Sand casting, despite being a traditional manufacturing method, has seen advancements and innovations that have improved its efficiency, accuracy, and overall quality. Here are some notable advancements in sand casting:
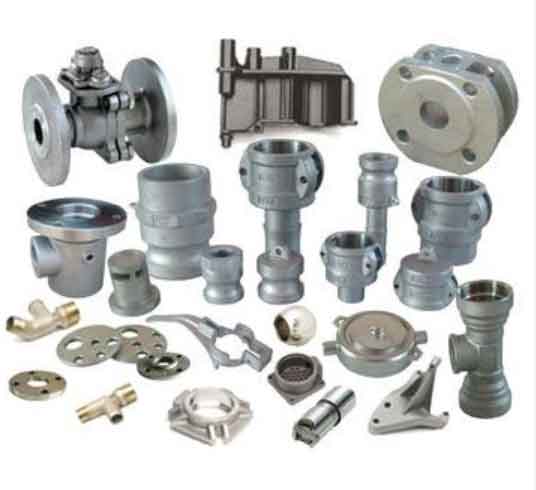
- Digital Design and Simulation:
- Computer-aided design (CAD) and computer-aided engineering (CAE) software have revolutionized the design and simulation of sand castings.
- Advanced software tools allow for 3D modeling and simulation of the casting process, including mold filling, solidification, and cooling.
- Digital simulations help optimize gating and riser designs, identify potential defects, and ensure better quality control.
- Additive Manufacturing for Patterns and Cores:
- Additive manufacturing, also known as 3D printing, has found applications in sand casting for the production of patterns and cores.
- 3D-printed patterns offer greater design freedom, allowing for the creation of intricate geometries and complex part shapes.
- 3D-printed sand cores can be produced with precise dimensions and internal cavities, enabling the casting of more intricate parts.
- Improved Sand Mixtures and Binders:
- The composition of sand mixtures and binders used in sand casting has improved, leading to better mold quality and dimensional accuracy.
- Advanced binders and additives have enhanced the strength, thermal stability, and collapsibility of sand molds.
- The use of environmentally friendly and sustainable binders has also gained attention, reducing the environmental impact of sand casting.
- Advanced Molding Techniques:
- Modern molding techniques, such as vacuum molding or precision sand control, have improved mold quality and surface finish.
- Vacuum molding ensures a denser and more uniform packing of sand around the pattern, resulting in improved mold strength and dimensional accuracy.
- Precision sand control techniques provide tighter control over sand properties, leading to better mold surface finish and reduced casting defects.
- Non-Destructive Testing (NDT) Methods:
- Non-destructive testing techniques have advanced, allowing for more accurate and efficient inspection of castings.
- X-ray inspection, ultrasound testing, and other advanced NDT methods are used to detect internal defects like porosity or inclusions.
- These methods help ensure the integrity and quality of castings without the need for destructive testing.
- Robotics and Automation:
- Robotics and automation have been introduced to various stages of the sand casting process, improving efficiency and consistency.
- Automated processes, such as sand mold preparation, pouring, and shakeout, reduce labor requirements and enhance process control.
- Robots can perform repetitive tasks with precision, leading to improved casting quality and reduced cycle times.
- Sustainable Practices:
- The sand casting industry has also embraced sustainable practices to minimize environmental impact.
- Efforts are being made to reduce sand consumption through improved sand reclamation and recycling techniques.
- Energy-efficient furnaces, waste management systems, and cleaner production practices contribute to a more sustainable sand casting process.
These advancements in sand casting have enhanced its capabilities, efficiency, and overall quality. The integration of digital design and simulation, additive manufacturing, improved materials, advanced molding techniques, non-destructive testing methods, automation, and sustainable practices have all contributed to making sand casting a more reliable and technologically advanced manufacturing method.