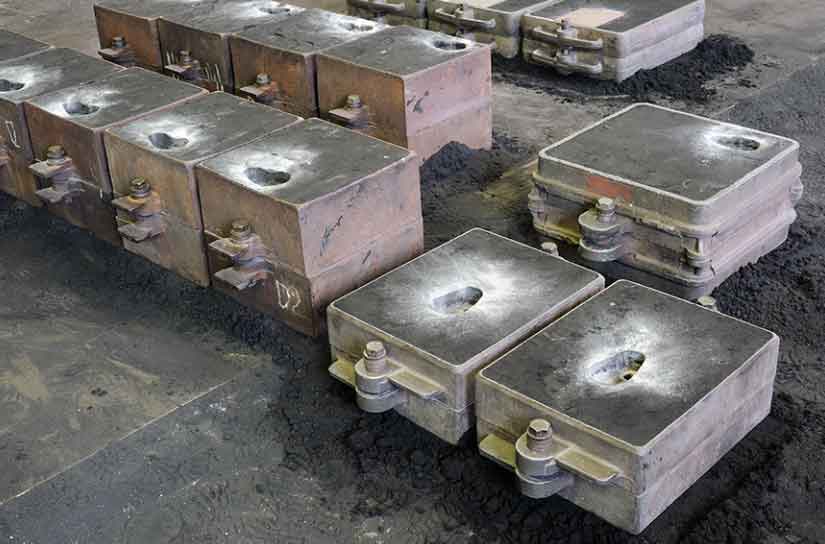
Resin sand casting, like any manufacturing process, can face several challenges that impact casting quality, productivity, and cost-effectiveness. Addressing these challenges effectively is crucial for the success of the resin sand casting process. Here are common challenges in resin sand casting and their corresponding solutions:
1. Surface Defects:
- Challenge: Surface defects, such as pinholes, scabs, and sand inclusions, can occur due to improper sand preparation or inadequate mold venting.
- Solution: Use high-quality sand and resin binders, and optimize the sand conditioning process to minimize surface defects. Proper mold venting and gas removal techniques are essential to reduce the risk of defects.
2. Inconsistent Curing:
- Challenge: Variations in curing time and temperature can lead to inconsistent mold strength and dimensional accuracy.
- Solution: Implement precise control over the curing process using temperature and time monitoring equipment. Conduct regular checks and adjustments to ensure consistent curing conditions.
3. Mold Warping or Distortion:
- Challenge: Mold warping or distortion can occur during the curing process, affecting the final casting’s dimensional accuracy.
- Solution: Use proper support and containment systems during curing to prevent mold warping. Ensure uniform curing conditions to minimize distortion.
4. Core Shift and Misalignment:
- Challenge: Core shift or misalignment can lead to casting defects and dimensional inaccuracies in the final part.
- Solution: Improve core assembly techniques and invest in advanced core setting equipment to ensure proper core alignment during mold assembly.
5. Metal Run-Off and Erosion:
- Challenge: Improper gating design can result in excessive metal run-off and erosion of mold surfaces.
- Solution: Optimize gating and risering design to ensure smooth and controlled metal flow. Incorporate metal flow simulation software to optimize gating systems.
6. Mold and Pattern Wear:
- Challenge: Frequent use of molds and patterns can lead to wear and degradation, affecting casting quality.
- Solution: Conduct regular maintenance and pattern inspection to identify wear and damage. Repair or replace worn-out molds and patterns to maintain casting quality.
7. Porosity and Gas-related Defects:
- Challenge: Trapped gases during the metal pouring process can lead to porosity and gas-related defects.
- Solution: Improve mold venting, implement vacuum sealing and degassing techniques, and optimize pouring and metal flow to reduce the risk of gas-related defects.
8. Pattern Design Complexity:
- Challenge: Complex pattern designs can be challenging to produce with traditional methods.
- Solution: Utilize 3D printing for pattern production to achieve intricate and complex designs more efficiently.
9. Process Control and Quality Assurance:
- Challenge: Inadequate process control and lack of quality assurance measures can lead to inconsistent casting quality.
- Solution: Implement real-time monitoring and process control technologies to ensure casting process stability and quality assurance protocols to verify casting compliance with specifications.
By effectively addressing these challenges and implementing appropriate solutions, foundries can achieve consistent, high-quality castings using resin sand casting and optimize the overall efficiency of the process. Regular process evaluation and continuous improvement efforts are essential for refining the resin sand casting process and meeting the demands of various applications.