(1) The defects of the anchor support and the outlet flange are close to the processing surface, and the processing surface is a regular plane. By setting the side riser for feeding, the defect problem can be effectively solved, so I will not repeat it here.
(2) The inlet flange is located at the top, which can apply riser to supplement shrinkage molten steel, and also has no worries about quality.
(3) There is no defect in the seal ring area except for the connection near the outlet. Through the analysis of the structure, it is preliminarily judged that the modulus of the connection part can be controlled to make the modulus of the area close to the modulus of the main wall thickness, so as to achieve the modulus balance state and realize self feeding.
(4) For the connecting flange, the connecting part brings certain benefits. The defects are concentrated here, which is conducive to feeding. A side riser is set at this position to ensure that the riser has enough pressure head to achieve feeding.
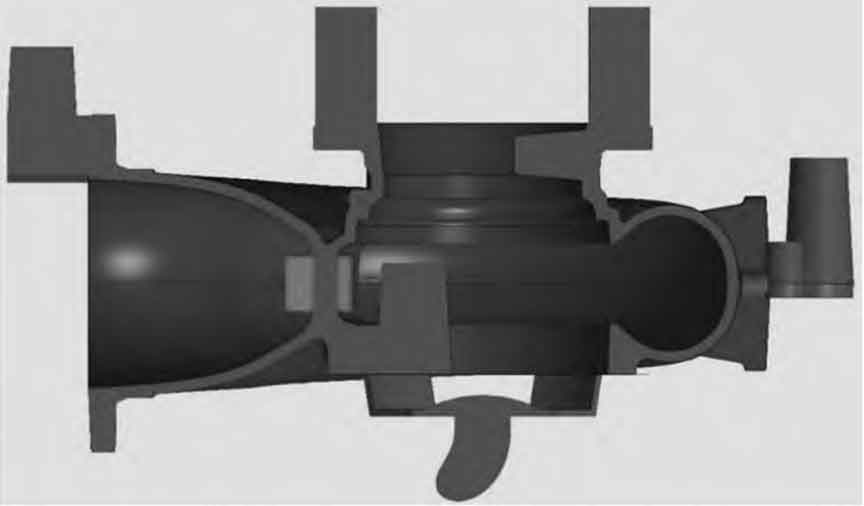
The final scheme is shown in Fig. 1. The foundation support and outlet flange are provided with side risers respectively; Two feeding risers are set at the top of the inlet flange; The connecting flange is provided with a side riser; Chrome iron ore balance modulus is used on both sides of the connection part.
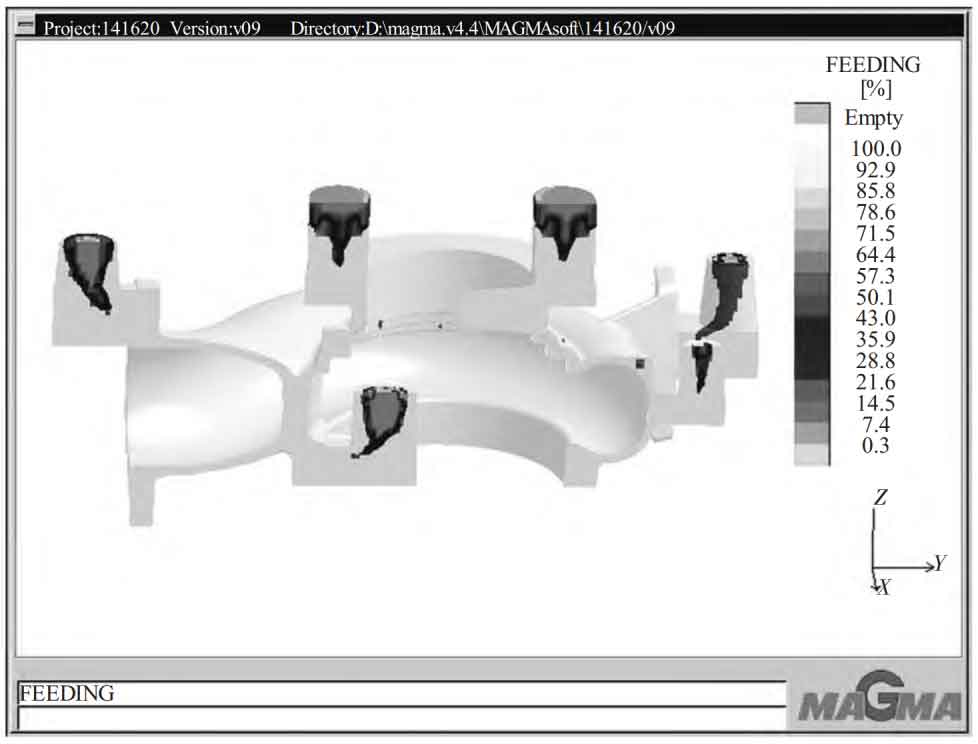
The simulation results of the final scheme are shown in Figure 2. It can be seen that there is no defect prediction in the key area, and the scheme is qualified for verification.