1 Causes and prevention of sand defects
As defined in GB5611-2017 Casting Terminology, sand removal is a meaty defect. Fleshy defects are “various on the surface of the casting.”The general term for multi-meat defects”, and the definition of sand defects is “sand mold.”The local sand block of the (core) falls under the action of mechanical force, making the casting Lumpy metal protrusions formed at the corresponding part of the surface. Its shape is the same as The sand lumps that fall are similar, but there are often sand holes or mutilations in other parts of the casting.”
1.1 Defect Characteristics
The sand defects are mainly concentrated in the attachment parts of the four small holes in the square top plane of the upper box. Figure 1 shows a casting with a sand drop defect.
1.2 Cause Analysis
Generally speaking, during the closing operation, the cavity of the upper box falls and the core head in the cavity of the lower box is damaged, resulting in the core breakage, such as If the box is not inspected at this time, the large and small sand blocks are left in the cavity. After pouring, sand defects are formed in the casting. It may cause core bumps The reasons for the bad are:
1) When closing the box, the parting surface of the upper and lower boxes is not parallel;
2) The relative position of the upper and lower boxes is not good or not aligned when closing the box (the height of the top surface of the positioning sand cone is lower than the top surface of the core head by 150mm, Unable to locate the core head, the core holder);
3) When the box is closed, the car slides;
4) The gap and slope of the core head of the process design are not suitable;
5) There is a problem with the size of the model;
6) When the core is lowered, the position of the four small round core heads is not accurate, etc. Due to the rubber injection machine 250t cylinder product prototype production The first 5 pieces were all qualified products, and none of the 15 pieces in the previous production were not
There is a problem of sand dropping in the piece, so the process and mold can be excluded
in question; If the driving is unstable, this problem will not occur one after another; So basically, it can be judged that it is due to the loading and unloading of the box when the box is closed
The parting surfaces are not parallel or the relative positions of the upper and lower boxes are not aligned
It is a matter of responsibility and operation methods that belong to Operational defects.
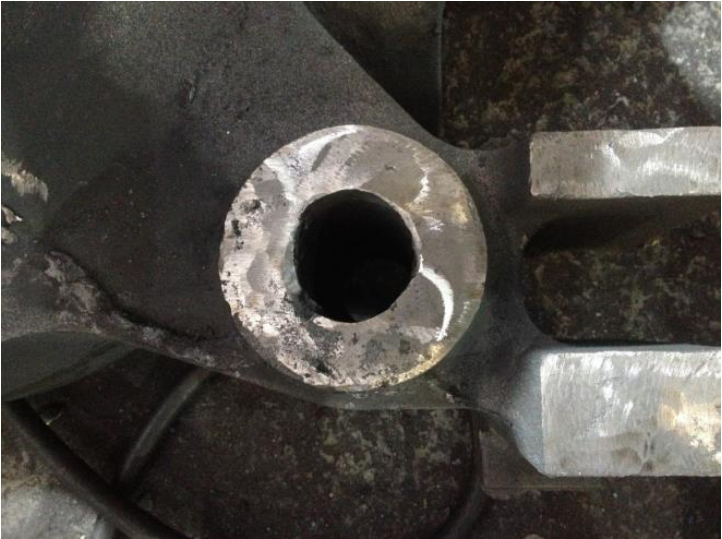
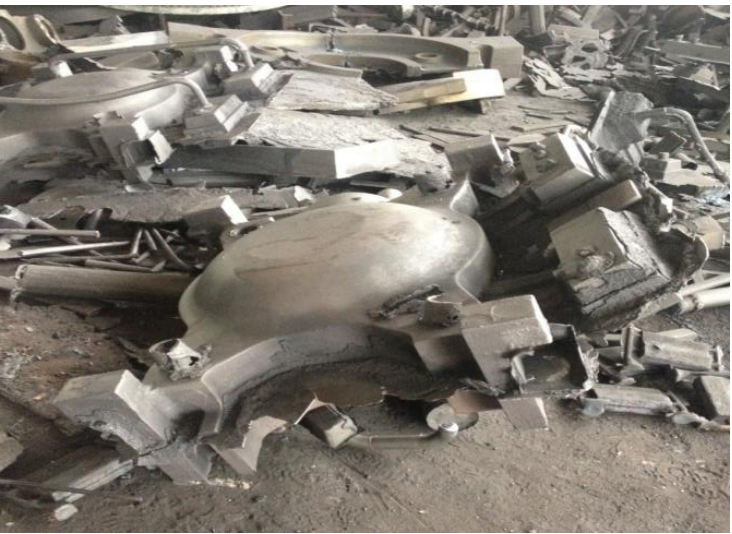
Figure 1 A casting with a sand drop defect
1.3 Resolutions
1) Improve the sense of responsibility and carefulness when closing the box to ensure that the core does not collide;
2) Before closing the box, the lower box should be placed horizontally, and the upper box should be adjusted by adjusting the tightness of the spreader to ensure the level and carefully check to ensure that the upper and lower boxes are ensured parallelism of the box parting surface;
3) When closing the box, it should be operated by multiple people to ensure that the relative position of the upper and lower boxes should be aligned.
4) If necessary, check the box (empty box) or use the pallet to verify the position accuracy of the four small round core heads.
5) It can be considered to adopt a resin sand box positioning guide pin sleeve to guide and position the box.
2 Causes and prevention of fire defects
The fire problem of this piece is also more prominent, which leads to the scrapping of castings in serious cases, accounting for 30% of the scrap; In addition, there were several times when there were fires that did not cause scrap.According to the definition of GB5611-2017 Casting Terminology, fire running is a defective defect. Defects in the category are “castings due to a variety of defects.”The general term for the shape defect caused by the cause”, and the definition of the fire defect is “the serious depression and mutilation of the part above the parting surface of the casting caused by the flow of molten metal from the parting surface during the pouring process”. Sometimes foil-like fragments are left along the surface of the unfilled cavity”.
2.1 Characteristics of the phenomenon
At the end of pouring, when the molten iron is close to being poured, the cavity is pressed After the force increases and the “bang” sound is made, a large amount of molten iron appears along the parting surface Spillover situation. Scrapped castings can be seen to be incomplete or missing It also poses a potential safety hazard to pouring personnel.

Figure 2 The pouring process runs off fire
2.2 Cause Analysis
In general, the possible causes of running fire (running fire) are:
1) The sand sealing of the parting surface is not strict before sand mold pouring, and the sand sealing strength is low;
2) The parting surface of the upper and lower boxes is uneven, deformed, warped, and the fitting is not strict, and there is a gap or a large area of flash;
3) The clamping force of the sand box is not enough or the clamping is improper (the strength and quantity of the clamping screws are not enough, and the position is incorrect), which causes the box to run after lifting Fire;
4) The pressing iron is too light, resulting in lifting the box;
5) The pouring speed is too fast in the later stage, etc.
More than two-thirds of the height of the 250t cylinder product casting of rubber injection machine is on the upper box. When pouring when the molten iron exceeds the parting surface,Due to various reasons (the static pressure of the molten iron increases, the mud seal parting surface is not strict), if there are weak links in the parting surface, there is a leakage, and the molten iron bursts out of the type, and the phenomenon of fire running (fire running) occurs. From the analysis of the existing problems, the uneven parting surface of the upper and lower boxes, the lack of strict fitting, and the existence of gaps may be the main reasons for the fire of lifting the box. This problem seems to be related to the above-mentioned inaccurate positioning of the closing box, and has a similar nature.
2.3 Resolutions
1) Improve the sense of responsibility and seriousness when sealing and tightening boxes;
2) In addition to avoiding the above-mentioned “possible causes of fire-running”, it is necessary to ensure that the cores do not collide when closing the box, so as to avoid causing the upper and lower boxes to be stuck and leave gaps.
3 Concluding remarks
The defects of sand falling and fire running of the 250t cylinder of the rubber injection machine were analyzed, and targeted preventive measures were put forward to prevent it The recurrence of two types of casting defects. In the process of casting production, it is inevitable that defects will occur in castings, and it is casting to carefully analyze the causes and propose preventive measures It is the duty of the worker to shirk it.