1. Introduction
Sand casting remains a cornerstone of metal casting industries due to its versatility, cost-effectiveness, and adaptability to complex geometries. However, traditional trial-and-error methods for optimizing casting processes are time-consuming and resource-intensive. This study focuses on leveraging numerical simulation technologies to predict defects, optimize process parameters, and enhance the quality of sand-cast components. By integrating computational fluid dynamics (CFD), finite element analysis (FEA), and advanced software tools like ProCAST and ANSYS, this work aims to bridge the gap between theoretical models and industrial applications in sand casting.
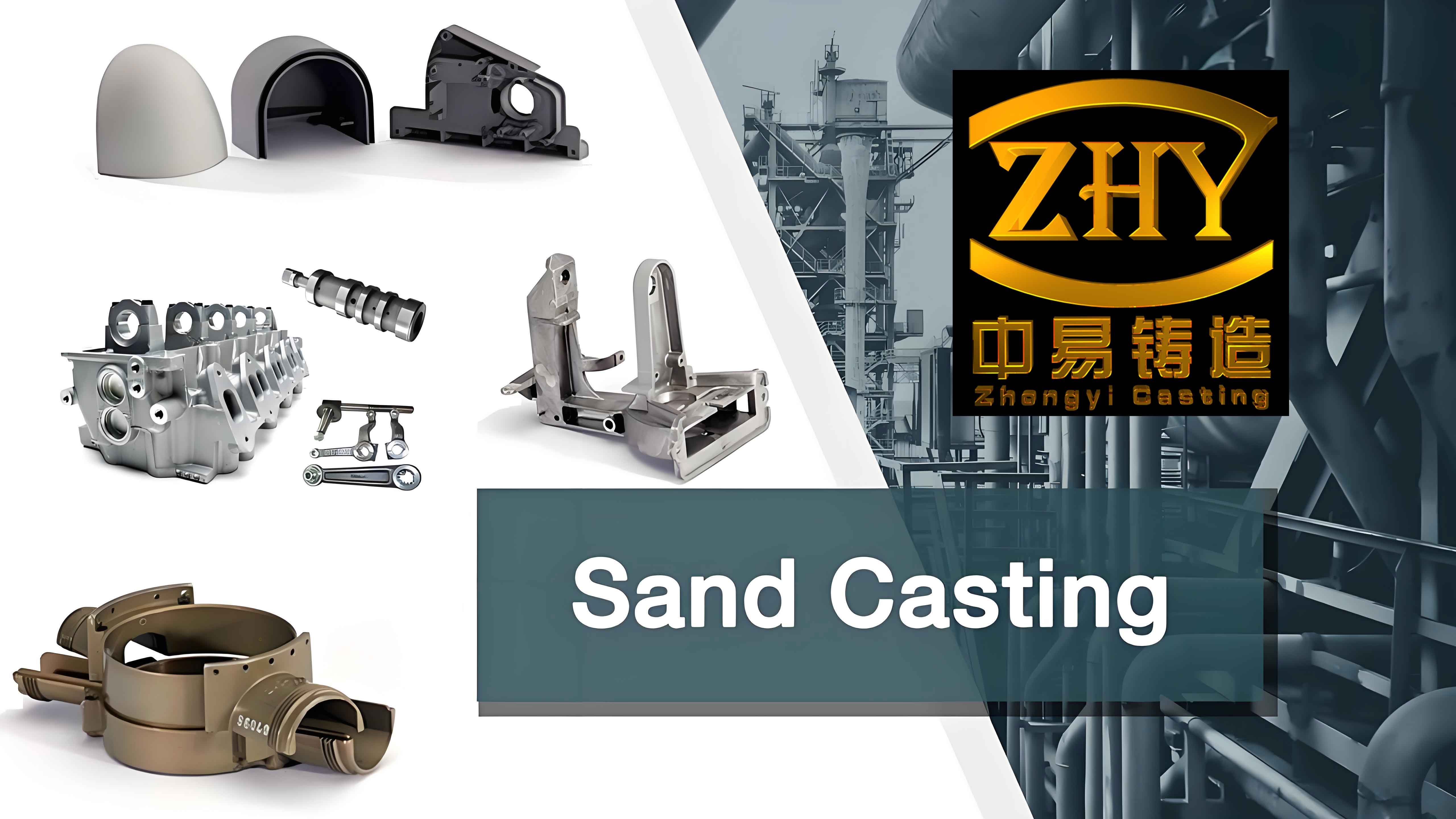
2. Fundamentals of Numerical Simulation in Sand Casting
Numerical simulation of sand casting involves solving coupled thermo-mechanical equations to model fluid flow, heat transfer, and stress evolution during mold filling, solidification, and cooling. Key governing equations include:
2.1 Governing Equations
- Continuity Equation:∂ρ∂t+∇⋅(ρu)=0∂t∂ρ+∇⋅(ρu)=0where ρρ is density and uu is velocity.
- Momentum Conservation (Navier-Stokes):ρ(∂u∂t+u⋅∇u)=−∇P+μ∇2u+ρgρ(∂t∂u+u⋅∇u)=−∇P+μ∇2u+ρgwhere PP is pressure, μμ is dynamic viscosity, and gg is gravitational acceleration.
- Energy Equation:ρcp∂T∂t+ρcpu⋅∇T=∇⋅(λ∇T)+Qlatentρcp∂t∂T+ρcpu⋅∇T=∇⋅(λ∇T)+QlatentHere, cpcp is specific heat, λλ is thermal conductivity, and QlatentQlatent accounts for latent heat release during solidification.
2.2 Material Properties and Boundary Conditions
Material properties such as thermal conductivity, viscosity, and specific heat are temperature-dependent. For example, the thermal conductivity of QT450-10 ductile iron varies with temperature (Table 1).
Table 1: Temperature-dependent thermal conductivity of QT450-10
Temperature (°C) | Thermal Conductivity (W/m·K) |
---|---|
25 | 35.2 |
500 | 28.7 |
1000 | 22.4 |
Boundary conditions include heat transfer coefficients at mold-metal interfaces (500 W/m²·K for sand molds) and ambient convection (10 W/m²·K).
3. Mold Filling and Solidification Simulation
3.1 ProCAST Workflow for Sand Casting
- Geometry Modeling: CAD tools like Pro/ENGINEER are used to design the casting, gating system, and molds.
- Mesh Generation: Surface meshing in Pro/MECHANICA followed by volumetric meshing in MeshCAST.
- Parameter Setup: Assign material properties, initial temperatures, and boundary conditions.
- Simulation Execution: Solve coupled fluid flow and heat transfer equations.
3.2 Case Study: Flywheel Casting Defect Analysis
A sand-cast flywheel (material: QT450-10) exhibited shrinkage porosity due to suboptimal riser design. ProCAST simulations revealed premature solidification of feeding channels (Figure 1). Key parameters included:
Table 2: Initial and optimized process parameters
Parameter | Initial Design | Optimized Design |
---|---|---|
Pouring Temperature | 1380°C | 1380°C |
Riser Volume | 1800 mm³ | 3600 mm³ |
Cooling Time | 15 s | 12 s |
Post-optimization, risers were repositioned near thermal hotspots, and chill blocks were added to enforce directional solidification. X-ray inspection confirmed a 70% reduction in shrinkage defects.
4. Stress Field Analysis Using ANSYS
4.1 Thermo-Elastoplastic Model
Residual stresses in sand-cast components arise from non-uniform cooling. The von Mises yield criterion was employed:σvon=12[(σ1−σ2)2+(σ2−σ3)2+(σ3−σ1)2]σvon=21[(σ1−σ2)2+(σ2−σ3)2+(σ3−σ1)2]
where σ1,σ2,σ3σ1,σ2,σ3 are principal stresses.
4.2 Simulation of a Stress Frame
A sand-cast stress frame (material: ZG25 steel) was analyzed to study stress evolution. ANSYS simulations captured transient thermal gradients and stress redistribution (Table 3).
Table 3: Stress evolution in ZG25 stress frame
Time (s) | Max. Tensile Stress (MPa) | Max. Compressive Stress (MPa) |
---|---|---|
1000 | 151 | -148 |
4500 | 74 | -72 |
Results aligned with ProCAST predictions, validating the feasibility of coupling both tools for multi-physics analysis.
5. Integration of ProCAST and ANSYS
A workflow was proposed to transfer residual stresses from ProCAST to ANSYS for structural analysis (Figure 2). Key steps include:
- Mesh Compatibility: Convert ProCAST tetrahedral elements to ANSYS SOLID185 elements.
- Stress Mapping: Extract nodal stress components from ProCAST results and map them to ANSYS.
- Validation: Compare stress distributions in critical regions (e.g., riser junctions).
Table 4: Node stress comparison between ProCAST and ANSYS
Node ID | ProCAST σxσx (MPa) | ANSYS σxσx (MPa) | Error (%) |
---|---|---|---|
61221 | -179.3 | -182.1 | 1.5 |
5902 | -175.8 | -173.9 | 1.1 |
6. Conclusions and Future Work
Numerical simulation technologies significantly enhance the precision and efficiency of sand casting processes. Key achievements include:
- ProCAST-enabled optimization of riser design for the QT450-10 flywheel, reducing defects by 70%.
- ANSYS-based stress analysis validated the thermo-elastoplastic model for ZG25 steel.
- A framework for integrating ProCAST and ANSYS was established, enabling coupled thermo-mechanical analysis.
Future work will focus on:
- Microstructure simulation to predict mechanical properties.
- Development of a unified material database for sand casting alloys.
- Enhanced interface algorithms for seamless ProCAST-ANSYS integration.
This study underscores the transformative potential of numerical simulation in advancing sand casting technology, offering a pathway to sustainable and high-quality manufacturing.