Abstract: In order to solve the problem that ZG15Cr1Mo1 steam turbine combustion pressure cylinder steel casting is sensitive to the cooling rate of heat treatment and has a large crack tendency, the technical requirements and structural characteristics of cast steel parts were analyzed. The casting process of castings was improved by horizontal casting, increasing riser, adding cold iron, and setting slag collecting runner. After reliable verification by numerical simulation analysis, production test was carried out, and qualified castings meeting the requirements were obtained.
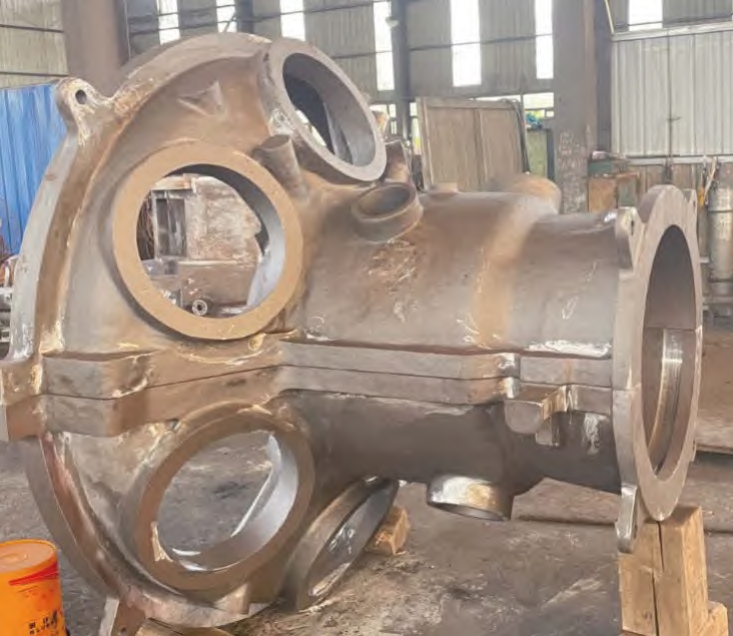
1. Introduction
The gas turbine industry is one of the important indicators of a country’s high-tech level and scientific and technological strength, possessing a prominent strategic position. The combustion pressure cylinder, an essential component of the G15A gas turbine, features a complex structure and thin cylinder walls, which are unfavorable for feeding and shrinkage of the casting, leading to a high tendency for porosity. The material of the combustion pressure cylinder is 2405CD0, with a commercial grade of ZG15Cr1Mo1. This material is sensitive to the cooling rate during heat treatment, easily resulting in uneven mechanical properties within the casting and a significant crack tendency. Therefore, researching the casting process of the combustion pressure cylinder of gas turbines to ensure product quality is particularly important.
2. Basic Parameters and Technical Requirements of the Product
The combustion pressure cylinder, is the upper half of the cylinder, weighing approximately 2,250 kg, and made of ZG15Cr1Mo1 material. The specific chemical composition is presented in Table 1, and the mechanical properties are shown in Table 2. The maximum contour dimensions are 1,600 mm × 1,100 mm × 1,100 mm, with a maximum wall thickness of 90 mm and a minimum wall thickness of 30 mm. NDT (Non-Destructive Testing) requires 100% UT2 (Ultrasonic Testing) and MT2 (Magnetic Particle Testing) acceptance for the casting body.
Table 1: Casting Chemical Composition Requirements (Mass Fraction, %)
Element | C | Si | Mn | P | S | Cr | Mo | Ni | Cu | Al |
---|---|---|---|---|---|---|---|---|---|---|
Range | 0.13-0.20 | 0.20-0.60 | 0.50-0.90 | ≤0.025 | ≤0.025 | 1.00-1.50 | 0.90-1.20 | ≤0.50 | ≤0.35 | ≤0.010 |
Table 2: Mechanical Properties Requirements of Castings at Room Temperature
Property | Tensile Strength (MPa) | Yield Strength (MPa) | Elongation After Fracture (%) | Reduction of Area (%) | Hardness (HBW) |
---|---|---|---|---|---|
Requirement | ≥550 | ≥345 | ≥16 | ≥50 | 180-220 |
3. Structural Analysis of the Casting
Through analysis and research on the structure and technical requirements of the casting, the following casting difficulties were identified:
(1) Minimum Wall Thickness and Cleanliness Requirements
The intake chamber has a minimum wall thickness of only 30 mm, with a pipe flange on the back and a maximum thickness of 90 mm. This area has a large hot spot, prone to sticking sand, slag inclusion, insufficient feeding, and difficulty in cleaning due to the narrow cavity. Additionally, the cleanliness requirement of the intake chamber is high.
(2) Difficulty in Feeding the Large Flange
The large horizontal rib at the back of the cylinder has a significant hot spot, making it difficult for molten steel to feed along the circumferential direction.
(3) Risk of Thermal Cracking and Deformation
The middle section of the cylinder consists of thin walls intersected with thick reinforcing ribs, which poses a significant risk of thermal cracking and deformation. This is primarily due to the uneven cooling rates during the solidification process. As the thicker sections solidify slower than the thinner ones, differential stresses arise due to the temperature gradients. These stresses, combined with the inherent rigidity of the reinforcing ribs, can exceed the material’s tensile strength, leading to cracks. Additionally, the rapid cooling of thin sections can cause contraction forces, further exacerbating the risk of cracking.
To mitigate the risk of thermal cracking and deformation, several strategies can be employed:
- Optimized Cooling Rates: Careful control of the cooling rates during solidification is crucial. This can be achieved by using insulation materials or adjusting the cooling parameters in specific areas to ensure a more uniform cooling profile. Table 3 summarizes the suggested cooling rates and insulation materials for different sections of the combustion pressure cylinder.
Section | Suggested Cooling Rate (°C/h) | Insulation Material |
---|---|---|
Thin Walls | 10-20 | Ceramic Fiber Blanket |
Thick Reinforcing Ribs | 5-10 | Refractory Concrete |
Flange Areas | 15-25 | Silicon Carbide Coating |
- Use of Cold Iron: Cold iron can be strategically placed in areas prone to rapid cooling, such as near thin walls, to moderate the cooling rates and reduce contraction forces. The type and size of cold iron should be carefully selected based on the specific casting dimensions and material properties.
- Sequential Solidification: Ensuring sequential solidification, where the thinner sections solidify first, followed by the thicker sections, can help reduce thermal stresses. This can be achieved through the design of the gating system and the placement of risers. Numerical simulation tools can be used to predict and optimize the solidification sequence.
- Thermal Stress Relief: After casting, thermal stress relief treatments such as annealing can be performed to reduce residual stresses and improve the mechanical properties of the cylinder. These treatments involve heating the casting to a specific temperature and holding it for a period to allow stress relaxation.
Note: This is a schematic representation. Actual treatment parameters may vary.
- Design Modifications: Minor design modifications, such as adding chamfers or fillets to the intersections of thin and thick sections, can reduce stress concentrations and improve the casting’s ability to withstand thermal stresses.
Conclusion on Thermal Cracking and Deformation:
The risk of thermal cracking and deformation in the middle section of the combustion pressure cylinder is a significant challenge. By optimizing cooling rates, using cold iron, ensuring sequential solidification, applying thermal stress relief treatments, and making design modifications, the risk can be mitigated. Continuous monitoring and adjustment of these parameters through experimental trials and numerical simulations are essential to achieving a robust casting process.
4. Casting Defects and Their Mitigation
The casting of the combustion pressure cylinder can be susceptible to various defects, such as porosity, inclusions, and shrinkage cavities. These defects can significantly impact the mechanical properties and performance of the cylinder. Therefore, understanding their causes and developing effective mitigation strategies is crucial.
4.1 Porosity
Porosity refers to the presence of small voids or holes within the casting. It can be caused by gas entrapment during pouring, inadequate venting, or the presence of volatile elements in the molten metal.
Mitigation Strategies for Porosity:
- Improved Venting: Enhance the venting system to allow gases to escape easily during pouring. This can be achieved by adding venting holes or using porous refractory materials.
- Degassing Treatment: Perform degassing treatments on the molten metal to remove dissolved gases before pouring.
- Controlling Pouring Speed: Adjust the pouring speed to minimize turbulence and gas entrapment.
4.2 Inclusions
Inclusions are foreign particles embedded within the casting material. They can be metallic, non-metallic, or oxide-based and can significantly weaken the structure of the cylinder.
Mitigation Strategies for Inclusions:
- Clean Molten Metal: Ensure that the molten metal is free from contaminants by using refining processes such as fluxing or filtration.
- Protect Pouring Operations: Use shrouds or pouring tubes to protect the molten metal from atmospheric contamination.
- Regular Maintenance of Equipment: Keep casting equipment clean and well-maintained to prevent the introduction of foreign particles.
4.3 Shrinkage Cavities
Shrinkage cavities occur due to insufficient molten metal to fill the cavity as it contracts during solidification. This issue is particularly prominent in complex structures such as the combustion and pressure cylinder of steam turbines, where thin cylinder walls and uneven wall thicknesses exacerbate the challenge of feeding and shrinkage compensation.
The combustion and pressure cylinder of the G15A gas turbine, for instance, features intricate geometry with a maximum wall thickness of 90 mm and a minimum of only 30 mm. This variation in wall thickness leads to significant thermal nodes, particularly in areas like the intake chamber and the back flange with large cross-ribs, making it difficult for molten metal to feed properly and resulting in a high tendency for shrinkage cavities and porosity.
To address this problem, advanced casting techniques and detailed process design are essential. The casting process for the ZG15Cr1Mo1 material, which is sensitive to cooling rates during heat treatment and prone to cracks, was refined by adopting a horizontal pouring system, increasing the number of risers and chillers, and incorporating a slag-collecting runner. These measures aim to improve the feeding of the molten metal and reduce shrinkage defects.
Furthermore, numerical simulation using software like AnyCasting was employed to model the solidification process of the steel, allowing for the optimization of the casting design. The simulations ensured that the casting body showed no tendency for shrinkage cavities or porosity, with the modulus meeting the requirements for sequential solidification, where the risers solidify last, both in the circumferential and axial directions.
In practice, the implementation of these refined processes led to a significant reduction in defects. The casting process was validated through production trials, resulting in castings with controlled wall thicknesses, minimal sticking sand, and a notable decrease in cracks in areas with large variations in wall thickness, such as the back flange. The chemical composition and mechanical properties of the castings met the specified standards, along with the customer’s non-destructive testing requirements.
In conclusion, addressing shrinkage cavities in complex castings like the combustion and pressure cylinder of steam turbines necessitates a thorough understanding of the casting material’s characteristics, meticulous process design, and the utilization of advanced simulation tools to predict and mitigate potential defects.