1. Filling Process Analysis
The filling process simulation analysis of Figure 5 shows that the filling time of the casting is 4.01 s.When the filling time reaches 1.0 s, the metal liquid fills the two bottom parting cavities of the casting. It can be seen from the color band that the metal liquid phase is relatively stable at this stage, and there are no splashes or coils of metal liquid during filling process. When the filling time reaches 2.01 s, the metal liquid fills the upper part of the casting and fills to 3.02.At s, the liquid metal has filled most of the cavity of the castings, and most of the contours of the castings except the top plate appear; at filling time of 4.01 s, the liquid metal is filled to the highest part of the castings and the filling is completed, so the overall filling effect of the castings is good.
2. Analysis of solidification sequence
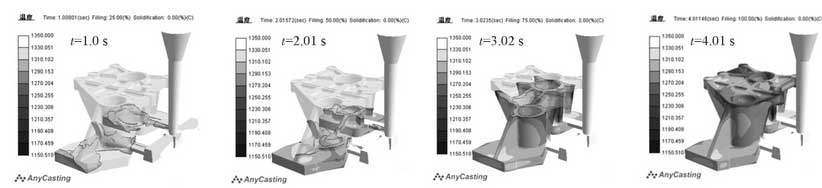
Looking at the solidification sequence of the castings in Figure 6, it can be seen that the outer contour and the inner gate of the castings in Figure 1A are first cooled and solidified. Analyzing Figure 1a and Figure 1b, it can be seen that the solidification of the castings is cooled from the outside to the inside because the outer wall thickness and structure of the castings are single and the cooling rate is faster. Some hot-spot parts of the castings in Figure 1C are not cooled, and these hot-spot locate 1D at the bottom of the inner side of theWhen the whole temperature reaches below the solid line temperature of nodular cast iron, the casting is cooled down and shows a completely solid state.
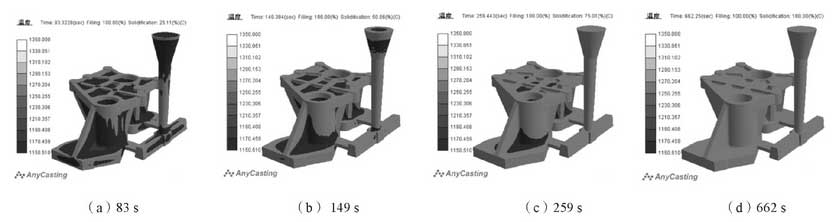
Considering that it is difficult to accurately determine the position or size of casting defects only by analyzing the solidification sequence of castings, it is necessary to analyze the probabilistic casting defect parameters (residual melt modulus).As shown in Figure 2, due to the lag of liquid metal solidification, there are many defects in the casting, and the distribution of defects is relatively dispersed. Potential defects in the casting account for 0.18% of its volume.
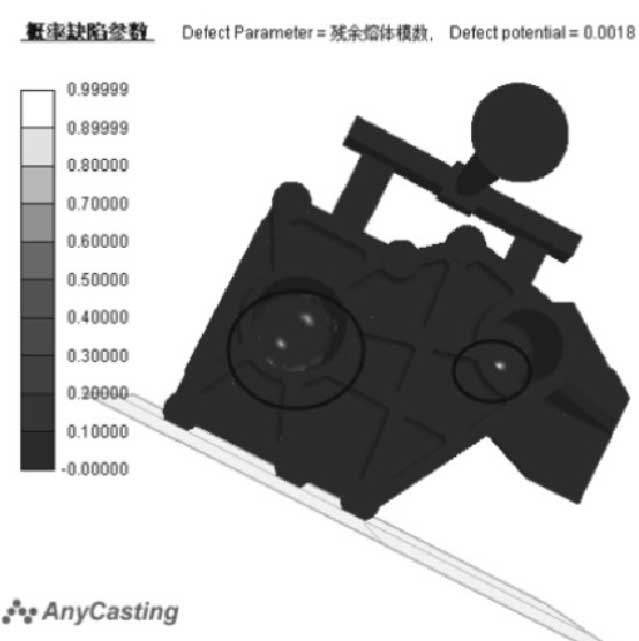