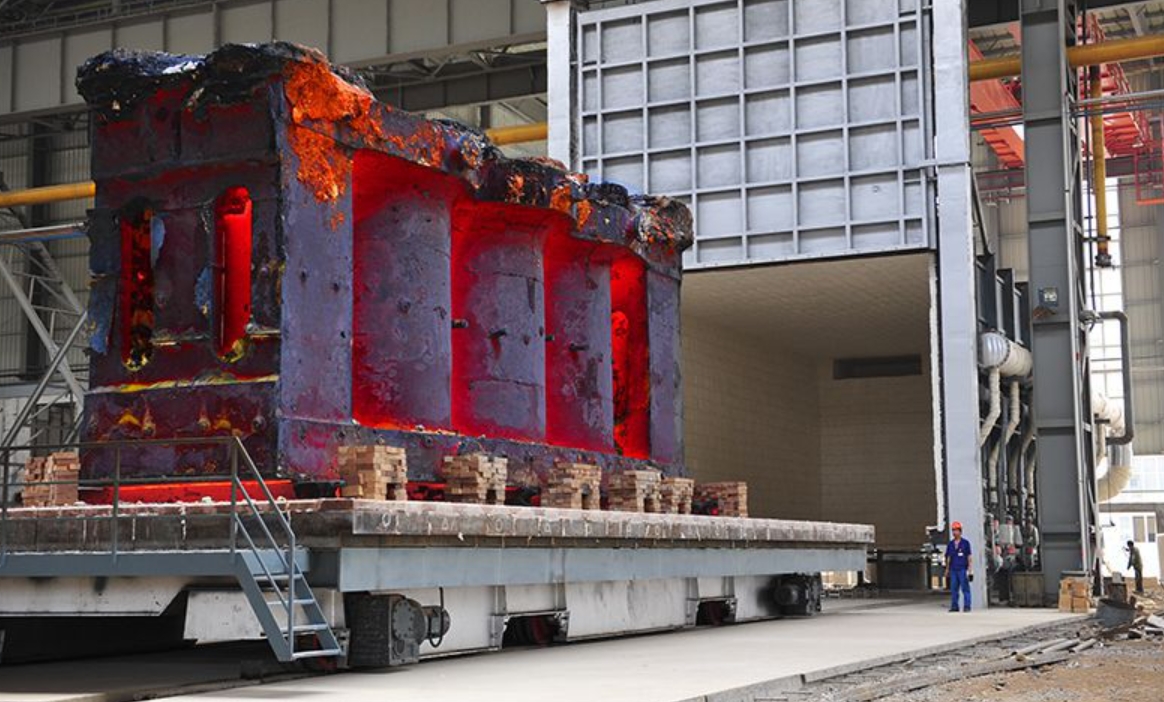
Advancements in the quality control of large steel castings are a crucial aspect of modern manufacturing and metallurgy. These advancements often revolve around the following areas:
- Improved Inspection Techniques: The development of advanced non-destructive testing (NDT) methods, such as ultrasonic testing, radiography, and magnetic particle inspection, has greatly enhanced the ability to detect internal and surface defects in large steel castings.
- Enhanced Material Quality: The formulation of better steel alloys, with controlled amounts of carbon, manganese, silicon, and other elements, improves the overall quality of the castings. This includes developing more homogenous and refined grain structures that enhance the mechanical properties of large steel castings.
- Advanced Casting Technologies: Methods such as vacuum casting, continuous casting, and controlled cooling have revolutionized the casting process. These technologies help in reducing defects like porosity, cracks, and inclusions.
- Digitalization and Automation: Incorporating digital technologies, such as computer-aided design (CAD) and computer-aided manufacturing (CAM), along with automated casting processes, allows for more precise control over the casting process, leading to higher quality products.
- Quality Control Software: Software for process monitoring and quality control helps in tracking the entire casting process, ensuring adherence to specifications and standards.
- Environmental and Safety Standards Compliance: Advancements in ensuring that the casting process is environmentally friendly and safe for workers are also considered a part of quality control.
- Simulation and Modeling: Using advanced simulation software to predict how large steel castings will behave during the casting process, enabling adjustments to be made beforehand to avoid defects.
- Data Analytics: The use of big data and predictive analytics to analyze historical data and predict potential issues in the casting process, leading to proactive quality control.
- Collaboration and Integration: Greater collaboration between different stages of production, from raw material selection to the final inspection, ensures comprehensive quality control.
- Customization and Flexibility: Ability to customize the casting process for specific applications, accommodating unique shapes, sizes, and properties required by various industries.
These advancements not only improve the quality of large steel castings but also contribute to higher efficiency, reduced waste, and better sustainability in the manufacturing process.