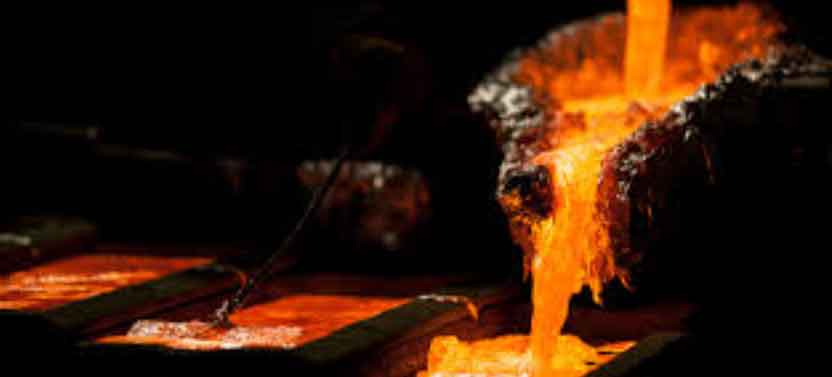
The sand casting process is a widely used and established method for manufacturing complex metal parts. While it has been around for centuries, there have been several advancements and innovations in recent years that have improved the efficiency, precision, and overall quality of sand casting. Here are some notable advancements in the sand casting process:
Digital Design and Simulation:
The integration of computer-aided design (CAD) and simulation software has revolutionized the sand casting process. Designers can create intricate part geometries and simulate the casting process digitally, allowing for optimization of the mold design, gating system, and metal flow. This technology helps identify potential defects and optimize the casting parameters before physical production, saving time and costs.
3D Printing of Sand Molds and Cores:
Additive manufacturing, specifically 3D printing, has been successfully applied to sand casting. Instead of manually producing molds and cores, 3D printing technology allows for the direct printing of sand molds and cores based on digital designs. This method enables greater design flexibility, faster turnaround times, and reduced costs compared to traditional mold-making techniques.
Advanced Sand Binders:
The binders used in sand casting have seen significant advancements. New binder systems provide improved strength, stability, and collapsibility of the sand mold or core. These advancements enhance the dimensional accuracy of the cast parts and reduce the likelihood of defects like sand burn-in or sand expansion.
Real-time Monitoring and Control:
Sensors and monitoring systems are being employed to gather data during the casting process. Temperature, pressure, and other parameters can be monitored in real time to ensure optimal process conditions and detect any deviations that may lead to defects. This data-driven approach enables better control and consistency in the casting process, resulting in higher-quality parts.
Automation and Robotics:
Automation technologies and robotics are being integrated into sand casting operations to improve efficiency and reduce manual labor. Robotic systems can handle tasks such as mold assembly, pouring molten metal, and removing finished castings. This automation not only enhances productivity but also minimizes the risk of injuries associated with manual handling of heavy molds and castings.
Advanced Alloys and Materials:
The development of new alloys and materials suitable for sand casting has expanded the range of applications. High-performance alloys with improved mechanical properties, heat resistance, or corrosion resistance can now be effectively cast using the sand casting process. These advancements have opened up opportunities for sand casting in industries such as aerospace, automotive, and defense.
Sustainable Practices:
Environmental concerns have led to innovations in sustainable practices in the foundry industry. Efforts are being made to reduce waste generation, improve energy efficiency, and develop greener sand binders and coatings. Recycling and reusing sand, minimizing emissions, and adopting eco-friendly technologies are becoming integral parts of modern sand casting operations.
These advancements in the sand casting process have made it more precise, efficient, and environmentally friendly. The integration of digital technologies, 3D printing, advanced materials, and automation has transformed sand casting into a highly competitive and versatile manufacturing method.