Advancements in heat treatment technologies for high-performance castings have been driven by the need for improved mechanical properties, dimensional stability, and overall performance. Here are some notable advancements in heat treatment technologies for high-performance castings:
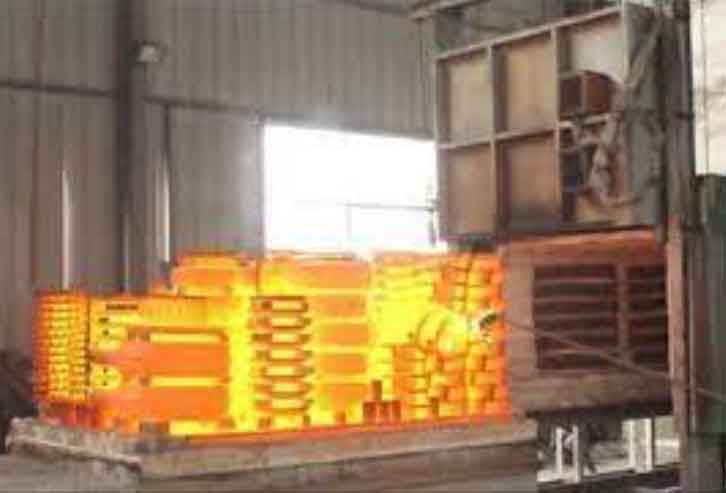
- Vacuum Heat Treatment: Vacuum heat treatment involves carrying out the heat treatment process in a controlled environment with low oxygen levels. This technology offers several advantages, including reduced oxidation and decarburization, improved cleanliness of the castings, and enhanced control over the heat treatment process. Vacuum heat treatment is particularly beneficial for high-alloy and reactive materials that are sensitive to oxygen and other contaminants.
- Induction Heat Treatment: Induction heat treatment utilizes electromagnetic induction to heat the casting rapidly and uniformly. This technology offers precise and localized heating, enabling selective heat treatment of specific areas of the casting, such as critical sections or surface hardening. Induction heat treatment is known for its energy efficiency, shorter cycle times, and excellent controllability, making it suitable for high-performance castings with complex geometries.
- High-Pressure Heat Treatment: High-pressure heat treatment, also known as hot isostatic pressing (HIP), involves applying high pressure to the casting while it is subjected to heat treatment. This process helps to eliminate internal porosity, improve density, and enhance the mechanical properties of the casting. High-pressure heat treatment is particularly advantageous for castings made from materials prone to porosity or for achieving near-net-shape components with superior properties.
- Cryogenic Treatment: Cryogenic treatment involves subjecting the casting to extremely low temperatures, typically below -150°C (-238°F) for an extended period. This treatment aims to transform retained austenite into martensite, which can enhance hardness, wear resistance, and dimensional stability. Cryogenic treatment is often used in conjunction with other heat treatment processes to optimize the properties of high-performance castings, particularly for tooling and wear-resistant applications.
- Pulse Plasma Ion Nitriding: Pulse plasma ion nitriding is a surface treatment technique that improves the wear resistance and surface hardness of castings. It involves bombarding the casting surface with a high-energy plasma containing nitrogen ions, which diffuses into the surface, forming a hardened layer. This technology offers precise control over the nitriding process, enabling customization of the surface properties to meet specific performance requirements.
- Additive Manufacturing-Specific Heat Treatment: With the increasing use of additive manufacturing (3D printing) for producing high-performance castings, heat treatment technologies specifically designed for additive manufacturing have emerged. These technologies address the unique challenges associated with the microstructure and properties of additively manufactured castings. Examples include stress relieving, hot isostatic pressing (HIP), and heat treatment processes optimized for specific additive manufacturing processes like selective laser melting (SLM) or electron beam melting (EBM).
These advancements in heat treatment technologies offer improved control, efficiency, and performance for high-performance castings. However, it’s important to note that the selection of the appropriate heat treatment technology depends on the specific material, casting design, and performance requirements. Consulting with experts in metallurgy and heat treatment processes is essential for determining the optimal heat treatment strategy for high-performance castings.