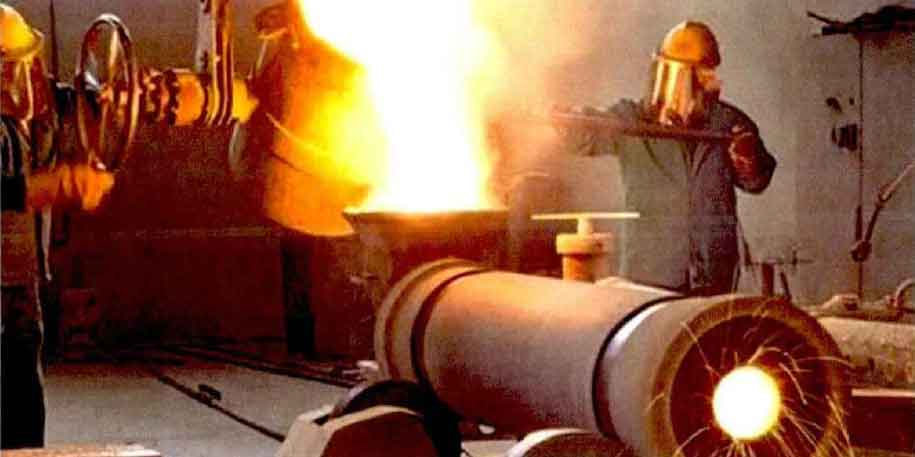
As a special casting method, centrifugal casting has the following advantages compared with traditional sand casting:
(1) Hollow cylindrical and annular castings and cast pipes with different diameter and length can be cast without sand core, with high production efficiency and low production cost.
(2) Some castings do not need any riser, so the utilization rate of liquid metal is improved. Taking centrifugal ductile iron pipe as an example, only 1040kg molten iron is consumed for 1t casting pipe, that is to say, the yield exceeds 96% (including the loss of waste products).
(3) The liquid metal solidifies under centrifugal force and has fine structure. The lighter slag, oxide and other inclusions will float out of the liquid metal body under the centrifugal force and remain on the inner surface, which can be removed by mechanical processing, so as to ensure the high performance requirements of engine cylinder liner and other castings.
(4) Bimetallic castings of different metals, such as rolls and flour grinding rolls, can be cast to make the parts hard on the outside and hard on the inside, with better performance.
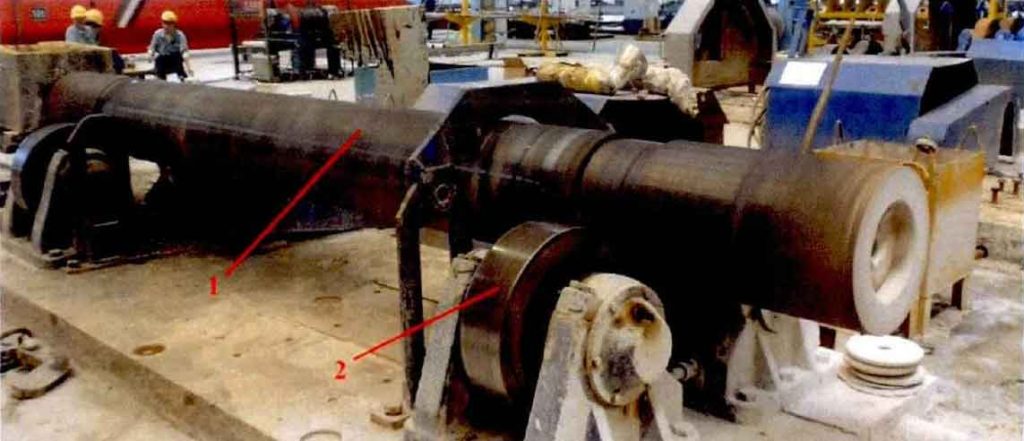
However, centrifugal casting also has some shortcomings
(1) The true centrifugal casting process is only suitable for hollow axisymmetric castings, but there are not many kinds of such castings.
(2) Centrifugal casting needs to use complex centrifugal casting machine, generally its price is very expensive, so the investment of centrifugal casting workshop is more than other casting methods.
(3) Due to the effect of centrifugal force, it is easy to cause density segregation in the solidification process of some molten metal. When the centrifugal ductile iron pipe is cast, if the carbon equivalent is too high, the graphite will segregate inward.
(4) The inner surface formed by centrifugal force is rough, so it can not be used directly.
It can be seen from the above advantages and limitations that centrifugal casting is suitable for specific, mass production and hollow axisymmetric castings.