As castings manufacturers across Europe confront unprecedented headwinds, the European Foundry Industry Sentiment Indicator (FISI) reveals alarming trends. June 2023 recorded FISI at 98.6 points – a 2.1-point decline from May and below its 2015 baseline of 100.0. This marks the fourth consecutive monthly deterioration, signaling deepening distress. Order backlogs are shrinking as new orders collapse across multiple sectors, with no immediate recovery anticipated. The Business Climate Indicator (BCI) mirrors this pessimism, dropping to 0.06 points – nearing pandemic-era lows observed in late 2020. For castings manufacturers, this translates to declining production volumes, shrinking order books, and falling price expectations over the coming months.
The FISI methodology aggregates monthly assessments from CAEF members regarding current conditions and six-month forecasts. Meanwhile, the European Commission’s BCI incorporates five weighted components:
$$ \text{BCI} = w_1(\text{Production}) + w_2(\text{Orders}) + w_3(\text{Export Orders}) + w_4(\text{Inventory}) + w_5(\text{Production Expectations}) $$
Recent performance across these dimensions shows uniform deterioration:
Indicator | May 2023 | June 2023 | Δ (Points) |
---|---|---|---|
FISI | 100.7 | 98.6 | -2.1 |
BCI | 0.19 | 0.06 | -0.13 |
New Orders Index | -8.2 | -12.7 | -4.5 |
Price Expectations | 1.3 | -0.8 | -2.1 |
Material-specific analyses reveal that both ferrous and non-ferrous foundries now report negative assessments – a convergence of decline previously masked by statistical base effects. For castings manufacturers, this environment necessitates radical operational innovations to maintain viability.
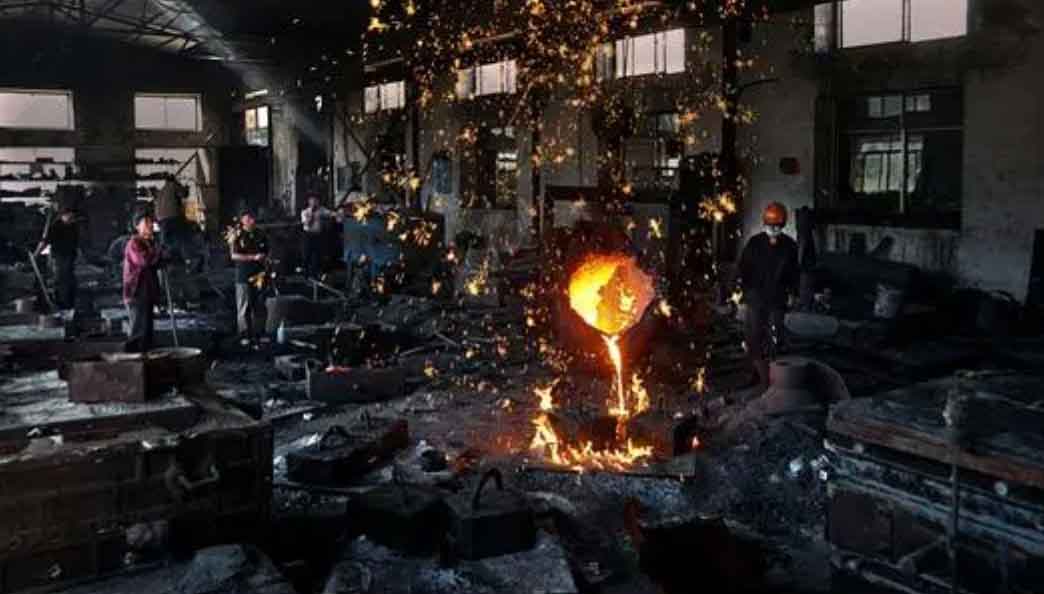
RESAND’s modular reclamation technology exemplifies such innovation. Deployed at Raahe Valimo Oy – a Finnish steel foundry established in 1919 – this system combines thermal and mechanical treatment to regenerate spent foundry sand. Before implementation, producing 1,000 tonnes of steel castings required 2,500 tonnes of virgin silica sand, mostly imported from Belgium. Post-consumption disposal posed critical challenges:
$$ \text{Annual Waste} = \text{Production} \times \rho_{\text{sand}} \times (1 – R_{\text{reclaim}}) $$
Where \( \rho_{\text{sand}} = 2.5 \) tonnes sand/tonne casting and \( R_{\text{reclaim}} = 0\% \).
Since adopting RESAND in 2023, Raahe Valimo demonstrates how castings manufacturers can transform waste streams. Operational data confirms:
Parameter | Pre-RESAND | Post-RESAND | Improvement |
---|---|---|---|
Virgin Sand Consumption | 2,500 tonnes | 300 tonnes | -88% |
Landfill Waste | 2,200 tonnes | 0 tonnes | 100% reduction |
Binder Requirements | 100% baseline | ≈82% baseline | -18% |
Particle Size Distribution | Broad dispersion | Tighter distribution | ↑ Consistency |
The regeneration process follows distinct phases:
- Thermal Treatment: Combusts organic residues at controlled temperatures
- Mechanical Reclamation:
$$ \text{Reclamation Efficiency} = 1 – e^{-k \cdot t} $$
Where \( k \) = material constant, \( t \) = processing time - Classification: Granulometric separation to ensure optimal AFS fineness
For castings manufacturers like Raahe Valimo, on-site reclamation eliminates logistical vulnerabilities while enhancing technical control. The economic advantage becomes evident when calculating savings:
$$ \text{Annual Savings} = C_v \cdot Q_s – (C_r \cdot Q_s + F_{\text{fixed}}) $$
Where \( C_v \) = virgin sand cost/tonne, \( C_r \) = reclamation cost/tonne, \( Q_s \) = annual sand volume, and \( F_{\text{fixed}} \) = installation depreciation.
With European silica sand prices ranging €80-120/tonne, RESAND achieves payback within 18-24 months while permanently reducing variable costs by 60-70%. For castings manufacturers navigating FISI’s decline, such technologies provide crucial resilience against both economic pressures and regulatory constraints like landfill prohibitions.
The sand reclamation process directly enhances casting quality parameters. Controlled grain distribution improves permeability and reduces gas defects:
$$ P_{\text{new}} = \frac{D_{10}^2 \cdot \phi}{\mu \cdot L} $$
Where \( P \) = permeability, \( D_{10} \) = effective grain size, \( \phi \) = porosity, \( \mu \) = viscosity, \( L \) = path length. Tighter particle distribution elevates \( D_{10} \) consistency by 15-20% compared to virgin sands.
European castings manufacturers must now balance cyclical challenges with structural innovation. While FISI and BCI data suggest prolonged difficulties, pioneers like Raahe Valimo demonstrate how operational reinvention can concurrently address economic, environmental, and technical imperatives. As RESAND’s deployment expands across German and Finnish foundries, it establishes a replicable template for transforming waste liabilities into competitive advantages – a necessity in an industry where sentiment indicators show no imminent recovery.