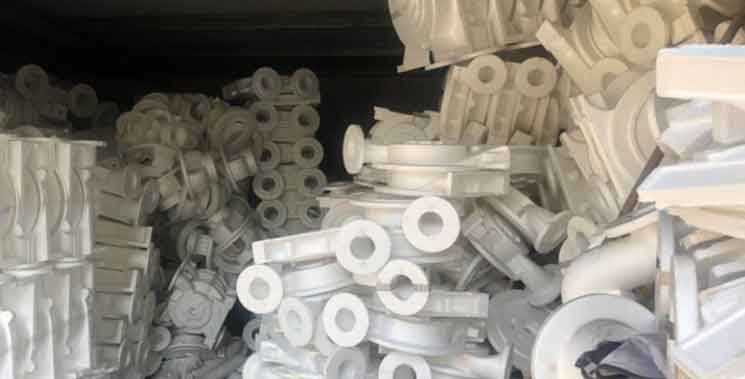
Lost foam casting offers several advantages that make it an attractive choice for many manufacturers:
- Efficiency: Lost foam casting is a highly efficient process compared to traditional casting methods. It eliminates the need for pattern-making and core-making, reducing production time and costs.
- Cost-effectiveness: The elimination of pattern-making and core-making results in cost savings, as there are fewer materials and labor required for the casting process.
- Design Freedom: Lost foam casting allows for intricate and complex designs with tight tolerances to be easily achieved. The foam patterns can be precisely shaped using CNC machines or 3D printers, enabling the production of detailed and custom parts.
- Near-Net-Shape Casting: Lost foam casting produces near-net-shape castings, which means that the final components require minimal additional machining or finishing. This reduces material waste and machining costs.
- Lightweight Designs: Lost foam casting is ideal for creating lightweight components with thin walls. The foam patterns can be designed with hollow sections or internal cavities, resulting in lightweight yet strong castings.
- Versatility: Lost foam casting can be used to cast a wide range of metals, including aluminum, iron, steel, and various alloys. This versatility makes it suitable for diverse applications.
- Reduced Environmental Impact: The process generates less waste compared to traditional casting methods, contributing to a more environmentally friendly production process.
- Consistency and Reproducibility: Lost foam casting offers high accuracy and repeatability, ensuring consistent quality in the final castings.
- Improved Surface Finish: The use of foam patterns with smooth surfaces can result in better surface finish on the final castings.
- Minimal Draft Angles: Lost foam casting allows for the creation of parts with minimal draft angles, which can be advantageous for specific applications.
- Reduced Tooling Costs: Lost foam casting does not require expensive tooling for patterns and cores, making it cost-effective for low to medium production volumes.
- Integration of Components: Complex shapes and multiple components can be integrated into a single foam pattern, simplifying the assembly process and reducing the number of individual parts.
Lost foam casting provides a competitive edge to manufacturers seeking efficient, cost-effective, and flexible solutions for producing complex and high-quality metal components.