The inlet cylinder is one of the typical high difficulty ductile iron castings. Its solidification characteristics are closely related to the solidification theory of ductile iron and the unique complex structure of the castings. The casting properties of nodular cast iron are closely related to their solidification characteristics. Solidification theory is an important basis for the study of casting characteristics. Therefore, the study and analysis of solidification theory combined with the structural characteristics of castings is the prerequisite for the research on the casting technology of inlet cylinder and the formulation of the technical scheme for defect prevention and control.
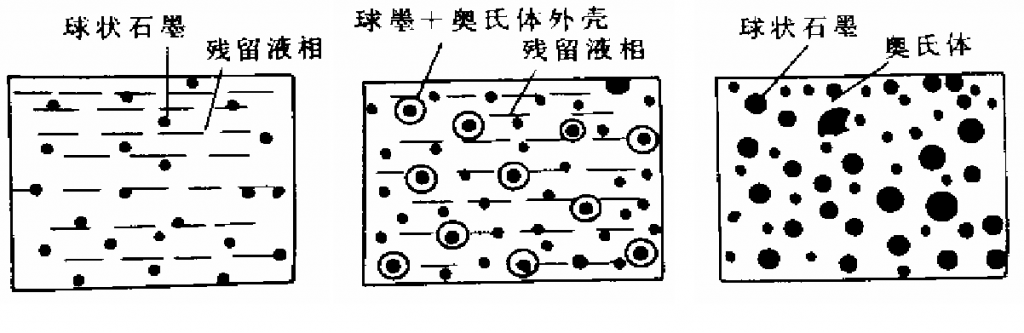
The solidification process of nodular cast iron can be roughly divided into: primary phase precipitation Eutectic Transformation residual liquid iron solidification. The eutectic process is usually called divorced eutectic, which is an important part of nodular cast iron casting solidification forming dense structure. The research of eutectic process is the basis of casting quality assurance. The whole eutectic transformation process needs to be completed in a large temperature range and a long period of time. Generally, the Eutectic Transformation of nodular cast iron is divided into three stages, i.e. the initial stage of solidification, the middle stage of solidification and the completion of solidification. The transformation process of graphite morphology and liquid phase in each stage is shown in Fig. 1. There are three main solidification characteristics of the inlet cylinder casting
(1) The eutectic solidification time of intake cylinder casting is long.
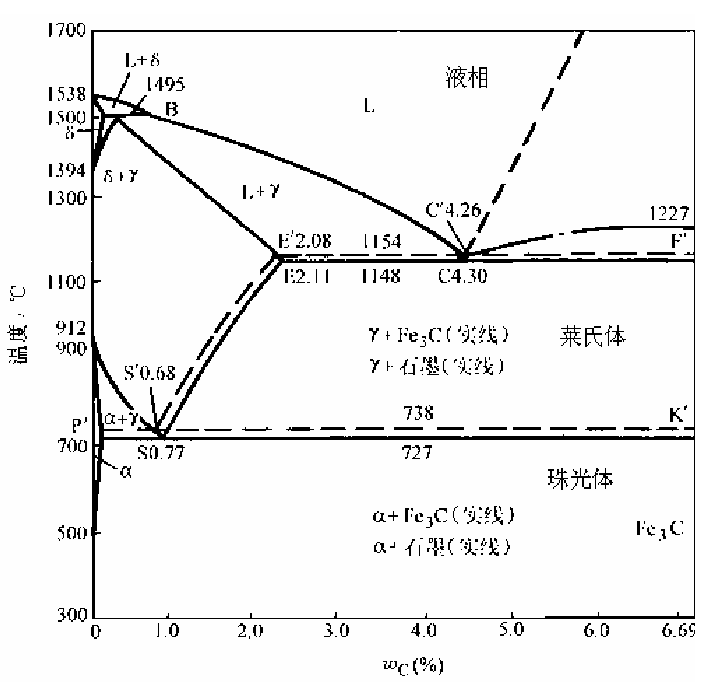
The cylinder is made of fcd450. According to the previous experience in producing similar castings, the carbon content of the finished product is estimated to be about 3.5 ~ 4.0 wt.%. According to the analysis of iron carbon phase diagram (Fig. 2), the eutectic temperature range is relatively wide. The theoretical study shows that after the eutectic group grows to a certain extent, the speed will gradually slow down or stop. At this time, the molten iron must rely on further supercooling as the driving force to promote the formation of new crystal nucleus. However, due to the concentrated high temperature molten iron coating on the thick section, the cooling speed in the mold is slow, resulting in the low undercooling degree during solidification. The inlet cylinder belongs to the super thick and large section ductile iron casting, and the solidification time of the position with large thickness and super thick wall thickness is prolonged. Therefore, the whole solidification process will last for a long time.
(2) The casting of the inlet cylinder is proportional solidification.
Due to the wide range of eutectic temperature, there is a large liquid-solid two-phase region in the solidification process of the inlet cylinder casting. Due to the influence of different thickness and thickness of casting wall, different cooling rate of molten iron in mold cavity, local temperature and heat dissipation conditions, the “liquid-solid” two-phase zone is unevenly distributed according to the structure of the casting, so that the whole casting shows strong balanced solidification characteristics. During the solidification process, liquid and solidification shrinkage occur simultaneously without obvious boundary. In the process of casting process design, according to the traditional theory, the sequential solidification of castings is usually carried out by means of gate design, chill quenching and feeding by setting riser at the final solidification position. However, it is difficult to realize the balanced solidification characteristics of the intake cylinder castings. The main advantage of balanced solidification is that the casting has certain self feeding ability and high process yield. However, for the complicated casting structure such as intake cylinder, the process design is difficult.
(3) There is a large eutectic expansion in the intake cylinder casting.
Due to the inherent characteristics of long eutectic solidification time and balanced solidification of nodular cast iron, the shell solidified at the early stage of solidification process is in a soft and non strength state for a long time. After Eutectic Transformation, C dissolved in molten iron will crystallize in the form of graphite with eutectic transformation. The precipitation of graphite can increase the volume of molten iron by about 2 times, which leads to graphitization expansion. Some research results show that the graphitization expansion force can be as high as (5.065 ~ 10.13) × 105Pa, which will lead to mold wall yielding. If the mold has problems such as insufficient rigidity and surface density, its deformation resistance to graphitization expansion is poor, and the casting shape will produce defects such as larger size, bulging, fleshy, iron clad sand, etc There are some serious quality problems, such as the lack of compactness.