and residue have sufficient time to be excluded from the cavity and rise to the top of the casting, and designing a slag-collecting riser at the highest point of the casting and appropriately increasing the machining allowance on the top of the model to eliminate gas holes and slag inclusions by metal cutting are taken.
4. Conclusion
Lost foam casting shows great potential in the production of machine tool spindle box castings. Despite the challenges posed by casting defects, through proper process design and defect prevention measures, high-quality spindle box castings can be produced with a qualification rate of over 98%. This not only meets the quality requirements of the castings but also provides a technical guarantee for the healthy development of enterprises. As the technology continues to evolve and improve, it is expected to play an even more important role in the field of machine tool casting.