Chapter 1 : The Introduction of Investment Casting
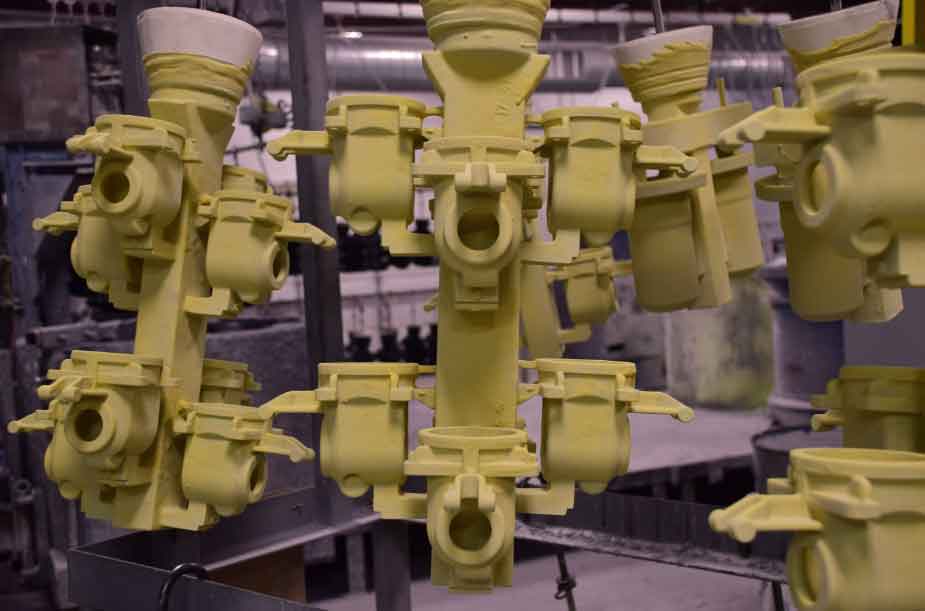
The so-called investment casting process , it is simply said that use fusible material fusible model covered with several layers of special refractory coating in the model surface, after drying and hardening to form a whole body shell, then steam or hot water from type shell model melt away , and then placed in the shell sand box , after filling the dry sand molding around it , and finally it is cast into the roaster in the high-temperature roasting, mold or shell after roasting, in which pouring molten metal and casting finally obtained.

The biggest advantage of investment casting is that due to the investment casting with high dimensional accuracy and surface finish, so it can reduce mechanical processing work, just in the component parts of the high demand for a little machining allowance, and even some castings only grinding, polishing allowance, don’t need to machining can be used. Using investment casting method, therefore, can save a lot of machine tool equipment and processing time, and greatly save metal materials. Another advantage of the method of investment casting is that it may be cast complex castings of various alloys, particularly may be cast super alloy castings. Such as jet engine blades, with the machining process its sleek outline and cooling cavity is almost impossible to form. Investment casting process to produce not only mass production can be done to ensure the consistency of the casting, and avoid stress concentration of residual knife pattern after machining.
The available investment casting production of alloy types include carbon steel, alloy steel, heat-resistant alloy, stainless steel, precision alloy, permanent magnet alloy, bearing alloy, copper alloy, aluminum alloy, titanium alloy and nodular cast iron etc.. Investment casting process is complicated, and not easy to control, use and consumption of material is expensive, so it is suitable for production of complex shape, high precision, or difficult to other processing of small parts, such as turbine engine.
Investment casting, also known as the lost-wax casting process, is a precision casting technique used to create intricate and complex metal parts with high dimensional accuracy and fine surface finishes. This process is particularly suitable for producing parts that are challenging to manufacture using traditional methods. Here’s an introduction to the investment casting process:
1. Pattern Creation: The investment casting process begins with the creation of a wax or other suitable material pattern that replicates the shape of the desired final metal part. The pattern can be made through injection molding, machining, or other methods. These patterns are often attached to a wax gating system to form an assembly called a “wax tree.”
2. Assembly: Multiple wax patterns, along with their gating systems, are attached to a central sprue (pouring channel) to create a cluster of patterns known as the “wax tree.” This assembly allows multiple parts to be cast in a single casting cycle.
3. Shell Building: The wax tree is coated with a ceramic slurry or refractory material, often in multiple layers. After each layer is applied, it is dried or cured to create a ceramic shell around the wax pattern. This shell is built up until it reaches a desired thickness, creating a mold.
4. Dewaxing (Wax Removal): The ceramic shell mold is then heated in an autoclave or furnace to melt and remove the wax pattern, leaving behind a cavity in the shape of the original wax pattern within the ceramic shell. This step is where the term “lost-wax” comes from.
5. Preheating: After wax removal, the ceramic shell is preheated to a temperature that prepares it for the incoming molten metal and prevents thermal shock during casting.
6. Casting: Molten metal, often heated in an induction furnace or other specialized melting equipment, is poured into the preheated ceramic shell mold. The metal fills the cavity left by the wax pattern, taking its shape.
7. Cooling and Solidification: The molten metal solidifies within the ceramic shell mold as it cools. This process allows the metal to take on the intricate details and features of the original wax pattern.
8. Shell Removal: After the metal has cooled and solidified, the ceramic shell is carefully broken away, revealing the metal casting.
9. Finishing: The casting may require some post-casting operations such as removal of excess material, machining, heat treatment, surface treatments, and quality inspection to ensure it meets the desired specifications.
Chapter 2 : The Advantage and Disadvantage of Investment Casting
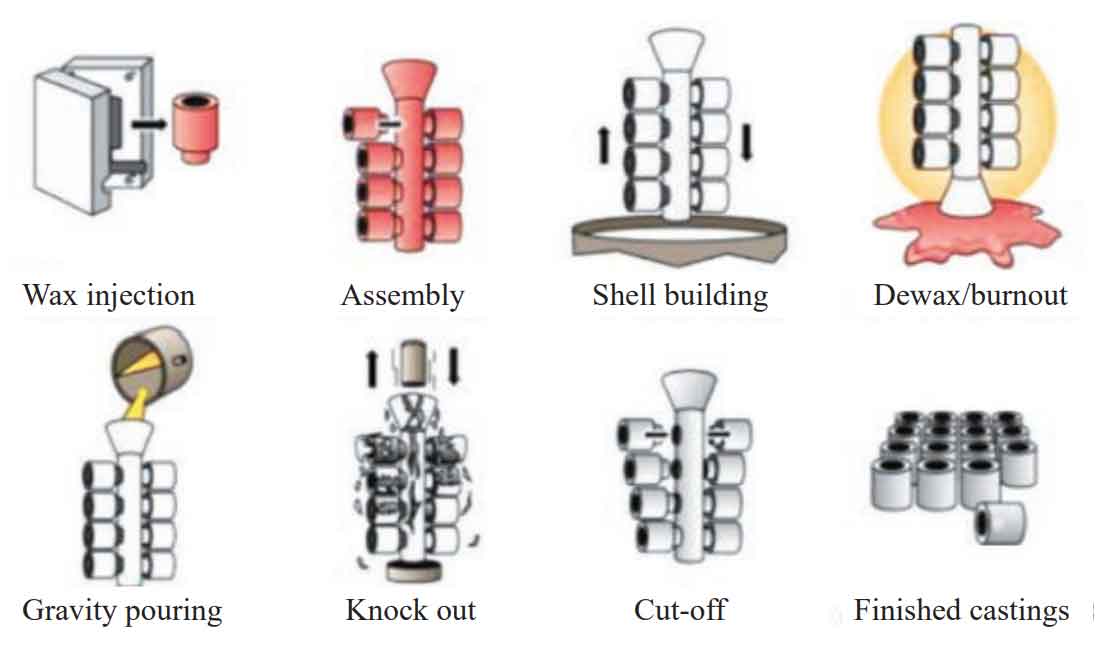
Investment casting, also known as lost-wax casting, offers several advantages and disadvantages. Understanding these pros and cons can help you determine whether this casting process is suitable for your specific manufacturing needs. Here’s a breakdown of the advantages and disadvantages of investment casting:
Advantages of Investment Casting:
- Complex Geometries: Investment casting is capable of producing intricate and complex shapes that would be difficult or impossible to achieve using other casting methods.
- High Dimensional Accuracy: The process results in tight tolerances and high precision, reducing the need for extensive post-casting machining.
- Excellent Surface Finish: Investment casting provides smooth surface finishes that often require minimal additional polishing or finishing.
- Versatility in Materials: A wide range of metals and alloys, including stainless steel, aluminum, titanium, and more, can be used in investment casting.
- Reduced Material Wastage: Investment casting generates minimal waste material compared to traditional machining methods.
- Variety of Sizes: Investment casting can accommodate a wide range of part sizes, from small intricate components to larger items.
- Casting Multiple Parts: Multiple parts can be cast together in a single tree, improving production efficiency.
- Reduced Tooling Costs: Complex tooling required in other casting methods is often unnecessary in investment casting, leading to cost savings.
- Intricate Details: Fine details, undercuts, and thin walls can be replicated accurately in the final casting.
- Near Net Shape: Investment casting often produces parts that are very close to the final shape, minimizing machining requirements.
Disadvantages of Investment Casting:
- Cost: The investment casting process can be more expensive than some other casting methods due to the multiple steps involved, including creating wax patterns, building ceramic shells, and post-casting finishing.
- Time-Consuming: The process involves several stages, including pattern creation, shell building, casting, and finishing, which can result in longer lead times compared to faster casting methods.
- Limited Production Rates: Investment casting may not be suitable for high-volume production due to its time-consuming nature and higher costs.
- Size Limitations: While investment casting can handle a variety of sizes, extremely large parts may be challenging to cast using this method.
- Complexity of Process: The process involves multiple steps and specialized equipment, requiring skilled operators and strict process control.
- Fragile Molds: The ceramic shells used in investment casting can be delicate and susceptible to damage, leading to potential defects.
- Quality Consistency: Maintaining consistent shell quality and achieving uniform casting results can be challenging.
- High Temperature Requirements: The process requires heating the ceramic shell to high temperatures, which can be energy-intensive.
Investment casting is a versatile and precise casting method that is well-suited for creating intricate and high-quality metal parts. However, its advantages and disadvantages should be carefully considered based on the specific requirements of your project. If the benefits align with your needs and you’re willing to manage the potential drawbacks, investment casting can be an excellent choice for producing complex and detailed components.
Chapter 3 : The Application of Investment Casting
Investment casting, also known as lost-wax casting, is a versatile manufacturing process that finds applications in a wide range of industries due to its ability to create intricate and complex metal parts with high precision and quality. Here are some key industries and applications where investment casting is commonly used:
- Aerospace Industry:
- Turbine blades and vanes for aircraft engines.
- Structural components for aircraft and spacecraft.
- Aerospace fasteners and fittings.
- Automotive Industry:
- Engine components such as cylinder heads, intake manifolds, and exhaust components.
- Suspension and steering components.
- Transmission and gearbox parts.
- Medical and Dental Industry:
- Orthopedic implants such as hip and knee joints.
- Dental prosthetics, crowns, and bridges.
- Surgical instruments.
- Industrial and Machinery:
- Pumps and valves.
- Gears, gearboxes, and industrial machinery components.
- Hydraulic and pneumatic components.
- Energy Industry:
- Turbine components for power generation.
- Oil and gas industry components such as valves and fittings.
- Renewable energy components.
- Jewelry Industry:
- High-quality jewelry and decorative pieces.
- Intricate designs and patterns.
- Firearms and Defense Industry:
- Firearm components like triggers, hammers, and receivers.
- Military and defense equipment.
- Art and Sculpture:
- Casting sculptures and artistic pieces with fine details.
- Replication of art pieces for museums and exhibitions.
- Marine Industry:
- Marine engine components.
- Propellers and underwater equipment.
- Electronics Industry:
- Connectors and housings for electronic devices.
- Heat sinks and other specialized components.
- Instrumentation Industry:
- Precision components for measuring instruments.
- Optics and optical components.
- Food Processing and Packaging:
- Food processing machinery components.
- Packaging machinery parts.
Investment casting’s ability to produce complex shapes with high precision, tight tolerances, and excellent surface finishes makes it an ideal choice for applications that require intricacy, detail, and a high degree of customization. Additionally, the process is well-suited for both small-scale production of highly specialized parts and larger production runs. The wide range of metals and alloys that can be used in investment casting further enhances its versatility and applicability across various industries.
Chapter 4 :The investment casting process
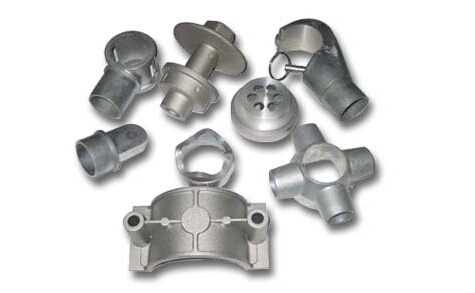
The investment casting process, also known as lost-wax casting, is a manufacturing technique used to create complex and intricate metal parts with high precision and quality. The process involves several steps, from pattern creation to the final casting. Here’s a detailed overview of the investment casting process:
1. Pattern Creation:
- The process begins with the creation of a wax or similar material pattern that replicates the shape of the desired final metal part.
- Patterns can be made through injection molding, machining, or other methods.
- Multiple patterns are often attached to a gating system to form a cluster called a “wax tree.”
2. Assembly:
- The wax patterns, along with their gating systems, are attached to a central sprue (pouring channel), forming a tree-like assembly.
- This assembly allows multiple parts to be cast in a single casting cycle, optimizing efficiency.
3. Shell Building:
- The wax tree is coated with a ceramic slurry or refractory material, often in multiple layers.
- After each layer is applied, it is dried or cured to create a ceramic shell around the wax pattern.
- The shell is built up until it reaches the desired thickness, creating the mold for casting.
4. Dewaxing (Wax Removal):
- The ceramic shell mold is heated in an autoclave or furnace to melt and remove the wax pattern. This step is also known as “dewaxing” or “burnout.”
- The molten wax flows out of the shell, leaving behind a cavity in the shape of the original wax pattern.
5. Preheating:
- After wax removal, the ceramic shell is preheated to a temperature that prepares it for the incoming molten metal and prevents thermal shock during casting.
6. Casting:
- Molten metal, often heated in an induction furnace or other specialized melting equipment, is poured into the preheated ceramic shell mold.
- The metal fills the cavity left by the wax pattern, taking its shape.
7. Cooling and Solidification:
- The molten metal solidifies within the ceramic shell mold as it cools. This process allows the metal to take on the intricate details and features of the original wax pattern.
8. Shell Removal:
- After the metal has cooled and solidified, the ceramic shell is carefully broken away, revealing the metal casting.
- Some cleaning and finishing processes may be required to remove any residual shell material and prepare the casting for use.
9. Finishing:
- Depending on the part’s requirements, post-casting operations such as machining, polishing, heat treatment, surface coatings, and quality inspection are performed.
Investment casting offers a balance between intricate detailing and high precision, making it suitable for applications where tight tolerances and excellent surface finishes are essential. While the process involves several steps and can be relatively time-consuming, its ability to create complex geometries with minimal material wastage makes it a preferred choice in various industries, including aerospace, automotive, medical, and more.