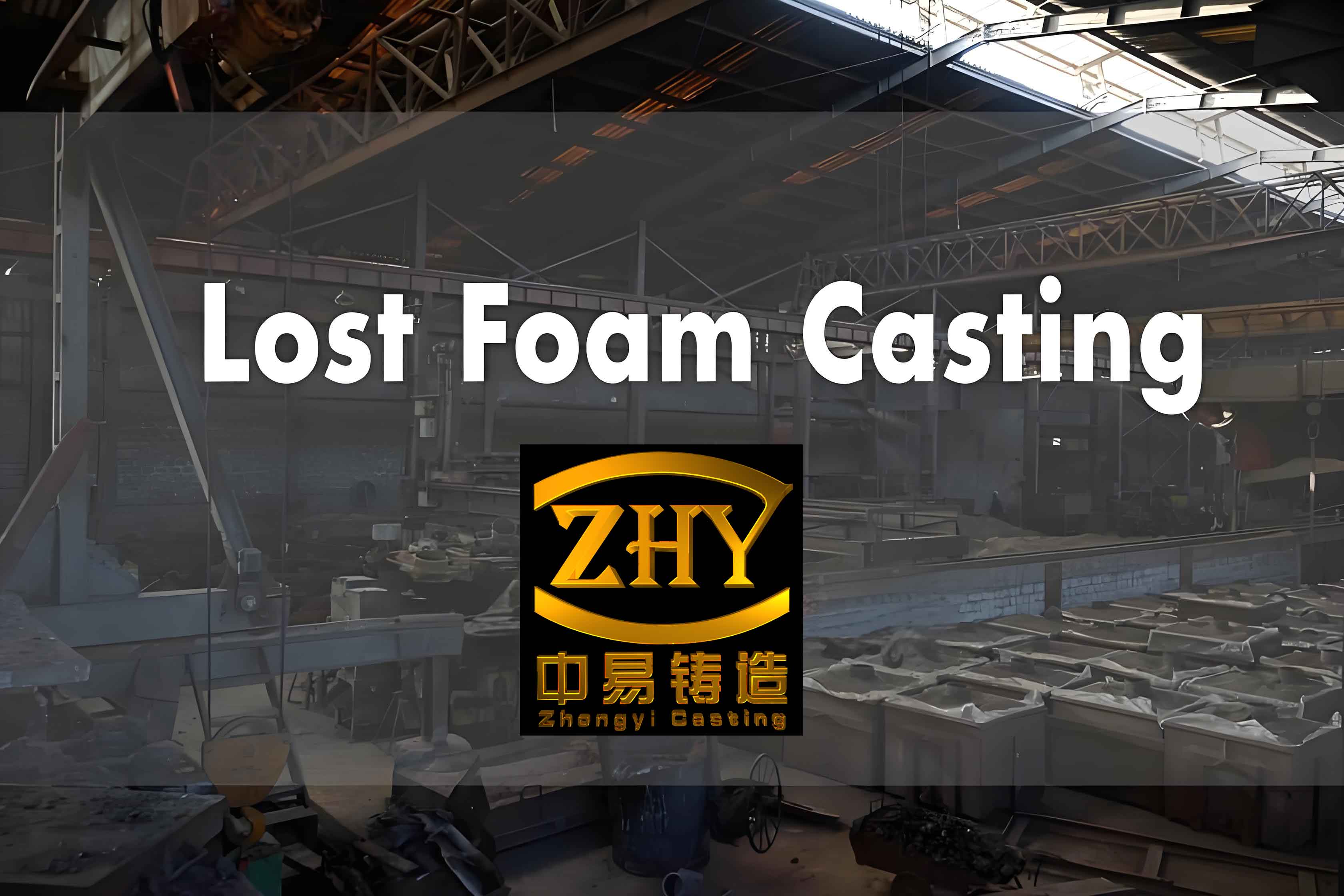
1. Introduction
Lost foam casting is a modern casting process that has gained significant popularity in the manufacturing industry. It offers several advantages such as the ability to produce complex shapes, reduced machining requirements, and improved dimensional accuracy. However, like any casting process, it is also prone to certain defects that can affect the quality of the final product. In this article, we will focus on the defects and improvements related to the lost foam casting of aluminum alloy shells for medium and light trucks AMT.
1.1 The Importance of Medium and Light Trucks AMT Aluminum Alloy Shells
The aluminum alloy shells for medium and light trucks AMT play a crucial role in the transmission system. They need to possess high strength, good heat dissipation properties, and precise dimensional accuracy to ensure the smooth operation of the vehicle’s transmission. Any defects in these shells can lead to performance issues, reduced durability, and even safety hazards.
1.2 The Challenges of Lost Foam Casting for These Shells
Lost foam casting of aluminum alloy shells for medium and light trucks AMT presents several challenges. The complex geometry of the shells, the properties of the aluminum alloy, and the requirements for high quality and reliability make it difficult to achieve defect-free castings. Some of the common challenges include porosity, cracks, and dimensional inaccuracies.
2. Defects in Lost Foam Casting of Aluminum Alloy Shells
2.1 Porosity
Porosity is one of the most common defects in lost foam casting. It can occur due to various reasons such as the decomposition of the foam pattern, gas entrapment during the pouring process, and the solubility of gases in the molten aluminum.
Causes of Porosity | Description |
---|---|
Foam Pattern Decomposition | The foam pattern used in lost foam casting decomposes during the pouring process, releasing gases. If these gases are not properly vented, they can be trapped in the casting, resulting in porosity. |
Gas Entrapment during Pouring | During the pouring of the molten aluminum, air can be entrapped in the liquid metal. This can happen due to improper pouring techniques or the presence of turbulence in the liquid metal flow. |
Solubility of Gases in Molten Aluminum | Some gases, such as hydrogen, have a high solubility in molten aluminum. When the aluminum solidifies, these gases can be released, forming pores in the casting. |
2.2 Cracks
Cracks can also occur in lost foam castings of aluminum alloy shells. These cracks can be caused by thermal stresses, shrinkage during solidification, and mechanical stresses during handling and machining.
Causes of Cracks | Description |
---|---|
Thermal Stresses | During the solidification process, the aluminum alloy undergoes a significant change in temperature. This can lead to the development of thermal stresses, which can cause cracks if the stress exceeds the strength of the material. |
Shrinkage during Solidification | As the molten aluminum solidifies, it shrinks. If the shrinkage is not properly compensated for, it can lead to the formation of cracks in the casting. |
Mechanical Stresses during Handling and Machining | The castings are subjected to mechanical stresses during handling and machining operations. If these stresses are too high, they can cause cracks in the casting. |
2.3 Dimensional Inaccuracies
Dimensional inaccuracies can occur in lost foam castings due to several factors such as the expansion and contraction of the foam pattern, the deformation of the mold during the casting process, and the inaccuracies in the machining operations.
Causes of Dimensional Inaccuracies | Description |
---|---|
Expansion and Contraction of Foam Pattern | The foam pattern used in lost foam casting can expand and contract due to changes in temperature and humidity. This can lead to dimensional inaccuracies in the casting. |
Deformation of Mold during Casting Process | The mold used in lost foam casting can deform during the casting process due to the pressure of the molten aluminum and the thermal stresses. This can also lead to dimensional inaccuracies in the casting. |
Inaccuracies in Machining Operations | The machining operations used to finish the casting can introduce inaccuracies if the cutting tools are not properly calibrated or if the machining parameters are not optimized. |
3. Analysis of Defect Causes
3.1 Influence of Foam Pattern
The quality of the foam pattern has a significant impact on the quality of the lost foam casting. A poorly made foam pattern can lead to porosity, cracks, and dimensional inaccuracies. The density, porosity, and surface finish of the foam pattern are important factors to consider.
Factors Affecting Foam Pattern Quality | Description |
---|---|
Density | The density of the foam pattern affects its strength and rigidity. A low-density foam pattern may not be able to withstand the pressure of the molten aluminum during the casting process, leading to deformation and defects. |
Porosity | The porosity of the foam pattern determines the amount of gas that will be released during the casting process. A highly porous foam pattern can lead to excessive gas entrapment and porosity in the casting. |
Surface Finish | The surface finish of the foam pattern affects the adhesion of the coating and the flow of the molten aluminum. A rough surface finish can lead to poor coating adhesion and turbulent flow of the molten aluminum, resulting in defects. |
3.2 Influence of Pouring Process
The pouring process is another critical factor in lost foam casting. The pouring temperature, pouring speed, and pouring method can all affect the quality of the casting.
Factors Affecting Pouring Process Quality | Description |
---|---|
Pouring Temperature | The pouring temperature of the molten aluminum affects its fluidity and the solubility of gases. If the pouring temperature is too high, the aluminum may become too fluid, leading to gas entrapment and porosity. If the pouring temperature is too low, the aluminum may not be able to fill the mold completely, resulting in incomplete castings. |
Pouring Speed | The pouring speed of the molten aluminum affects the turbulence in the liquid metal flow. A high pouring speed can lead to excessive turbulence, which can cause gas entrapment and porosity. A low pouring speed may result in incomplete fillings of the mold. |
Pouring Method | The pouring method used in lost foam casting can also affect the quality of the casting. Different pouring methods, such as top pouring, bottom pouring, and side pouring, have different advantages and disadvantages. The choice of pouring method depends on the geometry of the casting and the requirements for quality. |
3.3 Influence of Mold Design
The mold design is crucial for achieving high-quality lost foam castings. The mold should be designed to provide proper venting, cooling, and support for the casting.
Factors Affecting Mold Design Quality | Description |
---|---|
Venting | The mold should be designed with proper venting channels to allow the gases released during the casting process to escape. If the mold is not properly vented, the gases can be trapped in the casting, resulting in porosity. |
Cooling | The mold should be designed with proper cooling channels to control the solidification rate of the molten aluminum. If the cooling rate is too fast or too slow, it can lead to cracks and dimensional inaccuracies. |
Support | The mold should be designed to provide proper support for the casting during the solidification process. If the casting is not properly supported, it can deform due to its own weight or the pressure of the molten aluminum, resulting in dimensional inaccuracies. |
4. Improvement Measures
4.1 Optimization of Foam Pattern
To improve the quality of the lost foam casting, the foam pattern should be optimized. This can be achieved by controlling the density, porosity, and surface finish of the foam pattern.
Optimization Measures for Foam Pattern | Description |
---|---|
Density Control | The density of the foam pattern can be controlled by adjusting the formulation of the foam material or by using different manufacturing techniques. A higher density foam pattern can provide better strength and rigidity, reducing the risk of deformation and defects. |
Porosity Reduction | The porosity of the foam pattern can be reduced by using a denser foam material or by applying a coating to the foam pattern. A less porous foam pattern can reduce the amount of gas released during the casting process, decreasing the risk of porosity. |
Surface Finish Improvement | The surface finish of the foam pattern can be improved by using a smoother foam material or by applying a coating to the foam pattern. A better surface finish can improve the adhesion of the coating and the flow of the molten aluminum, reducing the risk of defects. |
4.2 Improvement of Pouring Process
The pouring process should also be improved to achieve high-quality lost foam castings. This can be done by controlling the pouring temperature, pouring speed, and pouring method.
Improvement Measures for Pouring Process | Description |
---|---|
Temperature Control | The pouring temperature of the molten aluminum should be controlled within a certain range. For aluminum alloys, a pouring temperature of around [Formula: T = 700 – 750°C] is usually recommended. This can ensure the proper fluidity of the aluminum and the solubility of gases, reducing the risk of gas entrapment and porosity. |
Speed Control | The pouring speed of the molten aluminum should be controlled to avoid excessive turbulence. A pouring speed of around [Formula: v = 1 – 3 m/s] is usually recommended. This can ensure the proper fill of the mold and the reduction of gas entrapment and porosity. |
Method Selection | The pouring method should be selected based on the geometry of the casting and the requirements for quality. For example, for complex geometries, a bottom pouring method may be more suitable as it can reduce the turbulence in the liquid metal flow and the risk of gas entrapment and porosity. |
4.3 Enhancement of Mold Design
The mold design should be enhanced to provide better venting, cooling, and support for the casting.
Enhancement Measures for Mold Design | Description |
---|---|
Venting Improvement | The mold should be designed with more and better-vented channels to allow the gases released during the casting process to escape more easily. This can reduce the risk of porosity. |
Cooling Optimization | The mold should be designed with more and better-cooled channels to control the solidification rate of the molten aluminum more effectively. This can reduce the risk of cracks and dimensional inaccuracies. |
Support Strengthening | The mold should be designed to provide more and better support for the casting during the solidification process. This can reduce the risk of deformation and dimensional inaccuracies. |
5. Experimental Verification
5.1 Experimental Setup
To verify the effectiveness of the improvement measures, an experimental setup was designed. The experimental setup included a furnace for melting the aluminum alloy, a pouring system for pouring the molten aluminum into the mold, and a mold for casting the aluminum alloy shell.
5.2 Experimental Results
The experimental results showed that the improvement measures had a significant impact on the quality of the lost foam casting. The porosity, cracks, and dimensional inaccuracies were significantly reduced, and the quality of the casting was improved.
Comparison of Casting Quality before and after Improvement | Description |
---|---|
Porosity | Before improvement, the porosity of the casting was relatively high. After improvement, the porosity was significantly reduced, indicating that the measures taken to control the foam pattern, pouring process, and mold design were effective. |
Cracks | Before improvement, cracks were present in some of the castings. After improvement, the number of cracks was significantly reduced, indicating that the measures taken to control the thermal stresses, shrinkage during solidification, and mechanical stresses during handling and machining were effective. |
Dimensional Inaccuracies | Before improvement, dimensional inaccuracies were present in some of the castings. After improvement, the dimensional inaccuracies were significantly reduced, indicating that the measures taken to control the expansion and contraction of the foam pattern, the deformation of the mold during the casting process, and the inaccuracies in the machining operations were effective. |
6. Conclusion
Lost foam casting of aluminum alloy shells for medium and light trucks AMT is a complex process that is prone to various defects. However, by analyzing the causes of these defects and implementing appropriate improvement measures, the quality of the casting can be significantly improved. The optimization of the foam pattern, improvement of the pouring process, and enhancement of the mold design are all important steps in achieving high-quality lost foam castings. The experimental verification has shown that these improvement measures are effective in reducing porosity, cracks, and dimensional inaccuracies, and improving the overall quality of the casting. In future research, further investigations can be carried out to explore more advanced techniques and methods for improving the quality of lost foam castings.