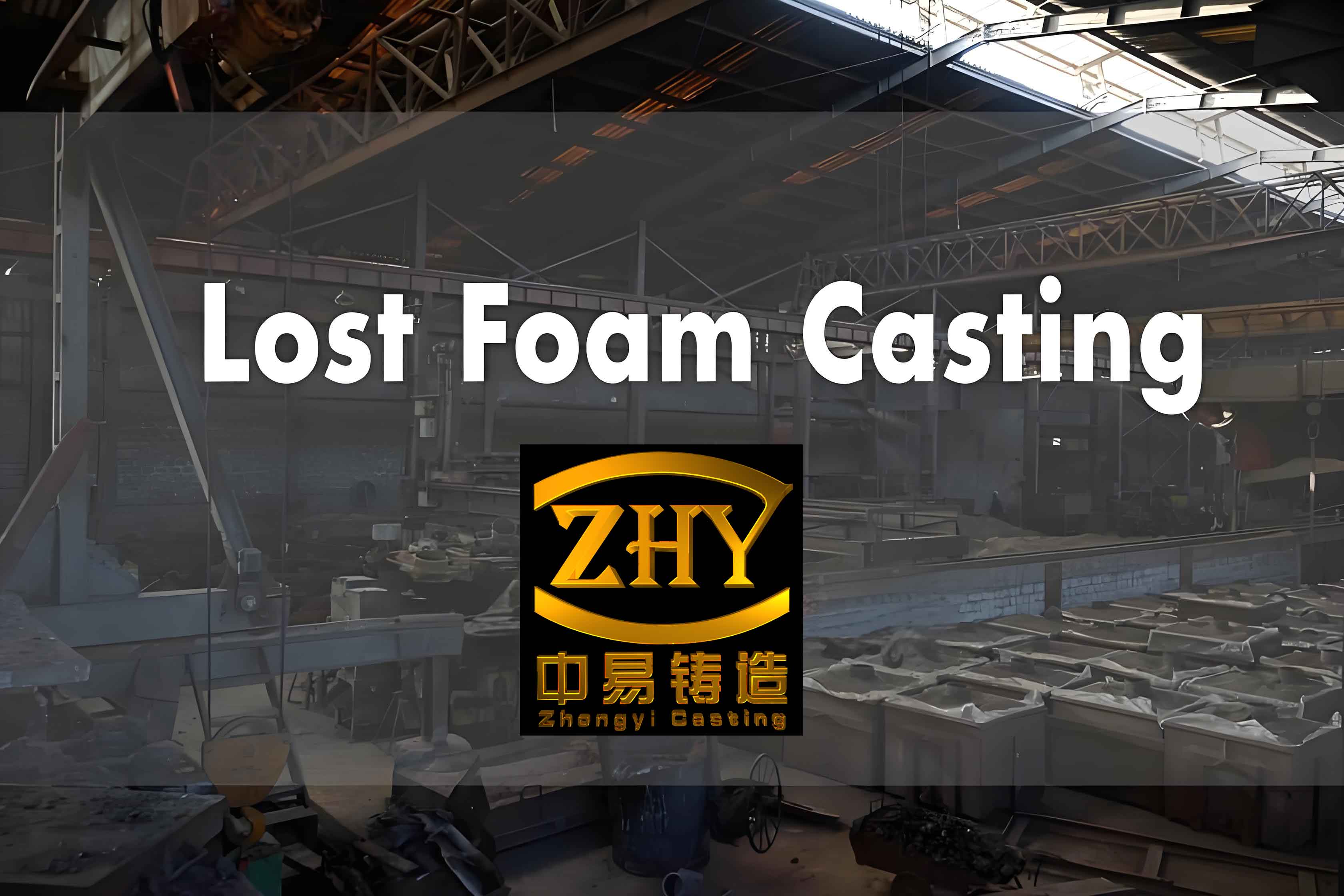
Lost foam casting is an innovative and versatile casting technique that offers significant advantages in producing complex metal components. The quality of castings produced using lost foam casting heavily depends on the materials used for the molds. Advanced mold materials can significantly enhance the casting quality by improving surface finish, dimensional accuracy, and mechanical properties. This article explores various advanced mold materials used in lost foam casting and their impact on casting quality.
Lost Foam Casting Overview
Lost foam casting is a method where a foam pattern, coated with a refractory material, is placed in a sand mold. The foam pattern vaporizes when molten metal is poured into the mold, leaving a metal casting that precisely replicates the foam pattern. This technique is particularly beneficial for producing components with intricate shapes and fine details.
Steps in Lost Foam Casting
- Foam Pattern Creation:
- A foam model is created using polystyrene foam, either by machining or molding.
- Pattern Assembly:
- The foam pattern is assembled with a gating system if required.
- Coating:
- The foam pattern is coated with a refractory material to form a thin shell.
- Mold Preparation:
- The coated foam pattern is placed in a sand mold, and sand is packed around it.
- Metal Pouring:
- Molten metal is poured into the mold, causing the foam pattern to vaporize and be replaced by the metal.
- Mold Breakout:
- Once the metal has solidified, the sand mold is broken away to reveal the metal casting.
- Finishing:
- The casting is cleaned, and any excess material is removed to achieve the final product.
Importance of Mold Materials in Lost Foam Casting
The mold material in lost foam casting plays a crucial role in determining the quality of the final casting. The properties of the mold material affect several aspects of the casting process, including the surface finish, dimensional accuracy, and mechanical properties of the cast component. Advanced mold materials offer numerous benefits that contribute to improved casting quality.
Key Properties of Mold Materials
- Thermal Stability:
- Mold materials must withstand high temperatures without degrading or reacting with the molten metal.
- Permeability:
- The mold material should allow gases generated during the casting process to escape, preventing defects.
- Refractoriness:
- The ability to withstand high temperatures without melting or deforming.
- Surface Finish:
- The mold material should provide a smooth surface to achieve a high-quality finish on the casting.
- Dimensional Accuracy:
- The mold material should maintain its shape and dimensions throughout the casting process to ensure precise castings.
- Ease of Removal:
- The mold material should be easily removable after casting without damaging the cast component.
Advanced Mold Materials for Lost Foam Casting
Several advanced mold materials have been developed to address the challenges associated with lost foam casting. These materials offer enhanced properties that contribute to improved casting quality.
Zircon Sand
Zircon sand is a high-performance mold material commonly used in lost foam casting. It is composed of zirconium silicate and offers excellent thermal stability and refractoriness.
- Thermal Stability: Withstands high temperatures without reacting with the molten metal.
- Refractoriness: High melting point ensures the mold material does not deform or melt during casting.
- Surface Finish: Provides a smooth surface for high-quality casting finish.
- Dimensional Accuracy: Maintains shape and dimensions, ensuring precise castings.
Property | Zircon Sand |
---|---|
Thermal Stability | High |
Refractoriness | High |
Surface Finish | Excellent |
Dimensional Accuracy | Excellent |
Fused Silica
Fused silica is another advanced mold material used in lost foam casting. It is composed of high-purity silicon dioxide and offers excellent thermal properties and low thermal expansion.
- Thermal Stability: Excellent resistance to high temperatures.
- Permeability: Allows gases to escape, reducing defects.
- Surface Finish: Provides a smooth casting surface.
- Dimensional Accuracy: Low thermal expansion ensures precise castings.
Property | Fused Silica |
---|---|
Thermal Stability | Excellent |
Permeability | High |
Surface Finish | Excellent |
Dimensional Accuracy | Excellent |
Alumina
Alumina, or aluminum oxide, is a highly refractory material used in lost foam casting for its exceptional thermal and mechanical properties.
- Thermal Stability: Withstands very high temperatures without degradation.
- Refractoriness: Extremely high melting point.
- Surface Finish: Provides a high-quality finish.
- Dimensional Accuracy: Maintains dimensional stability during casting.
Property | Alumina |
---|---|
Thermal Stability | Very High |
Refractoriness | Very High |
Surface Finish | High |
Dimensional Accuracy | High |
Chromite Sand
Chromite sand is a high-density material used in lost foam casting for its excellent thermal properties and resistance to thermal shock.
- Thermal Stability: Excellent resistance to high temperatures.
- Thermal Shock Resistance: Withstands rapid temperature changes.
- Surface Finish: Provides a smooth casting surface.
- Dimensional Accuracy: Maintains shape and dimensions during casting.
Property | Chromite Sand |
---|---|
Thermal Stability | Excellent |
Thermal Shock Resistance | High |
Surface Finish | Excellent |
Dimensional Accuracy | High |
Benefits of Advanced Mold Materials
The use of advanced mold materials in lost foam casting offers several benefits that contribute to improved casting quality.
Enhanced Surface Finish
Advanced mold materials such as zircon sand, fused silica, and chromite sand provide a smooth surface finish, reducing the need for extensive post-casting machining and finishing.
Improved Dimensional Accuracy
Materials like fused silica and alumina maintain their shape and dimensions throughout the casting process, ensuring high precision and accuracy in the final cast components.
Increased Thermal Stability
Advanced mold materials withstand high temperatures without degrading or reacting with the molten metal, preventing defects and ensuring the integrity of the castings.
Better Permeability
Materials with high permeability, such as fused silica, allow gases generated during the casting process to escape, reducing the likelihood of defects such as gas porosity.
Reduced Defects
The superior properties of advanced mold materials, including thermal stability, refractoriness, and dimensional accuracy, contribute to reduced casting defects, resulting in higher-quality cast components.
Benefits | Advanced Mold Materials |
---|---|
Enhanced Surface Finish | Zircon Sand, Fused Silica, Chromite Sand |
Improved Dimensional Accuracy | Fused Silica, Alumina |
Increased Thermal Stability | Zircon Sand, Fused Silica, Alumina |
Better Permeability | Fused Silica |
Reduced Defects | All advanced mold materials |
Conclusion
The quality of castings produced using lost foam casting is significantly influenced by the mold materials used. Advanced mold materials such as zircon sand, fused silica, alumina, and chromite sand offer superior properties that enhance the surface finish, dimensional accuracy, thermal stability, and overall quality of the cast components. By utilizing these advanced mold materials, manufacturers can achieve higher-quality castings with reduced defects, improved mechanical properties, and better performance, meeting the demanding requirements of various industries. The continued development and application of advanced mold materials in lost foam casting will play a crucial role in advancing the capabilities and applications of this innovative casting technique.