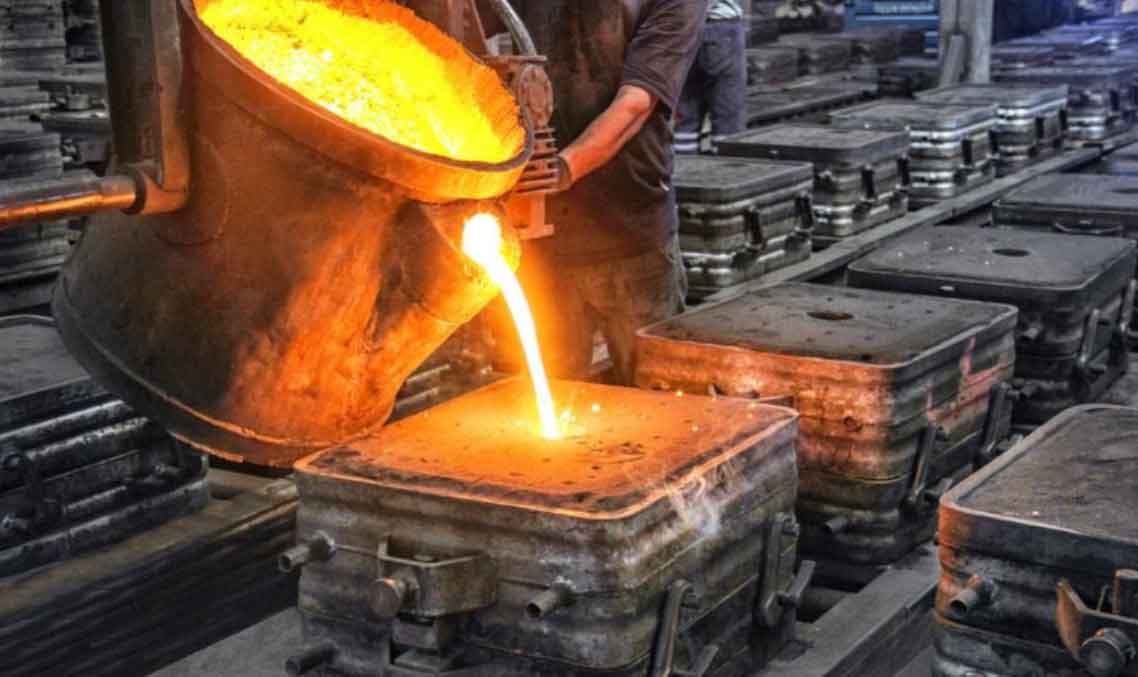
Large-scale sand casting manufacturing projects can present unique challenges that require careful planning and execution to ensure successful outcomes. Addressing these challenges is essential to meet project timelines, maintain casting quality, and manage production costs effectively. Here are some common challenges in large-scale sand casting projects and strategies to address them:
1. Pattern Design and Development:
- Challenge: Creating intricate and large patterns for complex components can be time-consuming and costly.
- Solution: Utilize 3D printing for pattern development to reduce lead times and facilitate design iterations. Implement design for manufacturability principles to optimize patterns for the casting process.
2. Material and Resource Management:
- Challenge: Managing a large volume of raw materials, such as sand, metals, and additives, can be challenging, leading to potential waste and higher costs.
- Solution: Implement efficient material handling and inventory management systems to minimize waste and ensure an uninterrupted supply of materials. Adopt sand reclamation systems to recycle and reuse sand, reducing the need for new sand.
3. Production Consistency:
- Challenge: Maintaining consistent casting quality and dimensions across a large number of castings is crucial but can be challenging in large-scale production.
- Solution: Implement robust quality control measures, including regular inspections, dimensional checks, and non-destructive testing. Continuously monitor and adjust process parameters to ensure consistent casting quality.
4. Mold and Core Assembly:
- Challenge: Assembling large molds and cores can be labor-intensive and time-consuming.
- Solution: Explore automated or semi-automated assembly processes to improve efficiency and accuracy. Implement standardized procedures for mold and core assembly to ensure consistent results.
5. Pouring and Solidification:
- Challenge: Ensuring uniform metal flow during pouring and proper solidification of large castings can be challenging.
- Solution: Optimize gating and riser designs using casting simulation software to achieve uniform filling and reduce the risk of defects. Implement controlled pouring techniques to ensure consistent metal flow.
6. Handling and Transportation:
- Challenge: Large castings can be heavy and challenging to handle, posing safety risks during transportation and installation.
- Solution: Use proper lifting and handling equipment to ensure safe transportation and installation. Collaborate with logistics experts to plan for efficient transportation and delivery.
7. Lead Time Management:
- Challenge: Large-scale projects may have extended lead times, affecting overall project timelines.
- Solution: Implement project management techniques to monitor progress and identify potential bottlenecks. Plan for contingencies and collaborate closely with the casting manufacturer to meet deadlines.
8. Communication and Collaboration:
- Challenge: Large-scale projects involve multiple stakeholders, and effective communication and collaboration are crucial for project success.
- Solution: Establish clear communication channels, hold regular meetings, and ensure all stakeholders are informed about project progress and any changes. Foster a collaborative approach to problem-solving and decision-making.
9. Environmental Impact:
- Challenge: Large-scale sand casting projects can have a significant environmental impact due to resource consumption and emissions.
- Solution: Implement eco-friendly practices, such as using greener binders, recycling sand, and optimizing energy use. Obtain relevant environmental certifications to demonstrate commitment to sustainability.
Addressing these challenges requires a proactive and collaborative approach from all project stakeholders, including design engineers, casting manufacturers, and project managers. By implementing effective strategies and leveraging advanced technologies, large-scale sand casting projects can achieve efficient production, high-quality castings, and successful project outcomes.