Sand casting remains a cornerstone of modern manufacturing for complex metal components, accounting for approximately 44% of global casting production. This paper presents an innovative automated horizontal parting molding line designed to address persistent challenges in traditional sand casting processes, including unstable mold positioning, low equipment recycling rates, and labor-intensive operations. Our system integrates advanced mechanical design with PLC-controlled automation to optimize production efficiency while maintaining 99.4% product qualification rates.
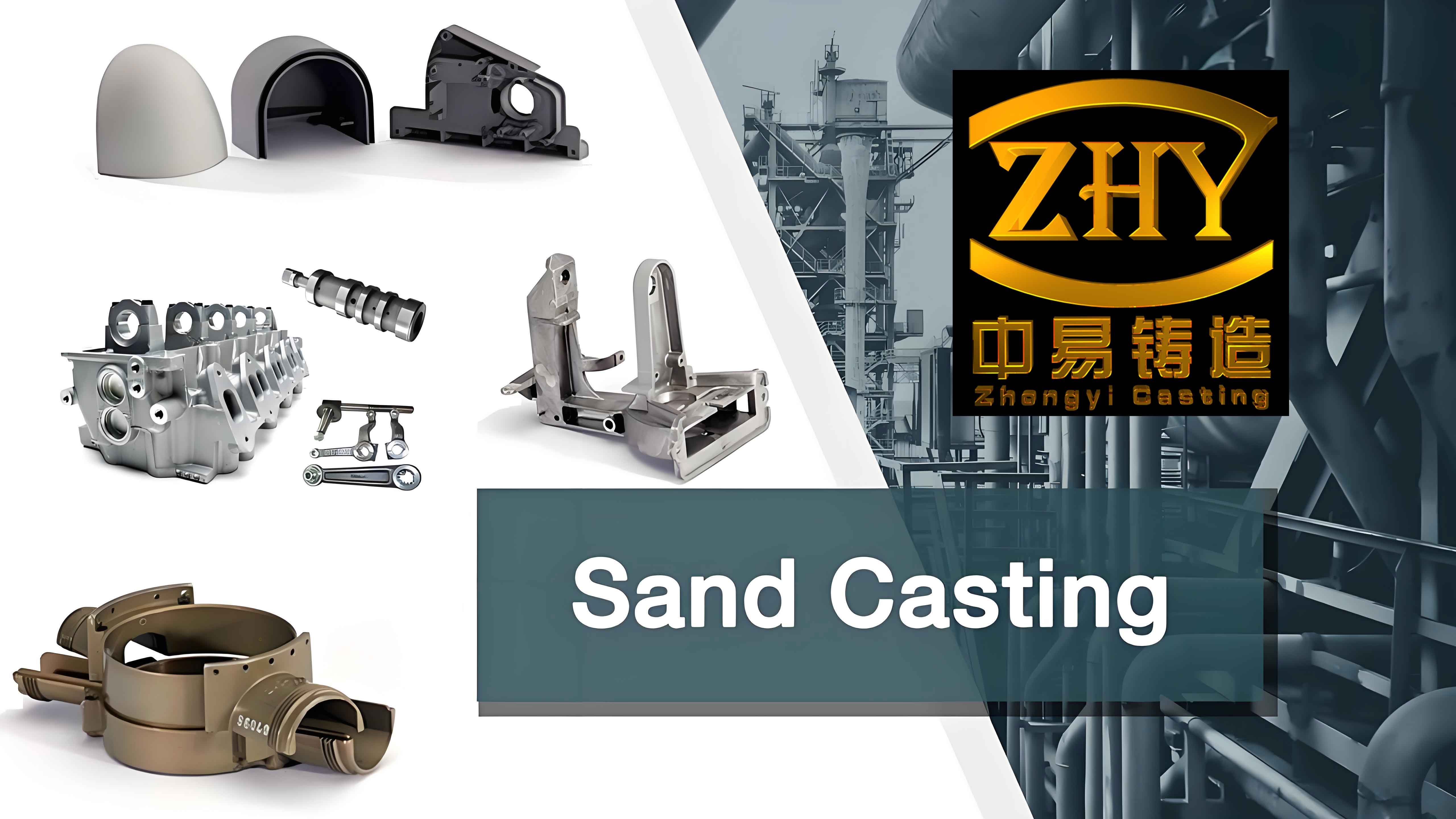
1. System Architecture and Workflow
The automated sand casting production line comprises four primary conveyor systems:
$$ \text{Production Throughput} = \frac{N_{\text{molds}} \times t_{\text{cycle}}}{60} $$
Where \( N_{\text{molds}} \) represents simultaneous mold processing capacity and \( t_{\text{cycle}} \) denotes the complete production cycle time in minutes. Key components include:
Component | Function | Technical Parameters |
---|---|---|
Molding System | Simultaneous upper/lower sand shooting | 32 mL/r pump capacity, 2400 rpm servo motor |
Flask Transfer Unit | Precision positioning | ±0.5 mm repeatability |
Sand Recovery | Closed-loop material reuse | 98% recycling efficiency |
2. Critical Mechanisms Design
The horizontal parting molding line incorporates three revolutionary mechanisms for sand casting optimization:
2.1 Flask Clamping System
The dual-gear clamping mechanism ensures precise mold positioning:
$$ F_{\text{clamp}} = \frac{\tau_{\text{gear}} \times r_{\text{pitch}}}{d_{\text{flask}}} $$
Where \( \tau_{\text{gear}} \) represents gear torque and \( r_{\text{pitch}} \) denotes pitch radius.
Parameter | Value |
---|---|
Clamping Force | 12 kN ±5% |
Positioning Accuracy | ≤0.3 mm |
Cycle Time | 8 s |
2.2 Flask-Press Conversion Unit
This subsystem enables 100% reusable flask utilization through coordinated pneumatic control:
$$ v_{\text{lift}} = \frac{Q_{\text{air}} \times \eta_{\text{cyl}}}{A_{\text{piston}}} $$
Where \( Q_{\text{air}} \) is airflow rate and \( \eta_{\text{cyl}} \) represents cylinder efficiency.
3. Automated Control System
The PLC-based control architecture features distributed I/O modules and real-time monitoring:
PLC Component | Specification |
---|---|
Main CPU | Mitsubishi FX5U-80MT |
I/O Modules | AJ65SBTB1-16D (Input), AJ65SBTB2N-16R (Output) |
Network Protocol | CC-Link IE Field |
4. Production Performance Analysis
Comparative data demonstrates significant improvements in sand casting operations:
Metric | Manual Process | Automated Line | Improvement |
---|---|---|---|
Labor Requirement | 32 operators | 4 technicians | 87.5% reduction |
Floor Space | 87.3% area utilized | 65.2% area utilized | 22.1% reduction |
Output Capacity | 28.8 tons/day | 46.4 tons/day | 61.1% increase |
The automated sand casting line achieves 640 wheel hubs and 1,040 clutch components daily production with 16-hour continuous operation. The closed-loop sand recovery system maintains material utilization efficiency at:
$$ \eta_{\text{sand}} = \left(1 – \frac{m_{\text{waste}}}{m_{\text{total}}}\right) \times 100\% = 98.2\% $$
5. Technological Advancements
Key innovations in sand casting automation include:
- Adaptive mold thickness adjustment (280-560 mm range)
- Multi-stage vibration degating system
- Intelligent pouring temperature control (±15°C)
These advancements enable the system to handle diverse sand casting applications while maintaining dimensional accuracy of:
$$ \sigma_{\text{dim}} \leq 0.5\% \text{ of nominal size} $$
6. Conclusion
The developed automated horizontal parting molding line revolutionizes traditional sand casting processes through:
- 62% increase in production efficiency
- 99.4% product qualification rate
- Full flask/press recycling capability
This system establishes a new benchmark for sustainable, high-precision sand casting production, particularly suitable for automotive components and industrial machinery parts. Future developments will integrate AI-based quality prediction models to further enhance process reliability.