Gate valves are essential components in fluid handling systems, providing effective flow control and shut-off capabilities. Understanding their operation, performing regular maintenance, and making informed selection decisions are crucial for optimal performance and longevity. Here’s a comprehensive guide to gate valves’ operation, maintenance, and selection:
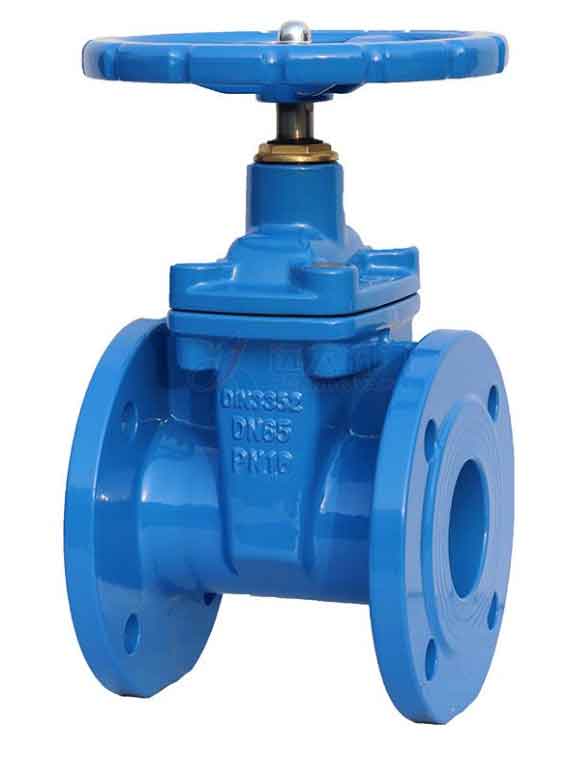
1. Operation of Gate Valves:
- Opening and Closing: Gate valves are operated by rotating the handwheel or actuator to lift or lower the gate, allowing or blocking the flow of fluid.
- Full Open and Close Positions: Gate valves should be fully opened or closed to ensure proper flow control and sealing. Partially open positions are generally avoided as they may cause vibration and accelerated wear.
- Gate Movement: The gate moves in a linear motion perpendicular to the flow direction. It is essential to operate the valve slowly and avoid sudden, forceful movements to prevent damage to the gate or seat.
2. Maintenance of Gate Valves:
- Regular Inspections: Perform visual inspections to check for leaks, corrosion, or any signs of damage. Inspect the sealing surfaces, stem, and packing gland for wear or degradation.
- Lubrication: Apply lubricant to the stem and other moving parts to reduce friction and ensure smooth operation. Follow the manufacturer’s recommendations for the type and frequency of lubrication.
- Packing Adjustment: Periodically inspect and adjust the packing gland to maintain proper stem sealing. Avoid over-tightening, which can hinder the stem movement, or under-tightening, which may cause leakage.
- Stem and Seat Cleaning: Clean the stem and seating surfaces to remove any debris or buildup that may affect the valve’s performance. Use suitable cleaning agents and procedures recommended by the manufacturer.
- Replacement of Worn Components: Replace worn or damaged components, such as seals, gaskets, packing, or the gate, as needed. Use genuine parts from the valve manufacturer to ensure proper fit and performance.
- Regular Testing: Periodically test the valve’s operation, including opening, closing, and shut-off capabilities, to verify its functionality. Conduct pressure tests if required by the system or industry standards.
3. Selection of Gate Valves:
- Application Requirements: Consider the specific requirements of your application, including the fluid type, pressure, temperature, flow rate, and system compatibility.
- Valve Size and Pressure Rating: Select the appropriate valve size and pressure rating based on the pipe diameter and the maximum operating conditions of the system.
- End Connections: Choose the right end connections (flanged, threaded, welded) that match your piping system and installation requirements.
- Material Selection: Consider the compatibility of the valve materials with the fluid properties (corrosiveness, temperature, abrasiveness). Common materials include cast iron, carbon steel, stainless steel, bronze, and various alloys.
- Stem Design: Gate valves can have rising or non-rising stems. Consider the available space and accessibility requirements when selecting the stem design.
- Actuation Options: Determine if manual operation or automated actuation (pneumatic, electric, hydraulic) is required based on the application and system control needs.
- Standards and Certifications: Ensure that the selected gate valve complies with relevant industry standards (API, ANSI, ISO) and meets any specific regulatory or safety requirements.
By understanding the operation principles, performing regular maintenance, and making informed selection decisions, gate valve users can ensure efficient and reliable flow control while extending the valve’s service life. Consulting with valve manufacturers, industry experts, or engineers can provide additional guidance and support in operation, maintenance, and selection processes.