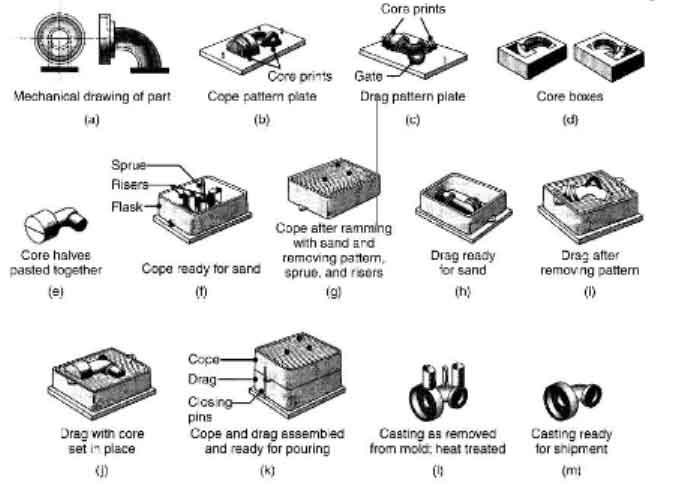
In recent years, there have been advancements in sand casting technologies aimed at improving the process efficiency, quality, and capabilities. Here are some notable advancements in sand casting part technologies:
3D Printing and Additive Manufacturing:
The integration of 3D printing and additive manufacturing techniques has revolutionized sand casting. 3D printing allows for the creation of intricate sand molds and cores directly from digital designs, eliminating the need for traditional pattern-making. This technology enables faster prototyping, complex geometries, and reduced lead times.
Digital Design and Simulation:
Computer-aided design (CAD) and simulation software have significantly enhanced sand casting processes. Advanced software tools allow designers to create and optimize complex part designs, simulate mold filling and solidification, and predict defects like porosity and shrinkage. This digital design and simulation approach improve the accuracy and efficiency of the casting process.
Rapid Pattern Making:
Traditional pattern-making techniques can be time-consuming and costly. However, advancements in rapid pattern-making technologies, such as CNC machining and rapid prototyping, have reduced the time and cost involved in producing high-quality patterns. These techniques enable faster pattern iteration and customization, reducing the overall lead time for sand casting production.
Binder Systems:
Sand casting traditionally uses clay-based binders to hold the sand particles together. However, advancements in binder systems have led to the development of alternative materials like synthetic resins and organic binders. These modern binder systems offer improved dimensional accuracy, better surface finish, reduced environmental impact, and enhanced mold stability during casting.
Sand Reclamation:
Sand reclamation technologies have gained prominence due to the increasing emphasis on sustainable and eco-friendly manufacturing practices. Sand used in casting processes can be reclaimed, treated, and reused, reducing the consumption of new sand and minimizing waste. Various techniques, such as mechanical, thermal, and chemical reclamation, are employed to regenerate the sand for multiple casting cycles.
Real-Time Process Monitoring:
Advanced sensors and monitoring systems are being implemented in sand casting to provide real-time data on process parameters like temperature, pressure, and humidity. This data helps optimize the casting process, ensure consistency in quality, and detect any deviations or defects during production. Real-time monitoring enables proactive adjustments, reducing scrap rates and improving overall process efficiency.
Automation and Robotics:
Automation and robotics are increasingly being adopted in sand casting operations to improve productivity, precision, and repeatability. Automated systems can handle tasks like mold handling, pouring, and post-casting operations. Robotic systems offer greater flexibility, speed, and accuracy in handling complex molds and performing intricate tasks, enhancing overall process efficiency.
These advancements in sand casting technologies have led to increased productivity, improved quality control, and reduced lead times in the production of sand cast parts. They have also expanded the design possibilities, enabling the manufacturing of complex, lightweight, and optimized components. As these technologies continue to evolve, sand casting is expected to remain a relevant and competitive manufacturing method in various industries.