The failed crankshaft is a ductile iron crankshaft!The material is hKM””&!Strengthening process for fillet groove rolling E axis radial medium frequency induction quenching + solidUse a stereoscope (scanning electron microscope “GR ‘# (metallographic microscope) to perform the inspectionDon’t analyze the fracture morphology of the failed crankshaft!The micro-area composition is analyzed using an energy spectrometer “R=G#” to perform energy spectrum analysis on the fracture area.Take samples for metallographic analysis to determine the environment (bearing) in the working process of the nodular cast iron crankshaftThe load!Combined with the characteristics of the crankshaft material!Comprehensive analysis of the crankshaftThe failure mechanism of the shaft!So as to find out the real reason for the early fracture.
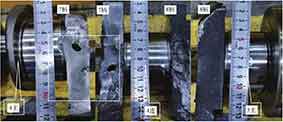
macro analysis
The fracture morphology of the failed workpiece shows that the workpiece withstands load (selfThe failure mechanism and process of materials (the comprehensive effect of operating environment! usually the working environment)All failures start from surface or near-surface damage, leaving uniqueThere are some features and traces!These features and traces include the fracture surfaceVisual appearance (metallographic structure (change in color and other states + fracture characteristic analysisIt is to search for the failure mechanism based on these characteristics and traces on the fracture surface of the failed workpiece.Origin of failure fracture (direction of fracture propagation (force at failureFeatures, etc. nodular cast iron Confirm whether there are macro defects in the crack source area, and then judgeMain crack (crack source or failure nature, etc.
The strengthening process for the broken crankshaft fillet is grooving and rolling + nodular cast iron rollingStrengthening!The tensile stress on the rounded surface becomes compressive stress + tensile stressThe main factor of fatigue failure of the crankshaft journal fillet!And the residual stress on the fillet surfaceThe residual pressure stress can effectively offset some of the tensile stress and reduce the deformation of the crankshaft during operation.The peak stress!This greatly improves the fatigue strength of the crankshaft fillet.The fillet is not the fatigue source location of rolling strengthening!Generally, it is the stress concentrationThe center of the fillet!After the fillet is rolled and strengthened, due to residual compressive stressThe pressure relief and peak shift effect!The fatigue source is generally transferred to the rollingAt the edges of both sides of the groove.From the figure, it can be seen that the crack source is also located at the position of the flaw.At the intersection of the lower end of the crank and the lower end of the connecting rod rolling groove edgeThe near surface of the first crankshaft + the crack propagation direction is aligned with the axial direction of the crankshaft.The present angle is close to the last groove edge of the main journal fillet near the $Instantaneous fracture occurs along the location.
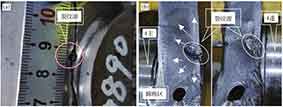
For ductile iron crankshafts, the failure location is oftenThe reason for the occurrence of the lower limit of the connecting rod journal and the transition fillet of the crankshaft is alsoIncluding!The area near the transition fillet of the lower stop point of the connecting rod journal belongs to the hot spot area!There are more shrinkage cavities (porosity (casting defects such as slag inclusion) are likely to exist.nodular cast iron 。
Observe the fracture of the first crank in Figure 1!The fracture area is crackedThe distribution characteristics of the source region (expansion region (instantaneous break region) are obvious. nodular cast iron In order to betterObserve the fracture morphology of the 7th crankshaft, which is included in the white box in Figure 1Zoom in the area, and the magnified topography is shown in Figure 2。
It can be clearly seen that the crack source area is “inside the white circleThe near-surface crack source of the first crank arm located on the side of the first connecting rod is a holeThe shape of the hole is oval, with a large inside and a small outside, with a size of aboutThe hole is large in volume, macroscopically obvious, and easily identifiable. The edges around the hole are distinct, showing a radial pattern structure that expands outward.There is no significant plastic deformation in the area near the main axisThe middle part of the handle edge is the expansion area!The expansion area has obvious fatigueThe fatigue crack propagates from the hole in the crack source area to the two ends of the crank arm.Expanding from the side and one side of the main journal, and finally on the side of the main journalThe occurrence of instantaneous fracture”nodular cast iron refers to the direction of fracture propagation indicated by the instantaneous fracture zone in the figureThe direction is indicated by the white arrow in the figure。
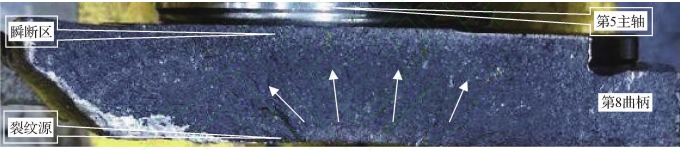
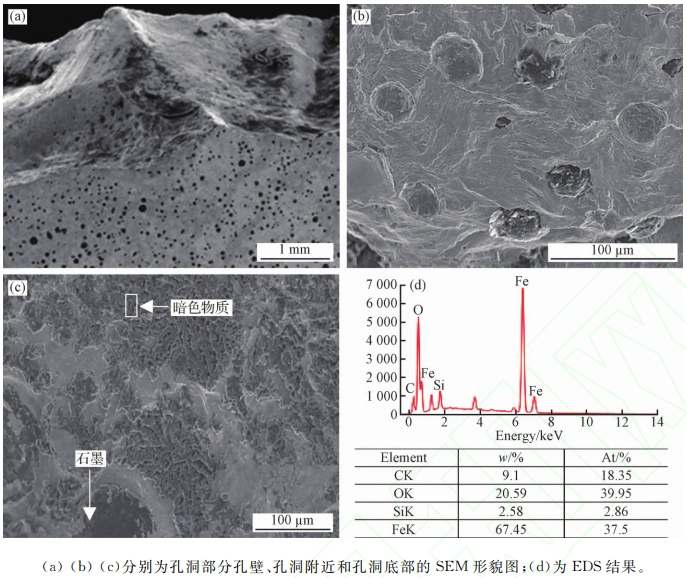
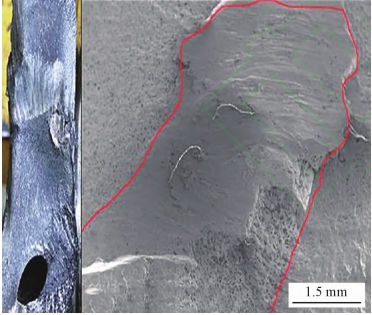
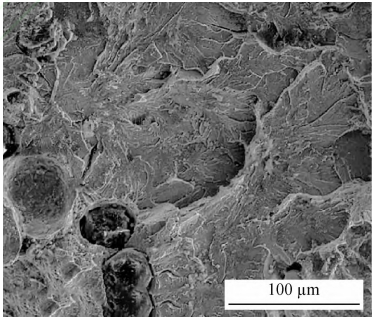
According to the national standard, ductile ironMetallographic examination of the cross-section of the crankshaft hole areaTest it!As shown in Figure 6, the graphite around the holeThe quantity is relatively large (the distribution is relatively even (the graphite roundness is good! Graphite ballThe chemical level is!level!The diameter of the graphite ball is <level+nitric acidObserve the corrosion of the sample with ethanol solution!nodular cast iron Find the tissue near the holeConsists of flake pearlite E, a small amount of ferrite E, and graphite!Pearlite containsIn addition, a layer of dark material was also observed at the bottom of the hole.Quality!

Based on all the previous analysis, the causes of the fracture of the crankshaft are as followsInvasive gas porosity process sand mold (water (organic matter) in sand coreWater vapor formed by combustion (carbon monoxide (carbon dioxide and other gases invasionEnter the crankshaft casting part: roll the groove edge of the lower stop point of the first crank and the first connecting rodThe surface of the casting at the handover position!Forming oval-shaped intrusive pores +”The intrusive pores have damaged the connection strength of the crankshaft matrix metal!Deteriorate the mechanical properties of defects!Reduce fatigue strength +When the mine vehicle is working at full load,nodular cast iron the crankshaft journal isExcessive bending and twisting stress near the corner!Stress exceeds the intrusive air holeThe fatigue limit at the defect causes the rapid formation and expansion of fatigue cracks.The first crank broke instantaneouslyAfter the fatigue fracture of the crankshaft, the crankshaft continues to rotate due to inertiaThis in turn caused the 6th crank to overload in a short period of time!The handle also instantly failed and broke!At the same time, the rear end of the cylinder body cracked!The lever is bent!The camshaft of cylinder No.nodular cast iron is also broken.