Abstract
Since entering the 21st century, with the rapid development of China’s casting industry, China has become a major casting country. The annual production of castings has gradually exceeded the total production of developed countries such as the United States, Japan, the United Kingdom, France, and Germany, accounting for one-third of the global casting production. Moreover, with the continuous development of industrial technology, the requirements for casting quality and accuracy are becoming higher and higher. Among them, coated sand casting, as an advanced casting process, has gradually received widespread attention due to its high precision and quality characteristics.
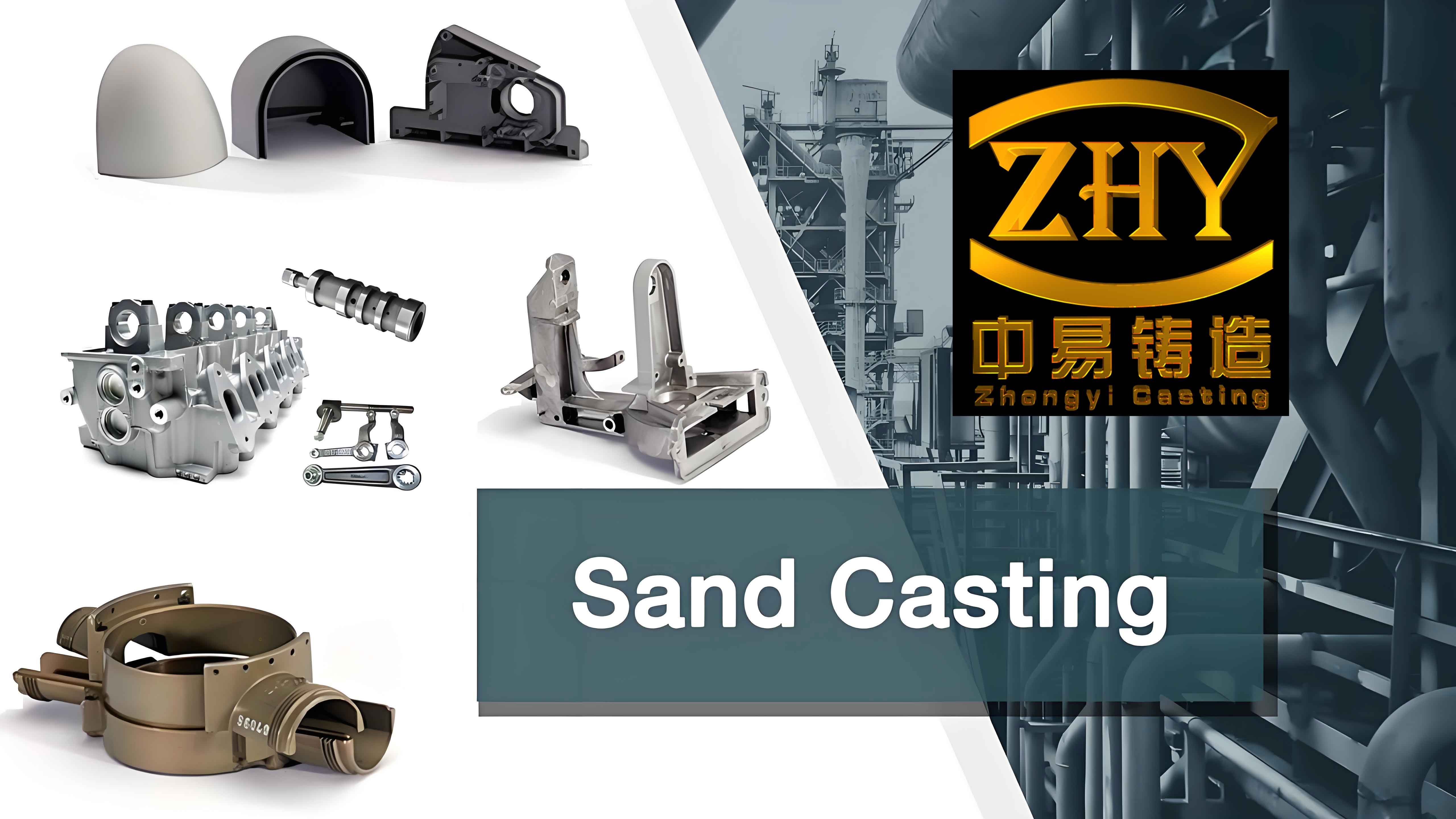
1. Introduction
Complex sand casting is an important casting process widely used in the automotive, machinery, and aviation industries. Traditional casting methods often face issues such as poor surface quality of castings, many casting defects, and low production efficiency when dealing with complex sand molds, which seriously affect the overall performance and service life of castings. With the development of materials science and process technology, high-performance coated sand, as a new type of casting material, has gradually gained widespread application in complex sand casting due to its excellent properties and wide adaptability.
2. Overview of Coated Sand Casting
Coated sand casting, as a modern casting process, occupies an important position in the manufacturing industry due to its high precision and efficiency. The core of this method lies in the use of coated sand material to create the mold. This special sand material is carefully mixed with sand grains, resin, and curing agent. It not only exhibits excellent fluidity but can easily fill every corner of the mold, ensuring high precision and quality of the castings. The superior performance of coated sand is attributed to its unique composition. The sand grains mainly provide the basic skeletal structure, while the resin serves as a binder to tightly adhere the sand grains together. The addition of the curing agent enables the resin to rapidly cure under specific conditions, maintaining the stability of the mold. This series of chemical reactions ensures the solidity and durability of the mold during the casting process.
3. Composition and Properties of Coated Sand
3.1 Composition of Coated Sand
High-performance coated sand is mainly composed of base sand, coating material, and additives. Quartz sand is commonly used as the base sand, and the shape and size of its particles directly affect the performance of the coated sand. High-quality quartz sand particles are uniform in size and smooth in surface, which helps in the uniform coverage of the resin, enhancing the strength and heat resistance of the coated sand. The coating material generally selects thermoplastic resins such as phenolic resin or furan resin, which can form a hard shell at high temperatures, providing good support and heat resistance. Additives are selected according to specific needs, such as toughening agents and antioxidants, to further improve the performance of the coated sand and enhance its stability and adaptability during the casting process.
3.2 Properties of Coated Sand
High-performance coated sand exhibits a series of excellent properties, making it outstanding in complex sand casting. It has high strength and hardness, maintaining stability at high temperatures and not easily deforming. This allows the coated sand to withstand various stresses generated during the complex sand casting process, ensuring the dimensional accuracy and surface quality of the castings. Additionally, it has good high-temperature resistance and chemical stability, forming a stable resin shell at high temperatures, effectively preventing defects such as sand sticking and inclusion during the casting process. Furthermore, it has excellent fluidity and formability, filling complex cavities to ensure perfect reproduction of the details of the castings, meeting the manufacturing requirements of complex castings.
4. Characteristics of High-Performance Coated Sand
4.1 Suitable Physical Strength
High-performance coated sand stands out in the casting industry due to its suitable physical strength, which is crucial for ensuring the quality of castings. Physical strength refers to the physical pressure that the sand mold can withstand during the actual casting process. It is a key factor enabling high-performance coated sand to stably support the pouring of molten metal. Through careful optimization of the ratio and scientific control of the process, high-performance coated sand achieves an ideal balance in strength, neither being too fragile to withstand the impact of molten metal nor too hard to cause difficulties in demolding. This suitable physical strength provides a solid foundation for the production of high-precision and high-quality castings, especially in the manufacturing of complex-shaped castings such as automobile engine blocks and machine tool beds. It can effectively resist the impact of molten metal, preventing casting defects caused by mold cracking, thereby ensuring the integrity and precision of the castings. Additionally, suitable physical strength means that high-performance coated sand can maintain stable shape and size during the casting process, further improving the quality of the castings.
4.2 Good Fluidity
Good fluidity is another prominent feature of high-performance coated sand, enabling it to easily fill every corner of the mold. During the casting process, coated sand with good fluidity can quickly and uniformly fill the mold, whether it is fine gaps or complex internal structures. This not only greatly ensures the integrity and detail precision of the castings but also significantly improves production efficiency. Good fluidity means that high-performance coated sand can rapidly complete the mold filling task, shortening the production cycle. At the same time, uniform filling reduces casting defects caused by uneven filling, further improving the quality of the castings. This feature gives high-performance coated sand a wide application prospect in the casting industry, especially in fields requiring high-precision and high-quality castings.
4.3 Excellent Collapsibility
The collapsibility of high-performance coated sand refers to the ability of the sand mold to easily collapse after the casting has cooled and solidified. This feature greatly facilitates the demolding and cleaning of castings. Excellent collapsibility not only simplifies the post-processing process of castings but also significantly improves production efficiency, especially in mass production. This feature can significantly reduce labor intensity and enhance overall production benefits. The excellent collapsibility of high-performance coated sand stems from its unique material composition and scientific preparation process. For example, by precisely controlling the ratio of sand grains, resin, and curing agent and optimizing the curing process, the sand mold maintains sufficient strength while having good collapsibility. This feature makes high-performance coated sand outstanding in casting complex-shaped castings, providing a strong guarantee for the production of high-precision and high-quality castings.
5. Application of Coated Sand in Complex Sand Casting
5.1 Application of Coated Sand in Automobile Engine Block Casting
The automobile engine block is a core component of the engine, and its casting quality directly affects engine performance and life. High-performance coated sand has become an ideal material for block casting due to its excellent formability and stability. For example, during the block casting process, coated sand can effectively fill complex cavities, ensuring clear internal structural details of the block and avoiding defects caused by poor fluidity of molding sand. Additionally, the high strength and high-temperature resistance of coated sand can withstand the impact and erosion of high-temperature molten metal during the casting process, preventing common deformation and cracking issues in block casting, thereby improving block quality and production efficiency.
5.2 Application of Coated Sand in Turbine Blade Casting
Turbine blades are key components of aeroengines and gas turbines, and their casting process requires extremely high precision and quality. High-performance coated sand can accurately replicate the complex internal structure and contour of the blades due to its excellent fluidity and formability. For example, during turbine blade casting, coated sand can uniformly cover the surface of complex cavities, avoiding the issues of easy deformation and difficult forming of traditional casting sand at high temperatures. Additionally, the high strength and high-temperature resistance of coated sand can effectively resist the erosion of high-temperature molten metal, reducing defects such as sand inclusion and shrinkage during the casting process, thereby improving blade quality and service life.
5.3 Application of Coated Sand in Complex Gear Casting
Complex gears are the core components of mechanical transmission systems, and their casting quality significantly affects the performance and stability of mechanical equipment. For example, high-performance coated sand can accurately replicate the complex tooth shape and internal structure of gears due to its excellent filling and forming capabilities. During gear casting, coated sand can quickly fill the cavity, ensuring the dimensional accuracy and surface quality of the castings. Moreover, the high strength and high-temperature resistance of coated sand can withstand the impact and erosion of high-temperature molten metal during the casting process, reducing common problems such as sand sticking and inclusion in gear casting, thereby improving gear quality and production efficiency.
6. Application Strategies of High-Performance Coated Sand in Complex Sand Casting
6.1 Selection of Suitable High-Performance Coated Sand
Selecting suitable high-performance coated sand is crucial in complex sand casting. Enterprises should base their selection on specific requirements of the castings, including shape, size, material, and other factors. They need to choose coated sand with appropriate strength, good fluidity, and excellent collapsibility to ensure casting precision and quality while improving production efficiency. Additionally, enterprises should consider the moisture resistance of coated sand because changes in environmental humidity during storage and transportation may affect the castings. The moisture resistance of high-performance coated sand can effectively resist this impact, maintaining the stability of the castings. Therefore, when selecting high-performance coated sand, enterprises should comprehensively consider various factors to ensure that the selected coated sand meets the production requirements of castings.
6.2 Optimization of Casting Process Parameters
Optimizing casting process parameters is key to improving casting quality in complex sand casting. The settings of parameters such as heating temperature, curing time, and sand injection pressure directly affect the quality and precision of castings. Therefore, enterprises need to reasonably set these parameters based on specific casting needs and material characteristics. For example, a suitable heating temperature ensures the fluidity of coated sand, enabling it to better fill the mold. A reasonable curing time guarantees the strength of the sand mold, preventing mold cracking during the casting process. Appropriate sand injection pressure ensures the compactness of the sand mold, thereby improving casting precision. By continuously optimizing these process parameters, enterprises can further enhance casting quality and production efficiency.
6.3 Strengthening Mold Design and Manufacturing
In complex sand casting, the precision of the mold directly determines the dimensional accuracy of the castings, and its durability affects production efficiency and cost. Therefore, when using high-performance coated sand for casting, enterprises must attach importance to mold design and manufacturing. To improve mold precision, enterprises should adopt advanced processing technologies and equipment to ensure mold manufacturing quality. At the same time, mold design should fully consider the characteristics and production needs of castings to achieve optimal casting results. By strengthening mold design and manufacturing, enterprises can further improve casting quality and production efficiency, meeting market demands.
7. Conclusion
High-performance coated sand has broad application prospects in complex sand casting. Enterprises can effectively improve casting quality and precision, reduce production costs, and create greater economic benefits by selecting suitable high-performance coated sand, optimizing casting process parameters, strengthening mold design and manufacturing, strictly controlling the production environment, and intensifying quality inspection and control.
Table 1. Comparison of Properties of Traditional and High-Performance Coated Sand
Property | Traditional Coated Sand | High-Performance Coated Sand |
---|---|---|
Strength | Medium | High |
Hardness | Low to Medium | High |
Heat Resistance | Low to Medium | High |
Fluidity | Low to Medium | Excellent |
Collapsibility | Poor to Medium | Excellent |
Precision of Castings | Low to Medium | High |
Surface Quality | Rough | Smooth |
Production Efficiency | Low to Medium | High |
Table 2. Application Examples of High-Performance Coated Sand
Application Area | Casting Component | Key Characteristics |
---|---|---|
Automobile Industry | Engine Block | Complex cavity, high precision |
Aerospace Industry | Turbine Blade | High temperature resistance |
Machinery Industry | Complex Gear | Precise tooth shape |