1. Casting Basic Information and Technical Requirements
Information | Details |
---|---|
Casting Outline Size | Approximately 800 mm×800 mm×200 mm |
Product Weight | 700 kg |
Product Material | HT300 |
Surface Quality Requirement | No casting defects such as porosity, sand holes, slag holes allowed after machining |
Existing Problem | Slag holes and inclusions on the upper surface of each casting, affecting appearance quality and customer installation effect |
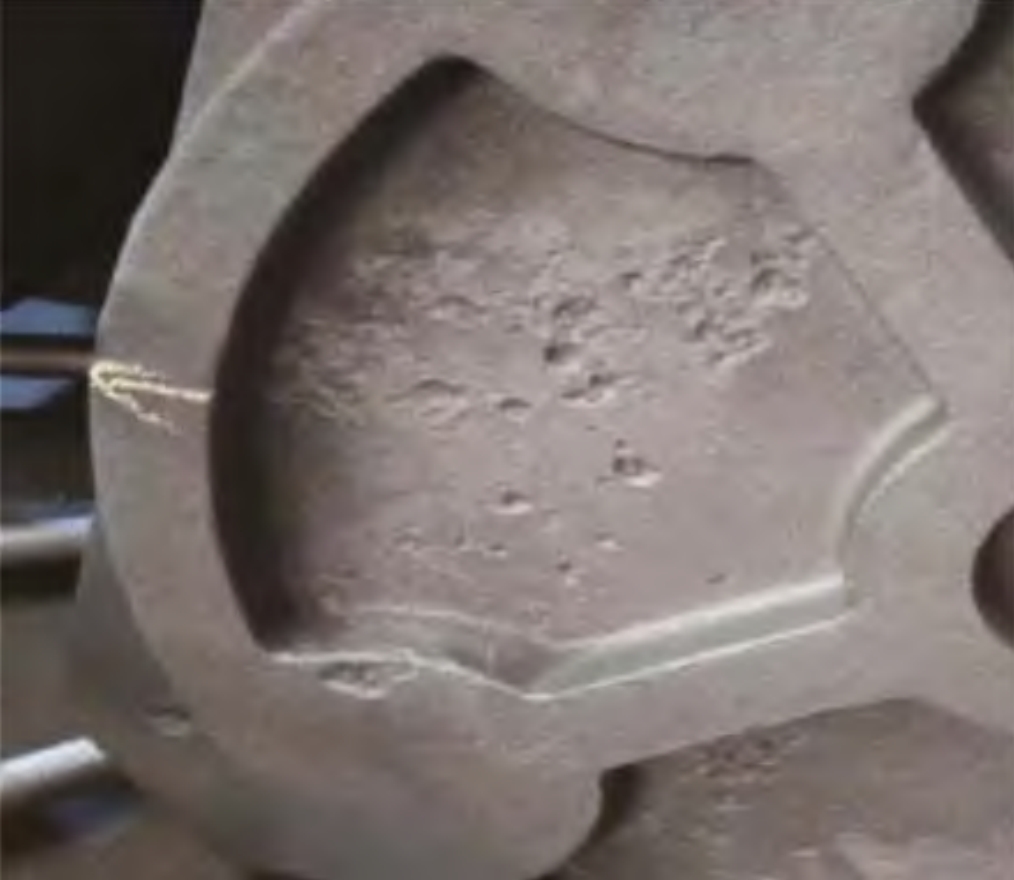
2. Casting Process Scheme Analysis
2.1 Pouring System Design
Pouring System Component | Specifications |
---|---|
Direct Pouring Channel | ϕ60 mm ceramic tube |
Cross Pouring Channel | Upper 40 mm, lower 50 mm, height 50 mm trapezoidal |
Ingate | Width 60 mm, thickness 7 mm, quantity 6 |
Section Ratio of Pouring System | ∑s内:∑s损:∑s在=1:1.8;1.2 |
Filter | Two 100 mm×100 mm×22 mm 20 PPI filters placed upright on the cross pouring channel |
2.2 Filling and Solidification Simulation Analysis
Simulation Aspect | Observation |
---|---|
Flow Field | Turbulence, air entrainment, and gas wrapping are obvious after molten iron enters the cavity, causing severe oxidation of molten iron |
Temperature Field | – |
Oxide Inclusions | Oxide film leads to the risk of secondary oxidation slag inclusion, and slag defects appear on the side wall and upper plane |
Particle Tracking | – |
3. Process Optimization and Improvement Results
3.1 Pouring System Optimization
Optimization Item | Before Optimization | After Optimization |
---|---|---|
Pouring System Type | Semi-closed | Open |
Ingate Size | 60 mm×7 mm | 100 mm×10 mm |
Section Ratio of Pouring System | ∑s内:∑s损:∑s在=1:1.8;1.2 | ∑s内:∑s损:∑s在=1:0.75;0.47 |
Molten Iron Filling Status | Turbulent, with slag and gas problems | Stable, with reduced secondary slag |
3.2 Reduction of Oxides and Sulfides
Improvement Measure | Details |
---|---|
Selection of Curing Agent | Use a low acidity curing agent with an addition amount of about 45% to reduce sulfur content in recycled sand |
Adjustment of Inoculant | Change from silicon-calcium-barium inoculant to ferrosilicon inoculant |
Selection of Coating | Use antioxidant, anti-seepage sulfur shielding coating to prevent sulfur infiltration and reduce iron oxidation |
3.3 Effect Verification
Verification Result | Description |
---|---|
Casting Defect Status | Slag hole defects are significantly reduced, the surface is clean, and no large slag holes appear |
Production Verification | Multiple small-batch production verifications have been carried out in similar products, with a significant reduction in slag hole defects and a greatly reduced rejection rate |
4. Conclusions
- The design of the pouring system is crucial. For different types of products, a suitable pouring system can effectively prevent slag and ensure stable molten iron flow during filling, reducing casting defects.
- Numerical simulation technology is used to analyze the feasibility of the casting process. By referring to the simulation results, the process rationality is evaluated and optimized to minimize potential problems and casting defects in production, thereby improving product quality.
- The selection of coatings is also important for different product structures and production processes. Appropriate coatings can help reduce casting defects, improve product quality, and lower the rejection rate.