The low pressure casting process has been in existence for more than 100 years.The concept of history was first proposed by the British scientist E.F.LAKE, butAt the beginning, this casting process did not form large-scale industrial application.Until 1945, the British Arumask Company used low-pressureLarge-scale, industrialized production of rainwater pipes and beer containers through casting technologyAfter 1950, due to the rapid development of the automotive industry, the United StatesThe country applies low pressure casting technology to the production of automotive engine components.Manufacturing has made the low pressure casting process and related equipment have a qualitativeIn 1957, China formally introduced low pressure casting equipment.Prepare and conduct research on related casting processes.
1 Basic principle of low pressure casting
Low pressure casting is a casting process method that enables the molten metal to fill the mold cavity under a certain pressure, forming a casting. Due toThe pressure used is relatively low (0.02 MPa~0.0.6 MPa), so theIt is often called low pressure casting.The basic process of the technology is:Dry compressed air or inert gas is introduced into the crucible (or sealed tank)The metal liquid is stabilized along the riser tube under the action of gas pressure.rise and enter the cavity through the inner gate, keeping the crucible (or sealingThe gas pressure on the liquid surface in the tank until the casting is completely solidified.Then, release the gas pressure on the metal surface, so that the uncondensed gas in the riser tubeThe solid metal liquid flows back into the crucible, and finally the casting can be pushed out.LowThe schematic diagram of die casting is shown in Figure 1.
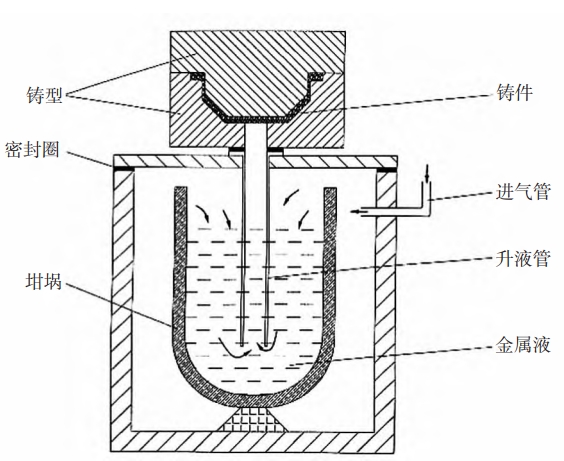
2 Low pressure casting process parameters
1) Lifting pressureThe pressure required to raise the metal surface near the gate is calledis the liquid pressure.The liquid pressure reflects the pressure of the molten metal in the liquid-raising tube.The rising speed of the metal liquid in the rising tube should be as fast as possibleSlowly, so as to facilitate the discharge of gas in the cavity, and also to prevent the splashing of molten metal when it enters the gate.2) Molding pressureIt refers to the process of causing the molten metal to rise to the top of the mold during the filling process.The required gas pressure.3) Filling speedThe rising speed of the metal liquid surface during filling is the fillingSpeed.To prevent the occurrence of cold shut and under-cast defects, the filling speed should beAbove the minimum value, while the speed should not be too fast to avoid turbulence.The generation of oxidation inclusions is caused by liquid-gas rolling.4) Crystallization pressureContinue to pressurize after the molten metal fills the mold cavity to crystallize the castingSolidification occurs under a certain pressure, which is calledThe higher the crystallization pressure, the better the feeding effect of the casting, and finallyThe obtained casting structure is also more dense, and the mechanical properties are also better.However,Over-crystallization increases pressure to improve casting quality, not in all cases.can be used.The typical value range of crystallization pressure is (0.1 MPa~0.25 MPa).5) Holding timeAfter the pressure of the molten metal increases to the crystallization pressure, it willHold for a period of time until the casting is completely solidified, and maintain the pressure required for solidificationThe required time is called the holding time.If the holding time is not enough, the casting will notWhen fully solidified, the pressure will be released, and the metal liquid in the cavity will be completely or partiallyFlow back to the crucible, causing the casting to “empty” and be scrapped: if the holding pressure time is too longFor a long time, the gate residue will be too long, which not only reduces the process yield, but alsoIt can also cause the metal liquid in the gate and the riser to “freeze”, resulting in the casting beingTherefore, suitable packing time must be selected during production.
6) Mould temperatureLow pressure casting can use various molds, and the work of non-metal moldsThe temperature is generally room temperature.However, the working temperature of the metal mold isAccording to the requirements of low pressure casting of aluminum alloy, the working temperature of the metal moldThe temperature is generally controlled at 200°C to 250°C, and when pouring thin-walled complex parts, it can even be as high as 300°C to 350°C.7) Pouring temperaturePractice has proved that under the premise of ensuring the formation of castings, the pouring temperatureThe lower the degree, the better. The pouring temperature of low pressure casting is generally lower than that of gravity casting.10℃~20℃.
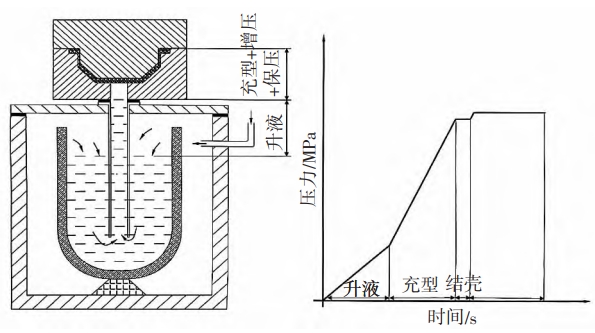
3 Features of low pressure casting process
3.1 Advantages of low pressure casting process1) Due to the fact that slag generally floats on the surface of the molten metal, low pressure castingThe process is to fill the metal liquid at the bottom of the crucible through the liquid lifting tubeTherefore, it can effectively avoid the possibility of slag entering the mold cavity,The purity of the liquid is high, and the casting has fewer inclusions and defects. The pressure is uniform.Therefore, the filling of the molten metal is relatively stable, which can effectively reduce or avoidTurbulence and splashes of molten metal during filling process, reducing double-layer oxygen in castingsThe possibility of defects such as film formation and oxidation slagging.3) The molten metal fills the mold under pressure, which canImprove the fluidity of the molten metal, which is beneficial to the formation of surface smoothnessGood and well-defined castings, especially for complex thin-walled castingsThe shape is more favorable.4) Castings are crystallized and solidified under certain pressure, and canRealize top-down sequential solidification (as shown in Figure 3), with good feeding effect.The casting structure is relatively dense, with fewer shrinkage defects such as porosity and shrinkage cavity.5) Low pressure casting generally does not require risers and risesThe uncrystallized and solidified metal liquid in the tube can be refluxed to the crucible to achieveTherefore, the recovery rate of metal liquid is high, generally up toOver 90%.
3.2 Disadvantages of low pressure casting process1) The equipment cost of low pressure casting is relatively high, and the initial investment is large.The production efficiency is low, and it is generally used for casting non-ferrous alloys.2) During the production of aluminum alloy castings, the crucible and liquid lifting tube are exposed to high temperature for a long time.Metal liquid contact, easily eroded and scrapped, will also increase the iron content of the metal liquidleading to deterioration of the casting properties.
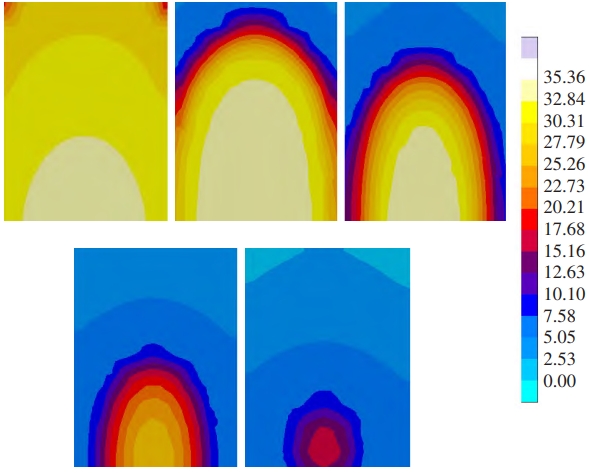
4 Analysis and Countermeasures of Common Defects in Low-pressure Casting
Common defects in low pressure casting include: porosity, shrinkage porosity,Cold shut, inclusion and other defects.
4.1 Air hole
The morphology of the stomata is mostly round or oval, with smooth inner walls.It is slippery and often has a slight oxidation color.Causes: 1) The filling speed of the molten metal is too fast, causing the flow to be disorderedInvolvement of gas and failure to discharge the gas smoothly in time, resulting in the lack of gas holes2) After the filling of the metal liquid is completed, due to the long sand mold and sand core,The time is heated to generate gas, causing the gas to invade the partially solidified metalIn the liquid, which leads to the generation of porosity defects;3) The type of poor exhaust,There is a pocket gas area in the cavity, which leads to the occurrence of porosity defects.Preventive measures: 1) Selecting a suitable filling speed, ensuring that theUnder the premise of generating cold shut-off and insufficient pouring, it is necessary to ensure that the molten metal is filled as much as possible.The smoothness of the mould during casting to avoid the generation of air entrapment;2) optimizing the sand mold and sandThe exhaust conditions of the core should be controlled to prevent gases generated by the sand mold and sand core from entering the gold.It is a liquid.In addition, under the premise of ensuring the strength of sand mold and sand core, reduceThe resin content of sand mold and sand core should be reduced to reduce gas emission;3) Avoid exhaustThe vent structure such as the hole and vent plug is blocked.
4.2 Shrinkage and porosity
The morphology characteristics of shrinkage porosity are mostly irregular holes and pores.The inner wall of the tunnel is relatively rough, with many dendritic protrusions, which are mostly generated at the center of the hot spot or at the last solidified part .Cause: After the filling of the molten metal, the solidification of the crystallizationDuring the process, a top-down temperature gradient cannot be formed, and theThe sequence of solidification is not good, and the hot spot that solidifies last cannot be wellThe shrinkage of the material leads to the formation of shrinkage defects.Preventive measures: 1) Strengthen the heat dissipation capacity of the hot spot (such as cloth2) Try to reduce the pouring as much as possible without causing cold shutTemperature;3) increase the holding pressure during crystallization and solidification to enhance the metal liquidThe fluidity of the mold is improved, and the ability to supplement shrinkage holes is enhanced.
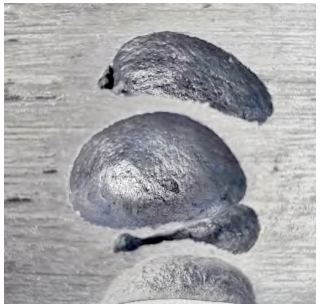
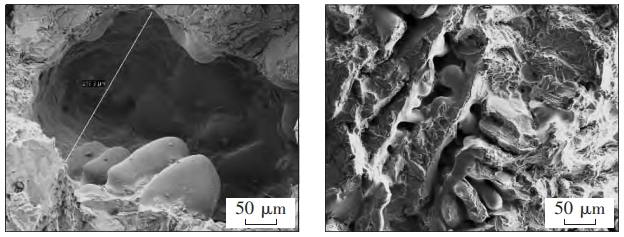
4.3 Cold Shut-off
The morphological characteristics of cold shuts are the existence of cold shut patterns, that is, two convection currentsThe front end of the molten metal failed to be welded well.Causes: 1) Too low pouring temperature or cooling capacity of the moldThe force is strong, and it is easy to cause cold shut defects in the area where the metal liquid flows;2) Insufficient filling pressure and poor fluidity of the molten metal can also lead to cold shut-off.The emergence of traps.Prevention measures: 1) appropriately increase the pouring temperature of the metal liquid;2) For the cold shut-off caused by the too fast cooling rate of the chilled iron rod, the coldModerate heating treatment of iron rod;3) appropriately increasing the filling of the metal liquidPressure, improve the fluidity of the metal liquid.
4.4 Inclusion
The morphology of the inclusion defects is irregular in shape, and the color of the defectsand there are significant differences between the casting body and the casting body.Causes: 1) For the formation of non-metallic inclusions, multiple sourcesForeign matters falling into the cavity during the research box process have not been cleaned up, resulting inDuring the filling process, it enters the molten metal to form inclusions;2) oxidationThe inclusion is mainly caused by the fast filling speed of the metal liquid, the disorderly splashing of the liquid surface, and the formation ofThe formation of a double-layer oxide film leads to the occurrence of inclusions.Prevention measures: 1) During the grinding process, the processing cavity should be cleaned thoroughly;2) Adjust the filling pressure to avoid excessive filling speed causing turbulence in the molten metalAdd a filter screen at the liquid outlet to prevent metal splashes or increase the filtering effect.The filtering and stabilizing effect.
5 Conclusion
The quality of low pressure casting castings is good, and the process yield rate is high.The application scope is constantly developing, and it is urgent to improve the level of low pressure casting process and technology to avoid the occurrence of defects in low pressure casting.In the field of computer numerical simulation technology, accurate numerical values have been developedSimulate the filling flow, solidification and crystallization sequence of the molten metal liquid, and compare it with the actual filling,A model with consistent solidification phase is particularly important.Through improving the performance of castings,In-situ detection capability (such as detecting residual stress in castings through ultrasonic equipmentThe situation can also be predicted through thermal analysis technology for key parts of the casting.mechanical properties), which not only avoids destructive testing on the casting,The detection can also reflect the accurate casting situation in time, realizingPrecise control of the casting process and casting properties.