1. Design of compensation system and air outlet
Based on the analysis results, the top area of the casting finally solidifies, so it is necessary to set a riser to compensate it.Risers are arranged in a ring around two cylindrical cavities at the top of the castings with 9 risers and their heights are 14.4 mm.During pouring, the cavity is closed, which is not conducive to metal liquid entering the cavity, and a series of mixed gases will be produced during pouring. Therefore, it is necessary to set an outlet to exhaust the gas.The air outlet is set on the top side of the casting so that the liquid metal can enter the cavity smoothly and the generated gas can also be discharged through the air outlet.
2. Setting of Cold Iron
According to the simulation results, the annular part at the bottom of the casting is thicker, the liquid metal cools slowly, resulting in solidification lag, thus forming hot spot. Therefore, it is necessary to set chill here to control the solidification sequence of the casting.Engineer ZHY Casting has set up 8 pieces of cold iron, which are arranged in the centralized position of the hot spot. Four pieces of cold iron are arranged in each place to form a circle as shown in the figure.
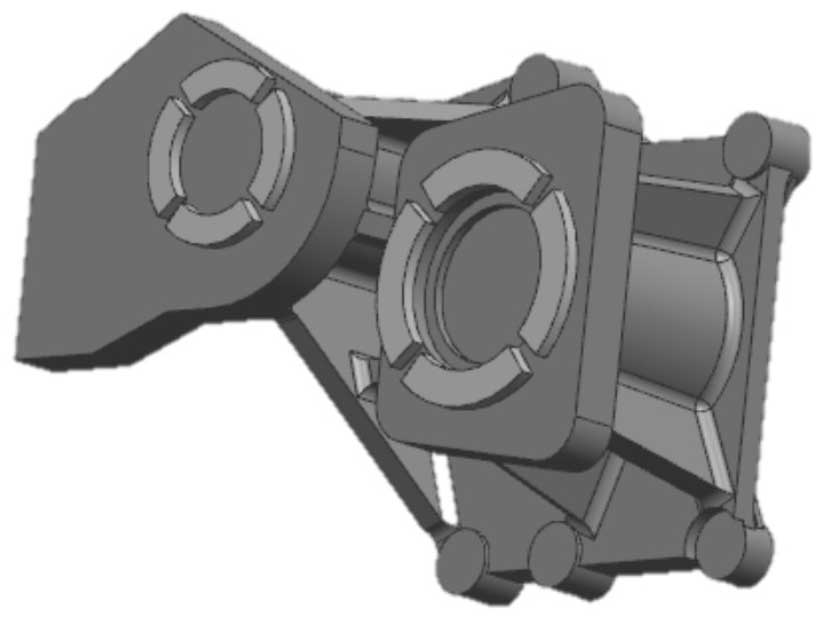