Air tightness test, also known as sealing test, is an important indicator to judge whether there is internal defect in the axle housing by observing the change of bubbles after the axle housing is processed and sealed with tooling. After the axle housing is immersed in water under a certain pressure for a certain period of time, it is an important indicator for judging whether there is oil leakage and oil leakage in the axle housing. The test site is shown in Figure 1.
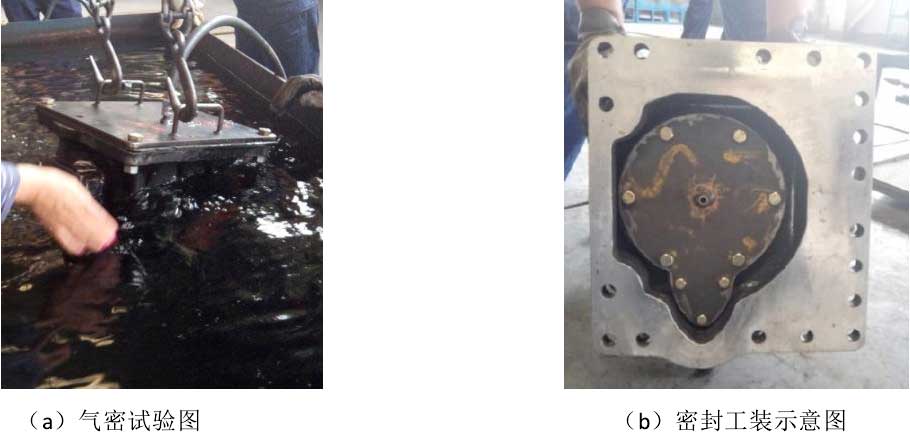
Restricted by economic conditions, this product adopts direct pressure test method. Its principle is: under stable environment, the test workpiece is inflated until the tested workpiece is full of gas. Then, close the pressure valve. Under the condition of relatively sealed test piece, within a certain period of time, through visual inspection to see whether there are bubbles, so as to judge whether the air tightness of the workpiece is good The workpiece is qualified, otherwise, the workpiece is unqualified.
(1) Clean the outer surface of the axle housing, remove the sludge, iron slag, etc. on the surface, and complete the preparation of the pressing tooling for the axle housing. The hydraulic test tooling for the axle housing is shown in Fig. 2. Hb-223 water-based antirust agent was added into the water for pressing, and the ratio of antirust agent: water was 1:10.
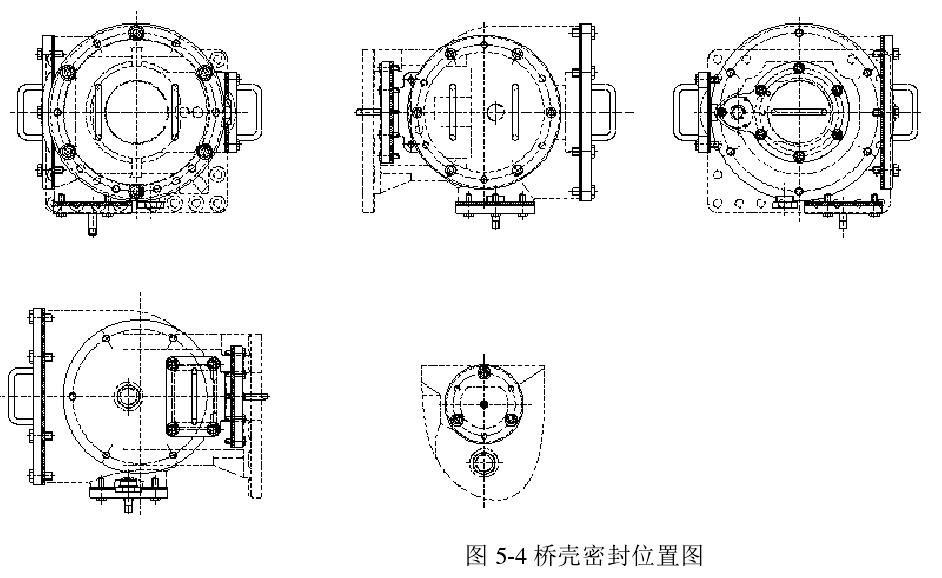
(2) As shown in Figure 2, the corresponding tooling of the axle housing is used to seal the connecting surfaces. When sealing, a rubber pad with a thickness of 6 mm is added to the contact surface of the axle housing and the tooling, and the rubber pad is fixed with bolts. A combination washer is added at the threaded through-hole for sealing. Add O-ring to seal the oil filling / discharging holes with the screw plug.
(3) Connect compressed air. One end of the gas pipe is connected to the connector on the tooling, and the other end is connected to the compressed air source on the pressure regulating valve to ensure that there is no air leakage in the connecting pipeline.
(4) Lifting and pressing. Lift the axle housing and tooling components to the top of the water tank, and slowly put it into 10-20cm below the water surface, slowly pressurize until the ventilation pressure is 0.5MPa, and the continuous pressing time of each piece shall not be less than 10min. Check whether there are bubbles in all parts of the axle housing. If there are bubbles, check the bubbling position and mark them.
(5) Remove the tooling. After the completion of the pressurization, close the air source, relieve the pressure, lift the axle housing and tooling components out of the water tank, and dismantle the gas pipe and the pressing tooling.
(6) Put the leaking axle housing into the designated unqualified product area, put the qualified axle housing in the designated area for sequence change, remove and dry the water stains on the surface of the axle housing, put the pressing tooling back on the tooling placing bench, and clean the pressing site.
In the product test, the third batch of 8 products, the fourth batch of 12 pieces of air tightness test. Two batches of axle housing were produced by semi closed new casting process. During the pressing process, there was no leakage of axle housing, and the casting quality of axle housing was significantly improved. By the end of 2019, more than 6000 axle housing pieces have been produced, 174 unqualified products have been found, and the defective product rate is controlled below 3%, which has achieved good results.