Gray cast iron is widely used in various industries due to its excellent machinability, good wear resistance, and damping properties. However, the performance of gray cast iron components can be significantly enhanced through advanced heat treatment techniques. This article explores these techniques and their impact on the microstructure and properties of gray cast iron.
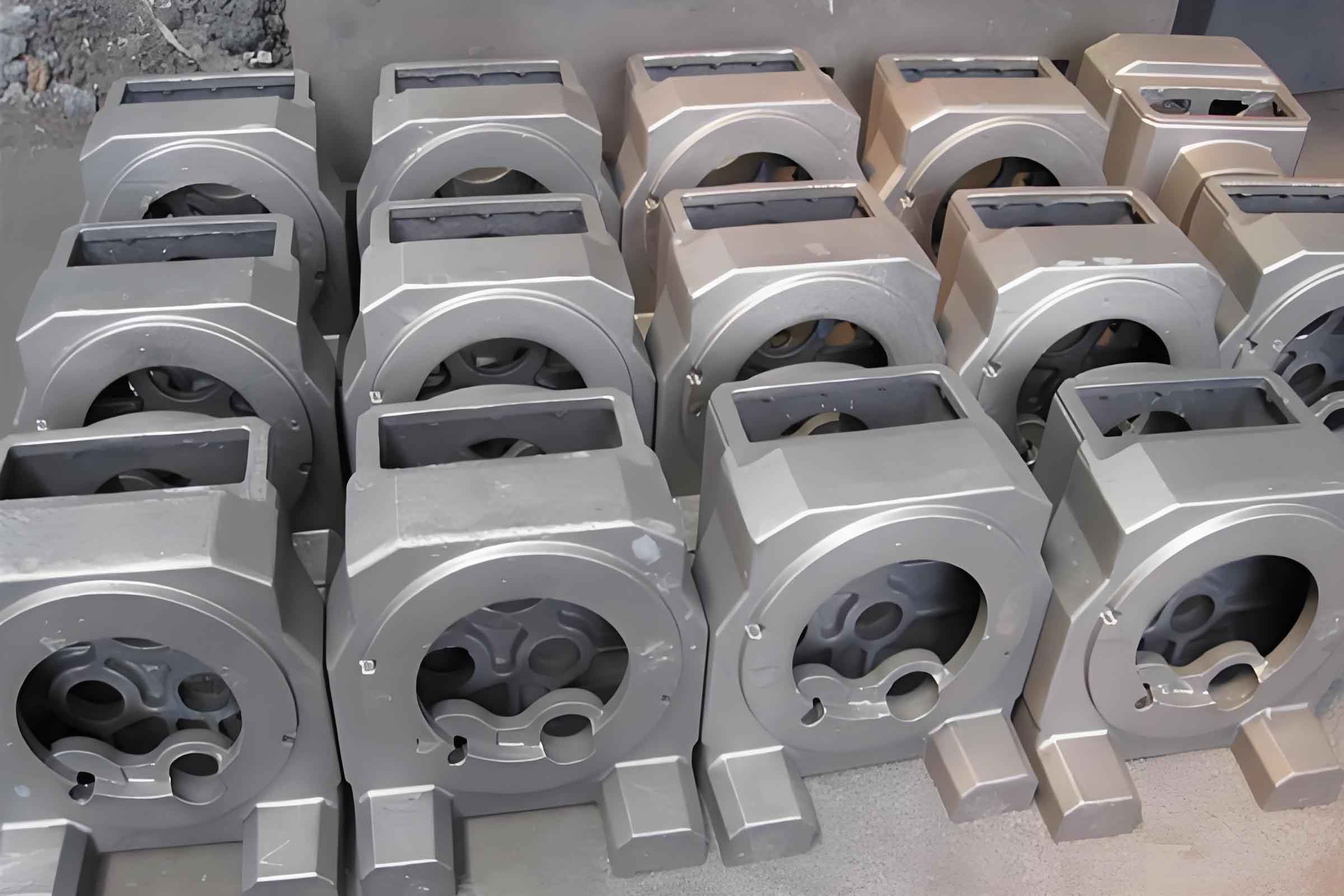
Introduction
Heat treatment is a critical process in the manufacturing of gray cast iron components. By manipulating the cooling rates and applying specific heat treatments, it is possible to optimize the microstructure, thereby enhancing the mechanical properties of the material. This article delves into various advanced heat treatment techniques and their effects on the microstructure of gray cast iron.
Importance of Microstructure in Gray Cast Iron
The microstructure of gray cast iron consists primarily of graphite flakes embedded in a matrix of ferrite, pearlite, or a combination of both. The size, shape, and distribution of these graphite flakes, as well as the matrix structure, play a crucial role in determining the mechanical properties of the material.
Advanced Heat Treatment Techniques
- Austempering
- Normalizing
- Quenching and Tempering
- Annealing
- Surface Hardening
Comparative Analysis of Heat Treatment Techniques
Heat Treatment Technique | Objective | Microstructural Changes | Mechanical Properties Enhanced |
---|---|---|---|
Austempering | Increase toughness | Formation of ausferrite (acicular ferrite and carbon-stabilized austenite) | Improved toughness and strength |
Normalizing | Refine grain structure | Uniform pearlitic or ferritic structure | Enhanced strength and hardness |
Quenching and Tempering | Increase hardness and strength | Martensitic transformation followed by tempering | High hardness and tensile strength |
Annealing | Reduce hardness and relieve stresses | Coarse pearlitic structure or fully ferritic structure | Improved machinability and ductility |
Surface Hardening | Increase surface hardness | Formation of hardened layer on the surface | Improved wear resistance |
Detailed Analysis of Heat Treatment Techniques
Austempering
Objective:
- Increase toughness and strength while maintaining ductility.
Process:
- Heating the cast iron to the austenitizing temperature (850-950°C).
- Rapid cooling to an intermediate temperature range (250-400°C) and holding until the transformation is complete.
Microstructural Changes:
- Formation of ausferrite, a mixture of acicular ferrite and carbon-stabilized austenite.
Applications:
- Components requiring a combination of high strength and toughness, such as gears and crankshafts.
Benefits:
- Improved toughness, reduced distortion, and enhanced fatigue strength.
Normalizing
Objective:
- Refine the grain structure and improve mechanical properties.
Process:
- Heating the cast iron to a temperature above its critical range (850-950°C).
- Air cooling to room temperature.
Microstructural Changes:
- Formation of a uniform pearlitic or ferritic structure.
Applications:
- General automotive parts, such as brake drums and clutch plates.
Benefits:
- Enhanced strength, hardness, and wear resistance.
Quenching and Tempering
Objective:
- Increase hardness and tensile strength.
Process:
- Heating the cast iron to the austenitizing temperature (850-950°C).
- Rapid cooling (quenching) in water or oil.
- Reheating (tempering) to a lower temperature (150-650°C) and holding.
Microstructural Changes:
- Formation of martensite during quenching followed by tempering to reduce brittleness.
Applications:
- Heavy-duty gears, machine tool parts.
Benefits:
- High hardness, improved tensile strength, and toughness.
Annealing
Objective:
- Reduce hardness, relieve internal stresses, and improve machinability.
Process:
- Heating the cast iron to a temperature just below the critical range (700-900°C).
- Slow cooling in the furnace.
Microstructural Changes:
- Formation of a coarse pearlitic structure or fully ferritic structure.
Applications:
- Components requiring excellent machinability and ductility, such as engine blocks and cylinder heads.
Benefits:
- Improved machinability, reduced residual stresses, and enhanced ductility.
Surface Hardening
Objective:
- Increase surface hardness for better wear resistance.
Process:
- Techniques such as induction hardening, laser hardening, or carburizing.
Microstructural Changes:
- Formation of a hardened layer on the surface while maintaining a tough core.
Applications:
- Wear-resistant surfaces, such as camshafts and valve seats.
Benefits:
- Improved wear resistance and surface durability.
Case Studies
Case Study 1: Austempering of Gears
Objective:
- Enhance the toughness and wear resistance of gears used in heavy-duty applications.
Process:
- Austempering at 350°C for 2 hours.
Results:
- Significant improvement in toughness and fatigue strength, leading to longer gear life and better performance under high loads.
Case Study 2: Normalizing of Brake Drums
Objective:
- Improve the strength and wear resistance of brake drums.
Process:
- Normalizing at 900°C followed by air cooling.
Results:
- Enhanced mechanical properties with uniform hardness and improved wear resistance, leading to longer service life and reliable performance.
Future Directions and Research
- Nano-structured Coatings
- Advanced Simulation Techniques
- Integration of AI in Heat Treatment Processes
- Eco-friendly Heat Treatment Methods
Nano-structured Coatings
Trend:
- Development of nano-structured coatings to further enhance wear resistance and surface properties.
Impact:
- Superior performance in high-stress applications.
- Increased lifespan of components.
Advanced Simulation Techniques
Trend:
- Use of advanced simulation techniques to predict microstructural changes and optimize heat treatment processes.
Impact:
- More efficient and precise heat treatment processes.
- Reduced development time and costs.
Integration of AI in Heat Treatment Processes
Trend:
- Integration of artificial intelligence and machine learning to optimize heat treatment parameters in real-time.
Impact:
- Improved process control and consistency.
- Enhanced quality and performance of cast iron components.
Eco-friendly Heat Treatment Methods
Trend:
- Development of eco-friendly heat treatment methods to reduce the environmental impact.
Impact:
- Sustainable manufacturing processes.
- Reduced energy consumption and emissions.
Conclusion
Advanced heat treatment techniques play a crucial role in optimizing the microstructure and enhancing the mechanical properties of gray cast iron. By understanding the effects of different heat treatments, manufacturers can select the most appropriate methods to achieve desired properties for specific applications. Ongoing research and innovations in heat treatment technology will continue to improve the performance and sustainability of gray cast iron components, ensuring their relevance in future industrial applications.