1. Introduction
In the automotive industry, the demand for high-quality engine cylinder heads is increasing. Sand casting is a widely used manufacturing process for producing complex-shaped components such as cylinder heads. This article focuses on the numerical simulation and process optimization of sand casting for cylinder heads, aiming to improve the casting quality and production efficiency.
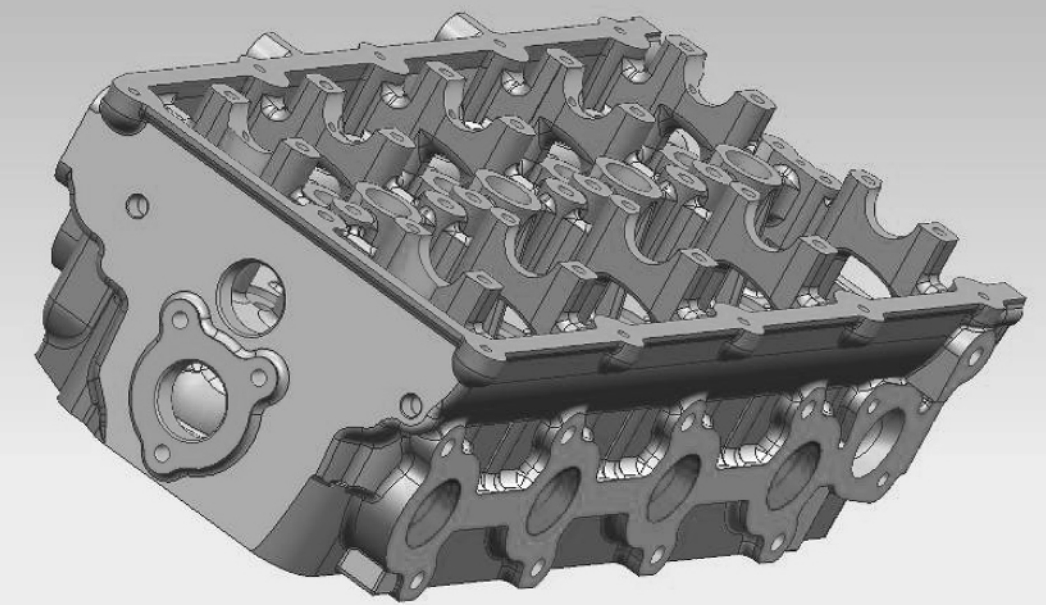
2. Sand Casting Process for Cylinder Head
2.1 3D Modeling and Process Design
The 3D model of the engine cylinder head was created using UGNX8.0 software. The material used for the cylinder head is ZL105 aluminum alloy, which has excellent casting properties. The chemical composition of ZL105 aluminum alloy is shown in the following table:
Element | Si | Cu | Mg | Al |
---|---|---|---|---|
Content (%) | 4.5 – 5.5 | 1.0 – 1.5 | 0.4 – 0.6 | Remainder |
The casting process design includes the selection of parting surface, gating system design, and riser design. The parting surface was chosen to ensure the smooth production and removal of sand cores, minimize the number of parting surfaces, and use a flat parting surface whenever possible. A single-sided bottom gating system was adopted to avoid direct impact of the molten metal on the mold sand and ensure a smooth rise of the liquid level. A waist-shaped open riser was selected and placed on the upper box. The CAD system was used to calculate the riser modulus and determine other related parameters. The designed casting mold CAD model.
2.2 Simulation Process
The designed casting mold CAD model was exported in IGES format from UGNX8.0 and meshed using the GeoMESH meshing module of ProCAST. The mesh cell length was generally 1/2 – 1/3 of the minimum wall thickness. The casting was divided into 115,990 total nodes and 508,256 unit cells. The meshing result.
The molding material used was phenolic urethane resin sand with silicon sand as the main component. The required boundary conditions are shown in the following table:
Pouring Temperature (°C) | Pouring Rate (kg/s) | Initial Casting Temperature (°C) | Initial Mold Temperature (°C) | Solidus Temperature of ZL105 Alloy (°C) | Liquidus Temperature of ZL105 Alloy (°C) | Interface Heat Transfer Coefficient (W/m²·K) |
---|---|---|---|---|---|---|
690 – 720 | 0.75 – 1.5 | 690 – 720 | 25 | 536 | 622 | 200 – 1000 |
3. Simulation Results and Analysis
3.1 Filling Process Simulation
The filling process of the molten metal was simulated using ProCAST. The filling status and temperature distribution at different stages. It can be seen that the single-sided bottom gating system can achieve smooth filling of the molten metal. The filling time of each part of the casting. The entire filling process lasted 15.43 seconds. The slow filling in the initial stage avoided sand washing and air entrainment, and the final stage filling speed slowed down again due to gravity and pouring pressure, but the riser part could still be filled without increasing the height of the static pressure head.
3.2 Solidification Process Simulation
The solidification process of the casting was also simulated. The solid fraction at different solidification times. It can be seen that the outer wall of the cylinder head solidified first, followed by the internal solidification of the casting, and the gating system had the longest solidification time. The riser provided good feeding for the thick parts at the upper part of the cylinder head, and the ingate achieved feeding for the thick parts at the lower end of the cylinder head. There was no obvious isolated liquid phase region in the entire casting.
The locations and porosities of shrinkage pores and shrinkage cavities formed under this filling condition. It can be seen that only uniformly dispersed shrinkage pores and shrinkage cavities occurred inside the casting, and the porosity was generally less than 10%, indicating good casting quality.
4. Production Verification
Based on the casting process design and numerical simulation results, the processes of molding, repairing, coating, and casting were completed. The cylinder head casting product. It can be seen that the casting surface has a clear contour and no obvious defects. Microstructural observation of the sections prone to casting defects revealed a dense microstructure and fine grains.
5. Conclusion
In this study, the numerical simulation of the filling and solidification processes of rapid sand casting for engine cylinder heads was carried out using ProCAST software. The results showed that the single-sided bottom gating system could achieve smooth filling, and the casting quality was good with uniform distribution of shrinkage pores and shrinkage cavities and a porosity less than 10%. The production verification also confirmed the effectiveness of the process design. This research provides a reference for the optimization of sand casting processes for cylinder heads and the improvement of casting quality.