Resin sand casting offers numerous advantages that contribute to its popularity in the manufacturing industry. This casting method delivers both quality and cost efficiency, making it an attractive choice for producing metal parts. Here are the key advantages of resin sand casting:
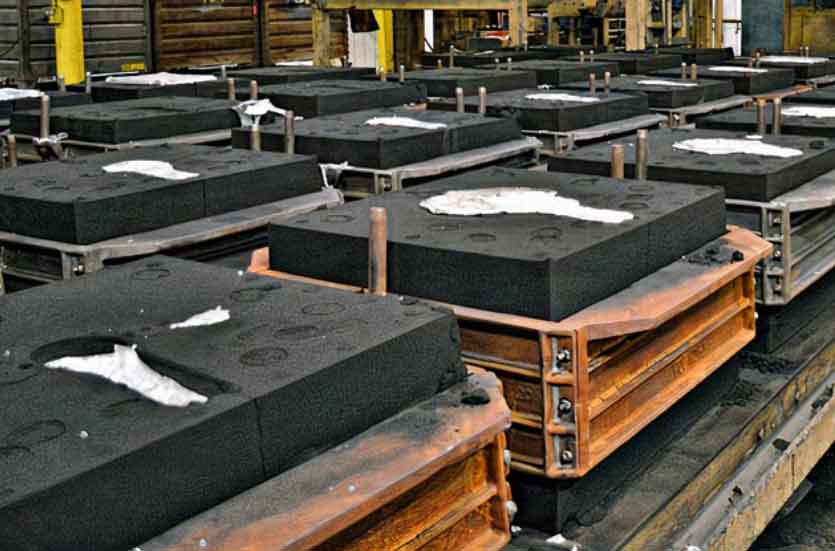
1. Versatility: Resin sand casting is highly versatile and can be used to produce a wide range of complex metal parts with varying shapes, sizes, and intricacies. This flexibility makes it suitable for diverse industries and applications, accommodating the production of both small and large castings.
2. Precision and Dimensional Accuracy: The use of resin-coated sand and careful mold preparation results in castings with high precision and dimensional accuracy. This is especially important for components that require tight tolerances and consistent shapes.
3. Improved Surface Finish: Resin sand casting creates smoother mold surfaces, which directly translates to better surface finishes on the final castings. This can reduce the need for additional post-processing and finishing operations.
4. Cost-Effectiveness: Compared to other precision casting methods like investment casting or die casting, resin sand casting is often more cost-effective. The materials used, such as sand and resin binders, are generally less expensive than the specialized refractory materials required for other processes.
5. Reduced Defects: The combination of resin-coated sand and proper molding techniques reduces the likelihood of defects in the casting, such as sand inclusions or surface imperfections. This leads to higher yield rates and less material waste.
6. Shorter Lead Times: Resin sand casting typically has shorter lead times compared to processes that require more intricate tooling and molds. The relatively quick setup and preparation enable faster production cycles.
7. Suitable for Various Metals: Resin sand casting can be used with various types of metals, including ferrous and non-ferrous alloys. This adaptability allows manufacturers to choose the most suitable metal for their specific application.
8. Energy Efficiency: The solidification process in resin sand casting requires less energy compared to other casting methods that may involve higher temperatures or specialized equipment.
9. Complex Part Geometries: Resin sand casting is well-suited for producing parts with complex geometries and internal features. The use of expendable patterns allows for intricate designs and internal cores, enabling the creation of complex castings.
10. Low-Volume Production: Resin sand casting is an excellent option for low to medium volume production runs. It provides an economical solution for smaller quantities of parts without the need for costly tooling.
11. Environmental Considerations: Resin sand casting produces less hazardous waste compared to some other casting methods, making it a more environmentally friendly choice.
Resin sand casting strikes a balance between precision, versatility, and cost-effectiveness, making it an attractive option for a wide range of industries. It provides manufacturers with the ability to create intricate and high-quality metal parts while maintaining competitive production costs. However, as with any manufacturing process, it is essential to consider specific project requirements and limitations to determine if resin sand casting is the optimal choice.