Advancements in gray iron castings have played a significant role in driving industry growth and expanding their application in various sectors. Some key innovations that have contributed to the development and growth of gray iron castings include:
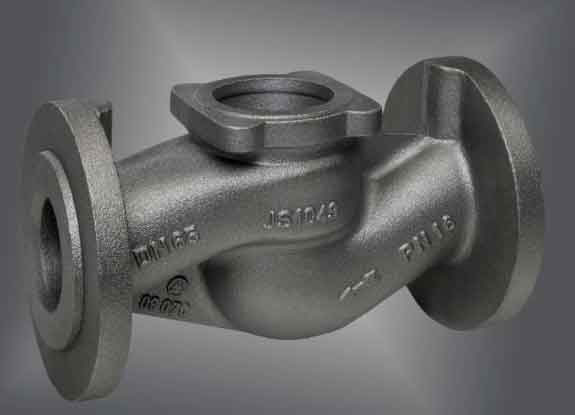
- Improved Metallurgy: Advancements in metallurgical understanding and alloying techniques have led to the development of new gray iron grades with enhanced mechanical properties. Modern gray iron alloys are designed to exhibit better strength, wear resistance, and thermal conductivity, making them suitable for a wider range of applications.
- Computer-Aided Design (CAD) and Simulation: CAD software and simulation tools have revolutionized the casting design process. Engineers can now optimize the design of gray iron castings digitally, allowing for better control of the cooling and solidification process, minimizing defects, and reducing the need for physical prototypes.
- 3D Printing and Rapid Prototyping: Additive manufacturing technologies, such as 3D printing, have started to impact the casting industry. They allow for the rapid production of intricate patterns and cores, reducing lead times and enabling the production of complex gray iron castings that were previously challenging or not feasible.
- Digital Manufacturing and Automation: Foundries are increasingly adopting digital manufacturing and automation technologies to improve efficiency, reduce waste, and enhance quality control. Advanced robotics and automated systems have streamlined the casting process, leading to higher production rates and consistency in casting quality.
- Innovative Casting Methods: Foundries are exploring new casting methods, such as vacuum casting and squeeze casting, to produce higher quality and more intricate gray iron castings. These techniques offer better metal distribution, reduced porosity, and improved surface finishes.
- Non-Destructive Testing (NDT) Techniques: NDT methods, such as ultrasonic testing and X-ray inspection, have advanced significantly, allowing for more accurate and reliable detection of internal defects in gray iron castings. This has improved the overall quality assurance process and reduced the risk of defective parts.
- Environmental Sustainability: The gray iron casting industry has been working towards reducing its environmental impact by adopting more sustainable practices. Recycling of scrap iron and optimizing energy consumption in the casting process are examples of these initiatives.
- Smart Foundries: The concept of “smart foundries” is gaining momentum, where data analytics, IoT devices, and AI-driven systems are used to monitor and optimize the entire casting process, from melt control to quality control. This data-driven approach enhances productivity and minimizes waste.
- Material Science and Coatings: Research in material science has led to the development of advanced coatings for gray iron castings, enhancing their corrosion resistance and overall performance in harsh environments.
These innovations and advancements in gray iron castings have expanded their application in industries such as automotive, construction, agriculture, and more. As technology continues to evolve, gray iron castings will likely remain a vital component of the industrial engineering landscape, offering a cost-effective and reliable solution for a wide range of applications.