The cylinder head of a certain type of diesel engine produced by ZHY Casting factory has complex structure, compact layout, poor casting process and many hole casting defects in production. This paper analyzes the shrinkage defects of the cylinder head of a diesel engine, and puts forward solutions.
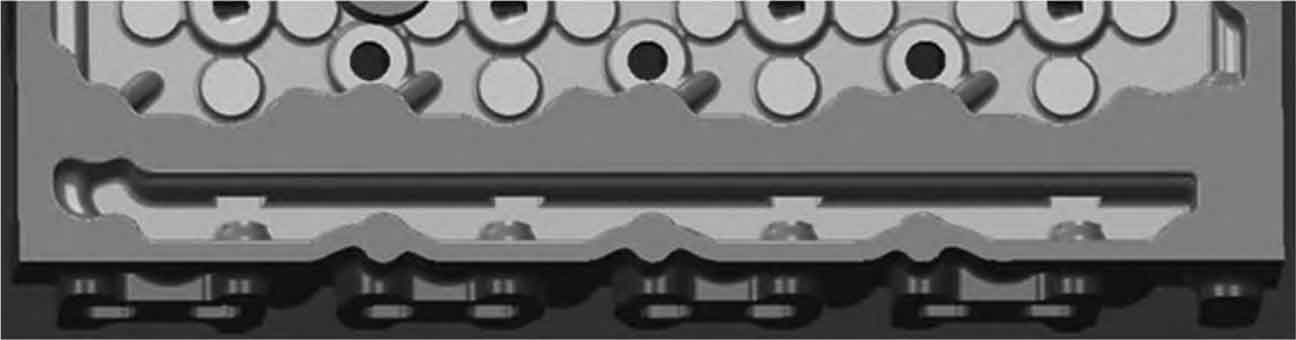
The cylinder head structure of a certain diesel engine is a four cylinder integrated cylinder head (as shown in Fig. 1). The material is HT250, the blank weight is 28KG, and the single sand core weight is 45kg. The sand core includes six kinds of sand cores: chassis core, upper cover core, water interlayer core, air inlet core and exhaust core. The first two kinds of sand cores are cold core box cores, and the last four kinds of sand cores are hot core box coated sand cores. The molding is the wet sand molding process, four pieces in one box, and the vertical casting bottom casting process.
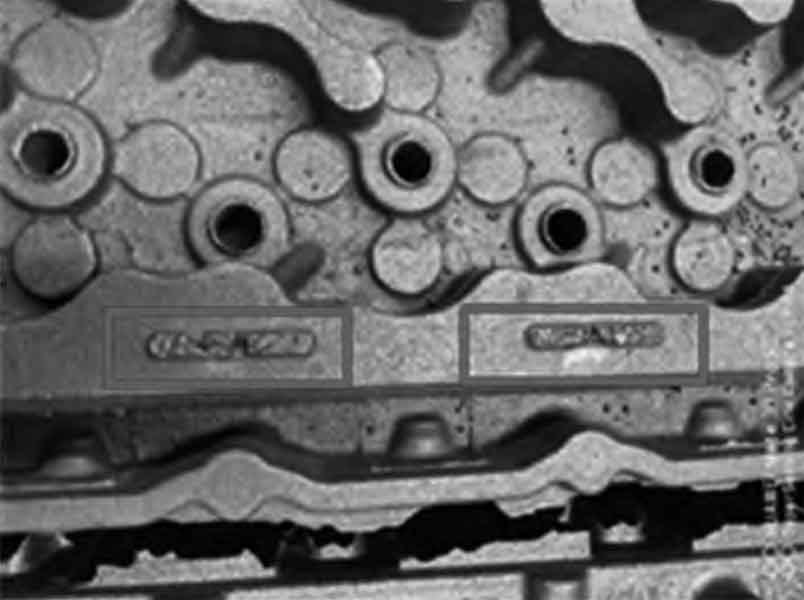
At present, the main casting defects of cylinder head are the holes at the inner gate position on the upper surface of the casting (as shown in Fig. 2), accounting for 70%. After dissection, the depth of the casting defects inside the casting varies from 3 to 10mm, and extends inward, resulting in great hidden dangers in the performance of the casting product.
(1) In the pouring process design of the compact gray iron cylinder head, the layout of the ingate should not only consider the temperature gradient in the pouring process, but also avoid the thick parts that produce hot spots to reduce the occurrence of shrinkage casting defects.
(2) The change of casting process should not only focus on the improvement of single casting defect, but also consider the fluctuation of comprehensive scrap rate to solve the casting defect problem as a whole.
(3) In the process tooling design stage of the product, it is necessary to consider the hot spot problem of thick and large parts in advance, reasonably arrange the pouring system, and reduce the production cost and time cost caused by subsequent process change and verification.