Abstract
Investment casting, as an advanced casting method, has been widely applied in the aerospace, automotive, and medical fields due to its ability to produce complex-shaped and high-precision castings. In this study, a numerical simulation was conducted to investigate the thin-walled frame titanium alloy investment casting process. The ProCAST software was utilized to establish a three-dimensional numerical model, which simulated the filling, solidification, and cooling processes of the casting. By analyzing the simulation results, the temperature field, flow field, and stress field within the casting system were comprehensively evaluated. Additionally, potential casting defects such as shrinkage pores, cold shuts, and hot tears were predicted and discussed. To verify the accuracy of the simulation, physical experiments were conducted, and the experimental results were compared with the simulation outcomes. The study provides a theoretical basis and practical guidance for optimizing the thin-walled frame titanium alloy investment casting process and improving casting quality.
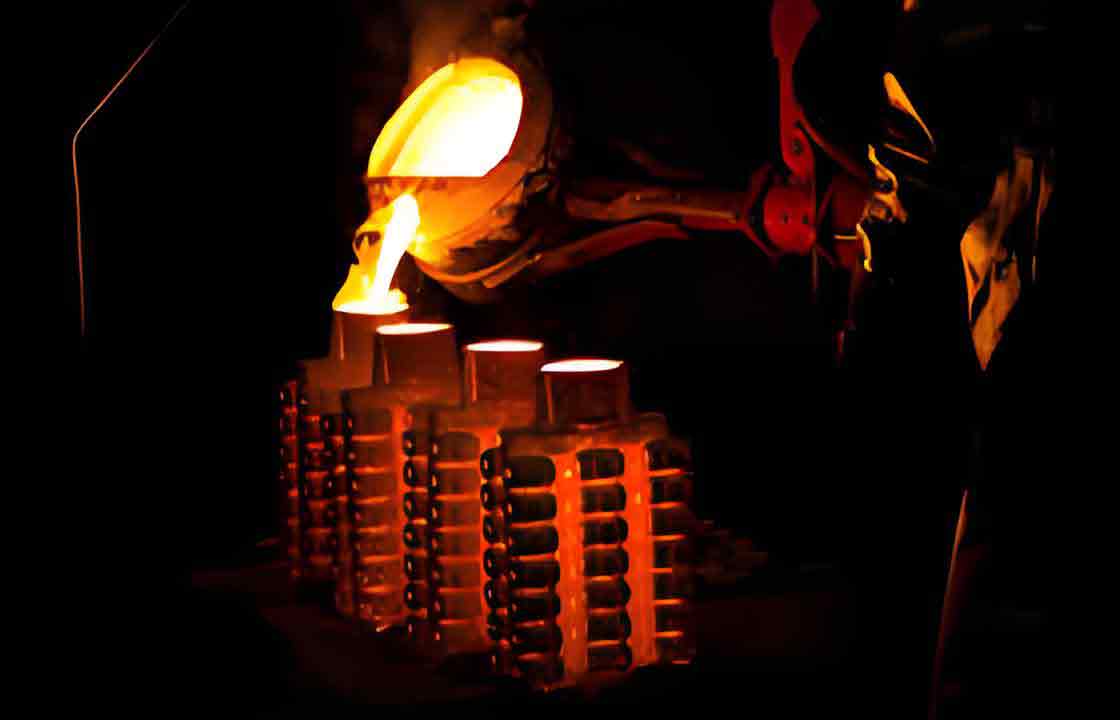
1. Introduction
Investment casting, also known as the lost-wax process, is a precision casting technique that utilizes a wax pattern to create a mold for the final casting. This method excels in producing complex geometries, fine details, and near-net-shape components, making it ideal for applications in the aerospace, automotive, and medical industries. Titanium alloys, known for their high strength-to-weight ratio, excellent corrosion resistance, and good biocompatibility, are frequently used in these fields.
However, the investment casting of thin-walled titanium alloy components presents significant challenges. The thin walls lead to rapid heat dissipation, which can cause premature solidification and defects such as cold shuts and hot tears. Furthermore, the high reactivity of titanium with common mold materials requires special attention to avoid contamination and ensure casting integrity.
To address these challenges, numerical simulation has emerged as a powerful tool for predicting and optimizing the investment casting process. By simulating the filling, solidification, and cooling stages, potential defects can be identified early, and process parameters can be adjusted accordingly to improve casting quality.
In this study, a comprehensive numerical simulation of the thin-walled frame titanium alloy investment casting process was conducted using the ProCAST software. The simulation results were analyzed to evaluate the temperature field, flow field, and stress field within the casting system. Potential casting defects were predicted, and their formation mechanisms were discussed. To validate the simulation results, physical experiments were performed, and a comparison between the experimental and simulation outcomes was presented.
The objectives of this study are as follows:
- To establish a three-dimensional numerical model for the thin-walled frame titanium alloy investment casting process using ProCAST.
- To simulate and analyze the filling, solidification, and cooling processes of the casting.
- To predict potential casting defects and discuss their formation mechanisms.
- To validate the simulation results through physical experiments and provide guidance for optimizing the casting process.
2. Literature Review
2.1 Investment Casting Process
Investment casting involves several key steps, including pattern making, mold preparation, wax pattern assembly, dipping and coating, dewaxing, shell firing, pouring, and casting cleanup. The wax pattern is first created using a three-dimensional printing or injection molding process. This pattern is then assembled onto a sprue system, which will direct molten metal into the mold cavities during the pouring stage.
The assembled wax pattern is dipped into a ceramic slurry and coated with a refractory material to form a mold shell. After multiple dipping and coating cycles, the mold shell becomes sufficiently thick to withstand the high temperatures and pressures encountered during the pouring and solidification stages. The wax pattern is then removed through a dewaxing process, leaving behind a hollow mold cavity.
The mold shell is fired to burn out any residual wax and to strengthen the shell. Molten metal is then poured into the mold cavity through the sprue system, where it fills the cavity and solidifies to form the casting. After cooling, the mold shell is removed, and the casting is cleaned and finished to meet the desired specifications.
2.2 Numerical Simulation of Investment Casting
Numerical simulation has been widely applied in the investment casting industry to predict and optimize the casting process. Various software tools, such as ProCAST, MagmaSoft, and FLOW-3D, have been developed to simulate the filling, solidification, and cooling stages of the casting process.
The filling stage involves the flow of molten metal into the mold cavity. Numerical simulations can predict the flow patterns, velocity distributions, and pressure variations within the casting system. This information is crucial for identifying potential defects such as cold shuts and misruns, which can occur due to inadequate metal flow or premature solidification.
The solidification stage follows the filling stage, during which the molten metal cools and solidifies to form the casting. Numerical simulations can predict the temperature distributions and solidification sequences within the casting. This information is important for identifying potential defects such as shrinkage pores and hot tears, which can occur due to uneven cooling rates or high stress concentrations.
The cooling stage involves the continued cooling of the casting after solidification. Numerical simulations can predict the residual stress distributions and distortion patterns within the casting. This information is useful for understanding the post-casting behavior of the component and for designing suitable fixtures or supports to minimize distortion during cooling.
2.3 Thin-Walled Titanium Alloy Castings
Thin-walled titanium alloy castings are characterized by their light weight, high strength, and excellent corrosion resistance. However, the production of these castings presents several challenges. The thin walls lead to rapid heat dissipation, which can cause premature solidification and defects such as cold shuts and hot tears. Furthermore, the high reactivity of titanium with common mold materials requires special attention to avoid contamination and ensure casting integrity.
To address these challenges, various strategies have been proposed, including the use of special mold materials, the optimization of process parameters, and the application of advanced casting techniques such as vacuum investment casting and centrifugal casting. However, the successful production of thin-walled titanium alloy castings often relies on a combination of these strategies, as well as extensive experimentation and optimization.
3. Methodology
3.1 Geometry and Mesh Generation
The geometry of the thin-walled frame titanium alloy casting was created using a computer-aided design (CAD) software. The casting features a complex thin-walled frame structure with a variety of hole sizes and positions. To accurately simulate the casting process, a high-fidelity three-dimensional model was created, including the sprue system, runner system, and gating system.
The mesh generation process involved discretizing the continuous geometry into a finite number of elements, which form the computational domain for the numerical simulation. A hybrid mesh was used, combining tetrahedral and hexahedral elements to balance computational efficiency and accuracy. The mesh size was refined in critical areas such as the thin walls, gates, and runners to capture the detailed flow and solidification behavior.
3.2 Material Properties
The material properties of the titanium alloy and mold materials were input into the ProCAST software. These properties included the density, specific heat capacity, thermal conductivity, latent heat of fusion, and solidus and liquidus temperatures. The material properties were obtained from published literature and manufacturer datasheets, and they were verified through experimental measurements when possible.
3.3 Boundary Conditions
The boundary conditions for the numerical simulation were defined based on the actual casting process. The initial temperature of the mold was set to room temperature, and the pouring temperature of the molten titanium alloy was specified. The heat transfer coefficients between the molten metal and mold materials, as well as between the mold and the surrounding environment, were estimated based on previous research and experimental data.
3.4 Simulation Setup
The ProCAST software was used to set up the numerical simulation. The filling, solidification, and cooling stages of the casting process were simulated sequentially. The filling stage was simulated using the volume of fluid (VOF) method to track the interface between the molten metal and mold materials. The solidification stage was simulated using the enthalpy method to capture the phase change behavior. The cooling stage was simulated using the finite element method to predict the residual stress distributions and distortion patterns.
4. Results and Discussion
4.1 Filling Process Simulation
The filling process simulation provided insights into the flow patterns and velocity distributions within the casting system. The molten titanium alloy was observed to flow smoothly through the sprue system and into the mold cavity. However, in some areas of the thin-walled frame, the flow velocity was relatively low, indicating potential areas for cold shuts.
To further analyze the filling process, the flow front progression was monitored over time. The flow front advanced rapidly through the thicker sections of the casting but slowed down significantly in the thin-walled areas. This behavior was attributed to the rapid heat dissipation in the thin walls, which caused the molten metal to solidify prematurely.
To mitigate the risk of cold shuts, the gate and runner design was optimized. By increasing the gate size and runner diameter, the flow velocity in the thin-walled areas was improved, and the risk of premature solidification was reduced.
4.2 Solidification Process Simulation
The solidification process simulation predicted the temperature distributions and solidification sequences within the casting. The temperature field was observed to evolve rapidly during the initial stages of solidification, with the molten metal cooling rapidly in the thin-walled areas. As solidification progressed, the temperature gradients became more pronounced, with the hottest regions located near the gates and runners.
To analyze the solidification behavior in more detail, the solidification fraction was monitored over time. The solidification fraction increased rapidly in the thicker sections of the casting but more slowly in the thin-walled areas. This behavior was attributed to the higher heat dissipation rates in the thin walls, which delayed the solidification process.
Potential casting defects such as shrinkage pores and hot tears were predicted based on the solidification simulation results. Shrinkage pores were predicted to form in areas with high solidification rates and low feeding potential, such as the intersections of thin walls. Hot tears were predicted to form in areas with high stress concentrations and low ductility, such as the corners of the thin-walled frame.
To mitigate these defects, the casting design was optimized. By increasing the wall thickness in critical areas and modifying the gating system to improve feeding, the risk of shrinkage pores and hot tears was reduced.
4.3 Cooling Process Simulation
The cooling process simulation predicted the residual stress distributions and distortion patterns within the casting. The residual stresses were observed to be highest in areas with large temperature gradients and high cooling rates, such as the thin walls near the gates and runners. The distortion patterns were found to be influenced by the residual stresses, with the casting tending to warp or bow away from the regions of high stress.
To minimize the residual stresses and distortion, the cooling conditions were optimized. By adjusting the mold material and heat transfer coefficients, the cooling rates were controlled to promote more uniform solidification and reduce temperature gradients. Additionally, support structures were designed to constrain the casting during cooling and minimize distortion.
4.4 Casting Defect Prediction and Mitigation
Based on the simulation results, potential casting defects such as cold shuts, misruns, shrinkage pores, hot tears, and distortion were predicted. The formation mechanisms of these defects were discussed, and strategies for mitigation were proposed.
Cold shuts and Misruns: These defects occur due to inadequate metal flow or premature solidification. To mitigate these defects, the gate and runner design was optimized to improve metal flow and reduce heat dissipation in the thin-walled areas.
Shrinkage Pores: These defects form in areas with high solidification rates and low feeding potential. To mitigate shrinkage pores, the casting design was optimized by increasing wall thickness in critical areas and modifying the gating system to improve feeding.
Hot Tears: These defects occur in areas with high stress concentrations and low ductility. To mitigate hot tears, the casting design was optimized by rounding sharp corners and reducing wall thickness variations.
Distortion: This defect is caused by residual stresses developed during cooling. To minimize distortion, the cooling conditions were optimized to promote more uniform solidification and reduce temperature gradients. Additionally, support structures were designed to constrain the casting during cooling.
5. Experimental Validation
5.1 Casting Preparation
To validate the simulation results, physical experiments were conducted using the optimized casting design and process parameters. The titanium alloy was melted in a vacuum induction furnace and poured into the investment mold at the specified pouring temperature. The mold was then allowed to cool, and the casting was removed and cleaned.
5.2 Microstructural Analysis
Microstructural analysis was performed on the castings to evaluate the solidification behavior and defect formation. Samples were taken from various locations within the castings, and they were mounted, polished, and etched to reveal the microstructure.
The microstructural analysis revealed that the solidification sequence was consistent with the simulation results. The grain structures were found to be finer in the thin-walled areas due to the rapid cooling rates, while they were coarser in the thicker sections. Additionally, no significant defects such as shrinkage pores or hot tears were observed in the microstructures.
5.3 Dimensional Accuracy Measurement
Dimensional accuracy measurements were performed on the castings to evaluate the impact of distortion. The castings were compared to the original CAD models, and the deviations were measured using a coordinate measuring machine (CMM).
The dimensional accuracy measurements revealed that the castings were within the specified tolerances. The deviations were relatively small, indicating that the optimization strategies for minimizing distortion were effective.
5.4 Mechanical Testing
Mechanical testing was performed on the castings to evaluate their strength and ductility. Tensile tests were conducted according to ASTM standards, and the results were compared to the material properties of the titanium alloy.
The mechanical testing revealed that the castings exhibited good strength and ductility. The tensile strength and elongation at break were found to be within the expected ranges for the titanium alloy. This indicates that the investment casting process was successful in producing high-quality thin-walled titanium alloy castings.
5.5 Comparison with Simulation Results
A comparison between the experimental results and simulation outcomes was conducted to validate the accuracy of the numerical model. The temperature distributions, solidification sequences, and defect predictions were compared, and the deviations were analyzed.
Overall, the simulation results were found to be in good agreement with the experimental outcomes. The temperature distributions and solidification sequences predicted by the simulation were consistent with the microstructural analysis results. Additionally, the defect predictions were validated by the lack of significant defects observed in the castings.
6. Conclusion
In this study, a numerical simulation of the thin-walled frame titanium alloy investment casting process was conducted using the ProCAST software. The filling, solidification, and cooling stages of the casting process were simulated, and potential casting defects were predicted. To validate the simulation results, physical experiments were performed, and a comparison between the experimental and simulation outcomes was presented.
The simulation results provided valuable insights into the casting process and enabled the prediction of potential defects. By analyzing the temperature field, flow field, and stress field within the casting system, potential areas for cold shuts, misruns, shrinkage pores, hot tears, and distortion were identified. Optimization strategies were proposed to mitigate these defects, and their effectiveness was validated through experimental validation.
The experimental results confirmed the accuracy of the numerical model. The microstructural analysis revealed that the solidification sequence was consistent with the simulation results, and no significant defects were observed in the castings. The dimensional accuracy measurements and mechanical testing demonstrated that the castings were within the specified tolerances and exhibited good strength and ductility.
In conclusion, this study demonstrates the potential of numerical simulation in predicting and optimizing the thin-walled frame titanium alloy investment casting process. By combining simulation and experimental methods, a comprehensive understanding of the casting process was achieved, and practical guidance for improving casting quality was provided. Future research can focus on further refining the numerical model to capture more complex phenomena and exploring new materials and processes for advanced casting applications.
7. Tables
Table 1: Material Properties of Titanium Alloy and Mold Materials
Property | Titanium Alloy | Mold Material |
---|---|---|
Density (kg/m³) | 4500 | 2500 |
Specific Heat Capacity (J/kg·K) | 520 | 840 |
Thermal Conductivity (W/m·K) | 7.9 | 2.3 |
Latent Heat of Fusion (J/kg) | 330000 | N/A |
Solidus Temperature (°C) | 1630 | N/A |
Liquidus Temperature (°C) | 1660 | N/A |
Table 2: Simulation Parameters
Parameter | Value |
---|---|
Pouring Temperature (°C) | 1700 |
Initial Mold Temperature (°C) | 25 |
Heat Transfer Coefficient (W/m²·K) | 1000 |
Mesh Size (mm) | 2 |