Custom large steel castings tailored to specific industry needs are essential in various sectors, each with unique requirements and challenges. These customizations typically revolve around the following aspects:
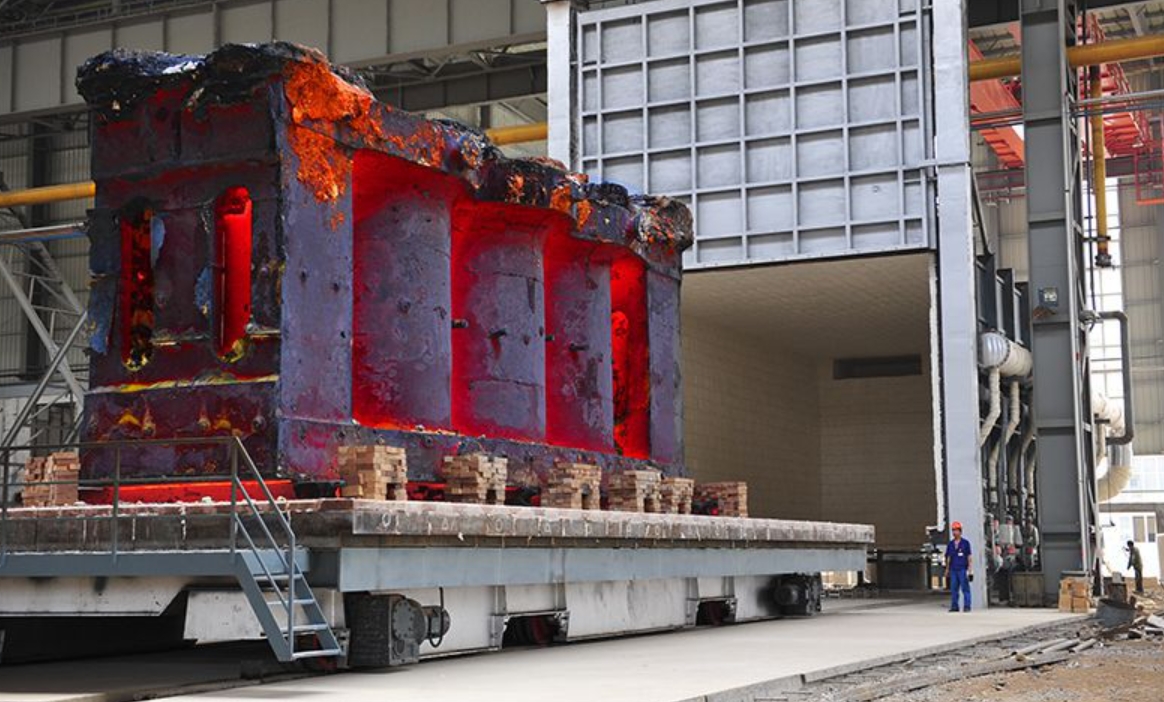
- Material Customization: Depending on the industry and application, the steel alloy’s composition is adjusted to provide the necessary strength, corrosion resistance, heat tolerance, or wear resistance. For example, stainless steel might be used for corrosion resistance in marine applications, while high-carbon steels might be chosen for their strength in construction.
- Design and Engineering: Custom castings require specialized design to meet specific functional requirements. This could include complex shapes or integrated features that reduce the need for additional fabrication or assembly. Engineering for custom castings also often involves detailed analysis to ensure performance under specific operating conditions.
- Precision and Tolerances: Industries such as aerospace, automotive, and defense often require extremely high precision and tight tolerances. Achieving these in large castings involves advanced manufacturing techniques and meticulous quality control.
- Size and Weight Considerations: Depending on the application, custom castings might need to be exceptionally large or particularly lightweight. This requires careful planning in the casting process to ensure uniform quality and structural integrity, regardless of size or weight.
- Surface Treatments and Finishing: Different industries may require specific surface treatments for their castings, like heat treatments, coating, or surface hardening, to enhance properties like hardness, resistance to wear or environmental factors.
- Testing and Certification: Many industries require extensive testing and certification to ensure that the custom castings meet rigorous industry-specific standards. This could include mechanical testing, non-destructive testing, and industry-specific compliance verification.
- Integration with Other Systems: In many cases, large steel castings need to integrate seamlessly with other components or systems. This requires precise manufacturing and often collaboration with the client to ensure compatibility.
- Prototyping and Modeling: Advanced techniques like 3D modeling and prototyping are often used to create and verify designs before full-scale production begins. This helps in identifying potential issues and making adjustments early in the process.
- Sustainability and Environmental Compliance: Custom casting processes are increasingly being designed to minimize environmental impact, through efficient use of resources, recycling of materials, and reduction of emissions.
- Logistics and Installation Support: For large custom castings, providing logistical support for transportation and installation is often a part of the service, given the challenges in handling and installing these massive components.
Custom large steel castings are integral in sectors like energy (including renewables), maritime, infrastructure, mining, heavy machinery, transportation, and defense. Each industry’s specific needs shape the approach to designing, manufacturing, and finishing these essential components.