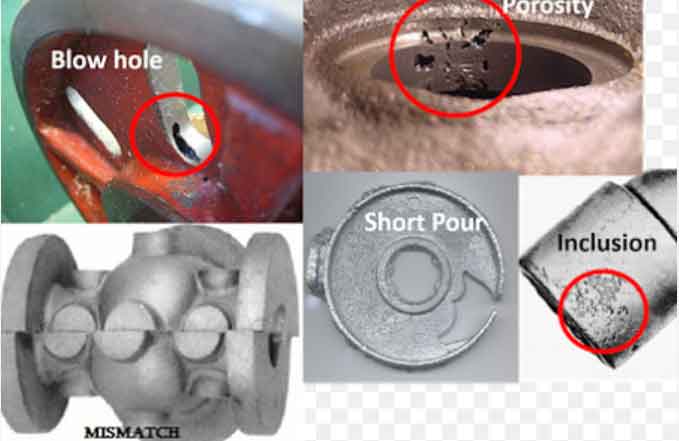
Addressing casting defects is crucial to ensure the production of reliable components in the casting industry. Defects can compromise the structural integrity, functionality, and overall quality of castings. This article discusses key strategies and best practices for effectively addressing casting defects to ensure the production of reliable components.
- Robust Design:
- Start with a robust design that takes into account factors such as part geometry, material selection, gating system design, and riser placement. A well-designed casting can help minimize the occurrence of defects.
- Process Control:
- Implement rigorous process control measures to maintain consistency and repeatability in casting production. This includes monitoring and controlling parameters such as melt temperature, pouring rate, mold temperature, solidification time, and cooling rates.
- Quality Raw Materials:
- Ensure the use of high-quality raw materials that meet specifications and have consistent properties. Raw material quality directly impacts casting quality and can help reduce defects related to impurities or material inconsistencies.
- Melt Treatment:
- Employ effective melt treatment techniques such as degassing, desulfurization, and alloy modification to remove impurities and enhance the cleanliness and integrity of the molten metal.
- Mold and Core Design:
- Optimize mold and core design to facilitate proper metal flow, minimize turbulence, and reduce the occurrence of defects such as porosity or misruns. Consider factors like venting, gating design, core venting, and mold surface finish.
- Proper Gating and Riser Design:
- Design gating and riser systems that promote uniform metal flow, proper filling, and feeding of the casting. This helps minimize defects like shrinkage and cold shuts.
- Quality Control and Inspection:
- Implement rigorous quality control procedures and inspections throughout the casting process. This includes regular visual inspections, dimensional measurements, non-destructive testing, and statistical process control techniques.
- Continuous Improvement:
- Foster a culture of continuous improvement to address casting defects proactively. Encourage feedback from operators, inspectors, and customers to identify areas for improvement. Regularly review and analyze defect data to identify patterns and take corrective actions.
- Supplier Collaboration:
- Collaborate closely with material suppliers, tooling manufacturers, and equipment suppliers to ensure the quality and reliability of the components. Communicate quality requirements, conduct audits, and maintain strong relationships to address any potential issues.
- Employee Training and Skills Development:
- Provide comprehensive training programs for employees involved in the casting process. Enhance their knowledge and skills in defect identification, process optimization, quality control techniques, and problem-solving. Empower employees to contribute to defect prevention and continuous improvement efforts.
Addressing casting defects is essential to ensure the production of reliable components in the casting industry. By implementing robust design practices, maintaining process control, using quality materials, optimizing mold and core design, and emphasizing quality control and continuous improvement, manufacturers can effectively address casting defects and enhance the reliability of their components. Proactive defect prevention, collaboration with suppliers, and ongoing employee training contribute to the production of high-quality, defect-free castings that meet customer expectations and industry standards.