Quality assurance in steel casting manufacturing is crucial to ensure consistency and excellence in the final product. Manufacturers employ various strategies and processes to maintain high-quality standards throughout the production cycle. Here are some key methods used by manufacturers to ensure quality assurance in steel casting manufacturing:
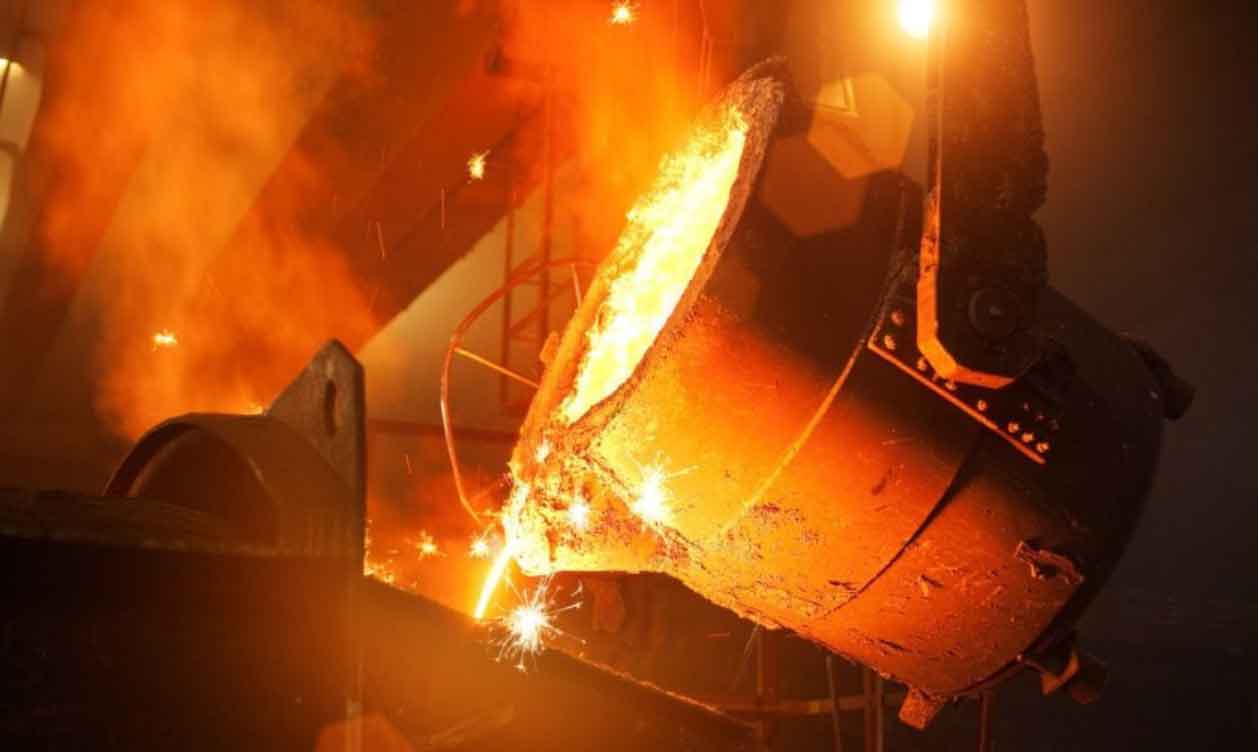
- Design and Engineering: The process starts with detailed design and engineering. Manufacturers work closely with engineers and designers to develop robust casting designs, ensuring that the product meets the required specifications and performance standards. This includes selecting appropriate materials, determining the gating system, and optimizing the casting process.
- Raw Material Selection: High-quality raw materials are essential for producing consistent and excellent steel castings. Manufacturers carefully select and source raw materials from trusted suppliers who meet specific quality standards. The chemical composition, cleanliness, and mechanical properties of the raw materials are thoroughly tested and verified.
- Process Control: Manufacturers implement strict process controls to monitor and control each stage of the casting process. This includes controlling the temperature, humidity, and other environmental factors to ensure consistent results. Process parameters, such as pouring temperature, solidification time, and cooling rate, are closely monitored and adjusted as necessary to optimize the casting quality.
- Quality Control Testing: Regular quality control testing is performed at various stages of the manufacturing process. This includes non-destructive testing (NDT), such as radiographic testing, ultrasonic testing, and magnetic particle testing, to detect any internal defects. Additionally, physical and mechanical tests, such as tensile strength, hardness, and impact resistance, are conducted to ensure the casting’s mechanical properties meet the required standards.
- Inspection and Dimensional Control: Visual inspection and dimensional control are critical to ensure the dimensional accuracy and surface finish of steel castings. Manufacturers employ techniques like coordinate measuring machines (CMM), 3D scanning, and precision gauges to verify the dimensions and tolerances of the castings.
- Documentation and Traceability: Manufacturers maintain comprehensive documentation throughout the production process. This includes recording all process parameters, inspection results, and any deviations from the standards. The traceability of raw materials, process steps, and inspection records allows manufacturers to identify and rectify any issues that may arise.
- Continuous Improvement: Manufacturers strive for continuous improvement by analyzing data, identifying trends, and implementing corrective actions. They actively monitor and review their quality control processes, seeking ways to optimize efficiency and enhance product quality.
- Certifications and Standards: Manufacturers often pursue certifications and adhere to international standards, such as ISO 9001, ISO 14001, and ISO/TS 16949. Compliance with these certifications and standards ensures that the manufacturing processes and quality management systems meet recognized industry benchmarks.
By implementing these strategies and processes, manufacturers can ensure consistency and excellence in steel casting manufacturing. Through a combination of robust design, rigorous quality control, and continuous improvement, they strive to deliver high-quality steel castings that meet customer expectations and industry standards.