The cylinder head is one of the main components of the diesel engine. The diesel engine ,The maximum temperature in the combustion chamber during engine operation can reach about 2 000 K(about 1 700 ℃), the cylinder head not only withstands the high temperature brought by the combustion chamber cyclic thermal shock load and the impact of high pressure circulation in the combustion chamber Loads, especially towards the high pressure side and inside the valve seat hole, are not allowed to have cast Manufacturing defects; the oil pipe holes and fuel injection holes on the cylinder head have a harsh working environment. Poor, the internal structure must be dense, so the cylinder head casting itself The internal and external quality requirements are relatively high, and the casting structure is shown in Figure 1.
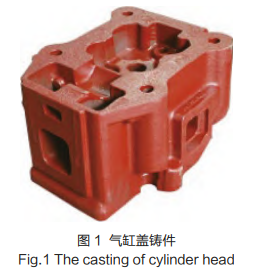
The material of the 16V190 cylinder head casting is RuT300, which has excellent
Its mechanical properties, thermal fatigue resistance and good air tightness are not affected by
It affects the cooling effect of water flow in the water cavity of the cylinder head, requiring the inside of the water cavity to be smooth and smooth.
Burrs, the wall thickness between the water cavity and the air channel must be controlled at 6~8 mm.
The overall dimensional accuracy of the parts is controlled at CT10~CT11 level.
The entire cylinder head mold is molded using resin sand machines, and the mold design is
2 pieces/type, some sand cores are handmade with resin sand, water cavity core,The bolt hole core is made of hot core box coated sand core. Because the cylinder head is cast ,There are many curved surfaces in the inner cavity of the piece and the structure is relatively complex. The sand core is designed to accumulate in the process. 22 items. The casting mold is spray-coated with water-based paint and dried in a drying oven.The drying and holding temperature is 170 ℃ ±10 ℃, and the holding time is 3.5~4 h.The sand core is spray-coated using a composite process of alcohol-based quartz coating and water-based graphite coating.During the assembly process, the sand core adopts the method of stacking the core in layers.Apply caster’s glue to the jointing surface, and put it into a drying oven to dry after the assembly is completed. gas The weight of the cylinder head casting is 89 kg/piece, and the local wall thickness of the casting is only 6 mm.The process requires that the pouring and filling of molten iron must be rapid and smooth, so a stepped The pouring system has a pouring temperature of 1 380 ~ 1 390 ℃ and a controlled pouring time.Set in 15~20 s.
1 Analysis of causes of casting defects
The 16V190 cylinder head is prone to blisters and blisters during the casting production process.
Typical defects such as insufficient pouring, inner cavity burrs, and pores are the main causes of these casting defects.
The reasons for this are explained in detail below.
1.1 Trachoma
The blisters in 16V190 cylinder head castings are caused by cleaning the castings.
Unnecessary holes are found inside or on the surface of the casting. Mostly produced
Blisters in raw castings are mainly caused by improper operation during the mold assembly and box closing process. bolt The hole core is not installed in place, the bolt hole core is not perpendicular to the bottom surface of the lower core, and when closing the box The crane lifting the mold is not stable, which will cause the mold to rise during the box closing operation.The mold breaks the bolt hole core, causing the sand core to break and fall into the mold cavity, making it difficult to inspect.
This causes blisters to appear in the casting after subsequent pouring (Figure 2). In addition, the upper water chamber A separate sand core is used with the injector hole core, which is bonded with caster glue and lowered as a whole.Core and sand core bonding will inevitably have some accumulated errors; at this time, if there is floating sand or paint accumulation in the injector hole core seat, the core will not be in place, and in addition During the box closing process, if the stability of the upper type lifting is not well controlled, it will also cause problems during the box closing process.The sand core is broken or crushed during the process, resulting in sand falling out, which also causes casting after pouring.Trachoma defects occur locally in the parts (Figure 3).
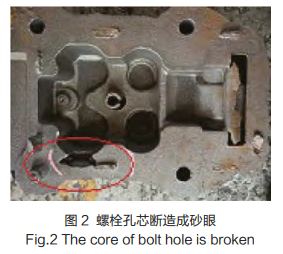
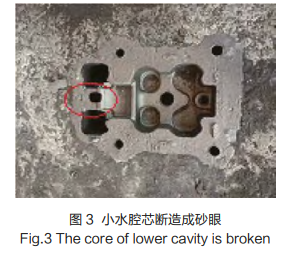
1.2 Inner cavity burrs
The inner cavity burr defect of 16V190 cylinder head casting refers to the air path, water
There is an irregular layer of varying thickness on the road or other parts that looks like “thin iron”
Something like “skin”. There are two main possible reasons for the formation of burrs in the inner cavity.
Yes, they are:
(1) Since the structure of the cylinder head water chamber is relatively complex, the water chamber
The structural sand core is made using the hot box core shooting process, but the coated sand softens when heated ,It is easy to form a shrinkage problem , resulting in a thin crust layer of the sand core, and the sand core in the natural Shrinkage during the cooling process will produce capillary cracks. During the pouring process of molten iron, the sand core It will crack after being exposed to high-temperature thermal radiation from the molten iron, allowing the molten iron to penetrate into the sand core.Different degrees of burrs are formed.
(2) Due to the complicated structure of the cylinder head water cavity, the partial wall of the inner cavity The thickness is only 6 mm, and the air intake core and exhaust core need to be interspersed with the water cavity core.As a result, the water cavity core is divided into two sand cores during process design (Figure 4, Figure 5) In the later stage, the two sand cores will be bonded with caster glue based on actual conditions. This will cause the bonding surfaces of the two sand cores to not fit closely enough, increasing the possibility of molten iron infiltration.
possibility, leading to an increased probability of burrs appearing in the inner cavity.
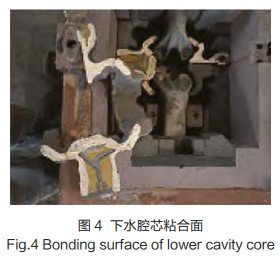
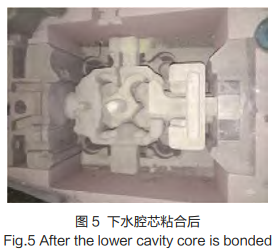
1.3 Insufficient watering
The main reason for the insufficient pouring defect of 16V190 cylinder head casting is
Because there is a phenomenon of molten iron overflowing at the parting surface during the pouring process, that is, a leaky box [3],In addition, it is also affected by the purity of the molten iron, the pouring temperature, and the placement of the filter.Whether it is correct, and the impact of air holes causing leakage of molten iron, see Figure 6.
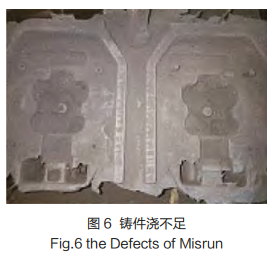
1.4 pores
The main cause of pore defects in 16V190 cylinder head castings is the use of resin self-hardening sand to mold the core, and the resin and curing agent in the molding sand.A large amount of gas will be produced under the heat of high-temperature molten iron. During the pouring process As the molten iron is drawn into the inside of the mold, the gas inside the mold will eventually be unable to flow smoothly.discharge, causing pores to appear after the casting is cooled and formed, and most of the pores are invasion Entrance stomata (Fig. 7).
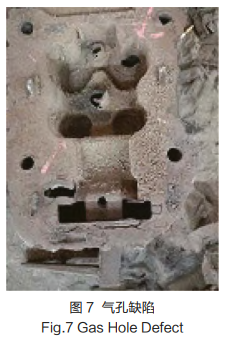
2 Improvement measures and effects
2.1 Measures to improve trachoma defects
(1) Make a core clamping board based on the actual situation to ensure that the sand core can be lowered into the position, the cylinder head actually adopts the core casting process. According to the sand core casting process,The actual production of the lower core pallet, especially the coordination involving the height direction of the sand core A height confirmation card board must be made on the surface to reduce the accumulated error of sand core setting, so as to Prevent the upper mold from breaking the bolt hole core and related sand core during the box closing process, and avoid sand
The core broke during core setting.
(2) Combined with the casting structure to produce the inner cavity wall thickness caliper and 6 mm soft Leather lines, regular wall thickness dimensions are checked with wall thickness calipers, irregularities such as airways For the curved wall thickness, use a soft leather thread as a check feeler gauge to pass through the curved wall.The cavity ensures the minimum wall thickness in the curved area, thereby ensuring that the inner cavity is The sand core is lowered in place to prevent the sand core from being crushed during the box closing process.
(3) Conduct regular quality awareness training to improve the quality of workers Be aware of quantity, and check the floating sand or accumulated paint in the core seat one by one during the core setting process.Clean it in place. After setting the core, check and verify the verticality of the bolt hole core one by one.During the boxing process, a dedicated person will check whether there is any collision between the bolt hole core and the upper core seat.Wipe to ensure that the box closing is smooth and prevent the upper mold from crushing the bolt hole core and crushing the sand core.phenomenon occurs.
2.2 Measures to improve inner cavity burr defects
(1) In order to prevent the occurrence of burrs in the inner cavity of castings, efforts should be made to improve the quality of the water cavity core sand core itself and control process parameters such as core shooting temperature and holding time.Number, ensure that the thickness of the sand core crust layer is >5 mm, and use Alcohol-based zircon powder coating is dipped twice to improve the density of the sand core surface properties, refractoriness and strength.
(2) Strengthen the quality control of the details of the water cavity core to ensure that the water cavity core The core is in place. When setting the core, first perform a trial fitting of the upper and lower water cavity sand cores.Check the matching of the mating surfaces, and match the two sand cores according to the shape of each part.The surfaces should be trimmed appropriately to make the fit smooth, and the gap between the mating surfaces should be controlled to a minimum.Secondly, when lowering the upper water cavity core, first wind the mating surface of the lower water cavity core.
Open the exhaust groove, apply a layer of caster glue evenly, and then close the upper sheet water
cavity core, apply a little pressure to squeeze the caster glue to both sides, take out the upper core and check Check the adhesion of the two sand cores, scrape off the excess caster glue, and finally check the adhesion If it is not tight enough, use caster’s glue to repair it appropriately, and then close the upper sand sheet again. core and pressurized to ensure that the mating surfaces of the two sand cores are tight enough to reduce the molten iron The possibility of penetrating into the sand core and reducing the burrs in the water cavity.
2.3 Measures to improve the defect of insufficient pouring
(1) Prevent box leakage during pouring. First check during the styling process
The sand box and other tooling conditions are not used. Missing or loose sand boxes are not used to prevent The casting mold is sunk as a whole, and then the sprue is avoided around the parting surface of the lower mold before closing the box.Place ϕ4 mm sealing mud strips, and when tightening the box clamps into the mold, they need to be diagonally aligned at the same time Tighten to ensure uniform stress on the mold.
(2) Control the quality of molten iron and the quality of the pouring process. During pouring
On the one hand, it is necessary to control the quality of the raw molten iron and do a good job in removing and removing slag, and on the other hand,On the one hand, it is necessary to strengthen the slag blocking operation during the pouring process. The pouring ladle nozzle must be connected during pouring.Close to the sprue cup, quickly fill the sprue cup, maintain the liquid level in the sprue cup, and avoid During the filling process, turbulence, eddy currents and even splashes are generated to prevent
The flow interruption causes the molten slag to block the filter holes.
(3) Make sure the ceramic filter is placed correctly. During process design, in At the overlap between the sprue and the lateral runner of the pouring system, place a ceramic filter to It plays the role of slag blocking [3]. When placing the ceramic filter, it must be ensured that the inflow hole faces Hold the sprue cup to ensure that the molten iron flows through the filter holes and into the mold.
(4) Control the ventilation holes, air holes, etc. to be clear and ensure that post-processing is in place.
Ensure that the air passages in the sand mold and sand core are clear and ensure that the sand core is properly ventilated during the mold matching process.When making air holes, the air holes should be reserved on the upper mold as much as possible, and the air holes should be reserved as much as possible.Necessary sealing should be done around it to prevent molten iron from entering the vent hole and causing leakage.
(5) Control the pouring temperature. During the cylinder head pouring process, start pouring
The pouring temperature is controlled according to the upper limit of the process (1 390 ℃), and the molten iron in the pouring ladle is Take good insulation measures and cover with appropriate insulation materials. The pouring process should be smooth, orderly and rapid, and try to ensure that the pouring temperature in the later stages of pouring is within the range of process requirements.
2.4 Measures to improve stomata defects
(1) Improve the process and rationally design the pouring system. When designing process
Ensure that the design of the inner runner is conducive to the principles of smooth filling of the molten iron and smooth gas floating. The design of risers, gas holes, etc. must be in correct positions and reasonable in number, so that the gas in the mold can be smoothly discharged from the mold cavity.
(2) Control the exhaust effect of the sand core. Sand core is blocked before dipping
Air channel holes to prevent paint from blocking the air channels during dipping. In addition, open up all the air channels in the sand core head and the air channel holes that were blocked before dipping, and extend to the thick part of the sand core. Pour out the sand core and crush it. Sand to make the sand core airway smooth.
(3) Do a good job of ventilating the sand core and mold. According to the type before core setting
At the position of the core head of the sand core in the cavity, open a vent hole from the outside of the mold to the core seat. Apply caster’s glue inside the core seat to block the gap between the core head. Bypass the vent hole and apply caster’s glue around it to prevent molten iron from entering during the pouring process. The air passage blocks the air passage so that the gas generated in the sand core cannot be smoothly discharged from the mold. In summary, by taking corresponding improvement measures, the actual production process effectively avoided the occurrence of defects such as blisters, inner cavity burrs, insufficient pouring, and pores in the 16V190 cylinder head castings. The scrap rate of the cylinder head castings dropped from the original 3.8% to 0.8%, achieving good implementation results.
3 Conclusion
In view of the typical casting defects such as blisters, inner cavity burrs, insufficient pouring, and pores in the cylinder head, the causes of related problems were analyzed based on the actual situation, and corresponding solutions were taken to effectively improve the quality of the cylinder head castings and cylinders. Cover casting scrap rates dropped by 3%. In view of the detailed quality control in the cylinder head casting production process, which has a direct impact on the quality of the cylinder head castings, combined with production experience and practice, the corresponding casting process should be reasonably designed and improved, and the on-site operation requirements should be standardized.
Relevant measures are formulated and implemented to greatly reduce the amount of scrapped castings, improve production efficiency, and reduce production costs.