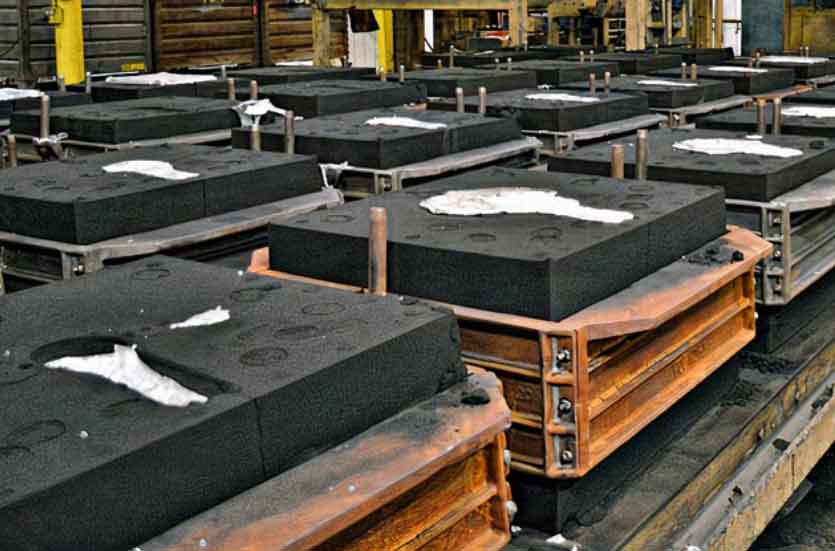
Resin sand casting technology has seen significant advancements in recent years, revolutionizing the industry and expanding its capabilities. These advancements have led to improved quality, efficiency, and design possibilities. Here are some notable advancements in resin sand casting technology:
- Digital Design and Simulation: The integration of advanced computer-aided design (CAD) and simulation software has revolutionized the design phase of resin sand casting. Engineers can create complex geometries, optimize part designs, simulate casting processes, and predict potential defects before actual production. This helps reduce iterations, improve casting quality, and save time and cost.
- Additive Manufacturing for Patterns: Additive manufacturing, such as 3D printing, is increasingly used to produce patterns for resin sand casting. This technology allows for faster pattern production, design iterations, and customization. 3D-printed patterns offer design flexibility, intricate details, and complex geometries that were previously challenging to achieve with traditional pattern-making techniques.
- Improved Mold Materials: Advancements in mold materials have enhanced the durability and dimensional stability of resin sand molds. High-quality resin binders and additives provide better mold strength, reduced mold degradation, and improved resistance to high temperatures and mechanical stresses. These improvements contribute to higher-quality castings and longer mold life.
- Automation and Robotics: The implementation of automation and robotics in resin sand casting processes has increased efficiency and productivity. Automated systems are used for mold handling, sand preparation, pouring, and shakeout processes, reducing manual labor, improving consistency, and minimizing cycle times.
- In-line Quality Control Systems: Advanced sensors, monitoring devices, and in-line quality control systems are used to monitor critical parameters during resin sand casting processes. Real-time data collection and analysis help detect variations, identify potential defects, and ensure consistent casting quality. These systems enable immediate corrective actions, reducing scrap rates and improving overall process control.
- Environmental Sustainability: The resin sand casting industry has made strides in adopting environmentally friendly practices. This includes the use of environmentally friendly binders and additives, as well as improved waste management and recycling processes. The aim is to reduce emissions, minimize waste generation, and enhance overall sustainability in resin sand casting operations.
- Smart Manufacturing and IoT Integration: Resin sand casting is becoming part of the broader smart manufacturing landscape. Integration with the Internet of Things (IoT) enables real-time data monitoring, remote control, predictive maintenance, and optimization of process parameters. This enhances production efficiency, quality control, and overall operational effectiveness.
- Advanced Non-Destructive Testing (NDT) Techniques: Advanced non-destructive testing techniques, such as computed tomography (CT) scanning and digital radiography, are being employed to inspect resin sand castings. These techniques provide detailed internal and external imaging, enabling precise defect detection and analysis without damaging the castings. This ensures higher casting quality and reduces the need for destructive testing methods.
These advancements in resin sand casting technology have transformed the industry by improving casting quality, reducing costs, and expanding design possibilities. Manufacturers can now produce more complex, precise, and high-quality castings with greater efficiency and sustainability. Continued research and development in resin sand casting technology will likely lead to further innovations, making it an even more attractive casting method for a wide range of industries.