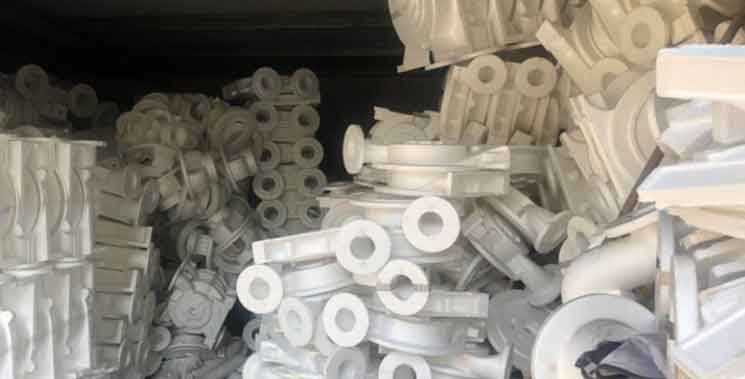
Precision engineering refers to the manufacturing process of creating components or products with extremely high accuracy and precision. Lost foam casting can be a valuable technique for achieving intricate designs in precision engineering. Here’s how it enables the production of complex and precise components:
1.Complex Geometries:
Lost foam casting allows for the creation of intricate and complex shapes that may be difficult or costly to achieve using other manufacturing methods. The foam patterns used in the process can be easily manipulated and shaped, enabling the production of components with intricate details, undercuts, and fine features. This makes it an ideal technique for manufacturing precision components that require intricate geometries.
2.Near-Net Shape:
Lost foam casting can produce components with a high level of accuracy and a near-net shape. The foam patterns accurately reproduce the desired geometry of the final component, minimizing the need for additional machining or finishing operations. This reduces material waste, time, and costs associated with secondary processes, while maintaining the precision of the final component.
3.Tight Tolerances:
Precision engineering often requires components to be manufactured within tight tolerances, meaning the dimensional and geometric specifications must be met with high accuracy. Lost foam casting can achieve tight tolerances by using precise foam patterns and carefully controlling the casting process variables such as temperature, mold material, and pouring technique. This level of control allows for the production of components that meet the required precision specifications.
4.Consistency and Reproducibility:
Lost foam casting offers good consistency and reproducibility in the manufacturing process. Once the optimal casting parameters and foam patterns are established, it becomes easier to replicate the process and produce multiple components with consistent dimensions, surface finish, and mechanical properties. This is crucial in precision engineering, where consistency and uniformity across multiple parts are essential.
5.Integration of Multiple Components:
Lost foam casting allows for the integration of multiple components into a single casting, eliminating the need for assembly and reducing the potential for misalignment or tolerance stack-up issues. This integration capability enhances the overall precision and functionality of the final product.
6.Material Options:
Lost foam casting can be performed with various metals and alloys, including aluminum, iron, steel, and more. This provides flexibility in material selection based on the specific requirements of the precision component, such as strength, corrosion resistance, or thermal properties.
By leveraging the benefits of lost foam casting, precision engineering can achieve intricate designs, tight tolerances, consistent production, and efficient manufacturing processes. The technique enables the creation of complex components with high accuracy, reducing the need for additional machining or assembly steps, and contributing to the overall success of precision engineering applications.