In this test, 6 test pieces were poured in the same ladle of molten steel. The chemical composition of molten steel was detected before pouring, and the initial carbon content was 0.09%. After casting is completed and the casting is cooled down, the box is opened for sand dropping, and then the pouring riser is cut off for pouring. Sampling and sample preparation are carried out according to the sampling position specified in the drawing. Finally, the chemical composition is determined by direct attack spectrometer.
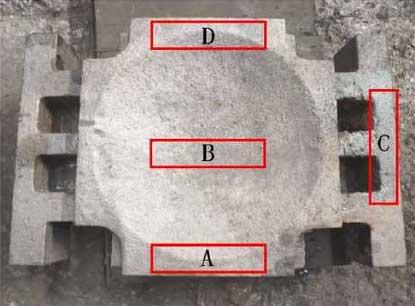
For low carbon steel castings, EPS foam is significantly more carbonized than STMMA foams. The average carbon addition range of EPS foams is between 0.10%~0.25%, the maximum value of single point carburizing is 0.3%, while the average carbon content of STMMA foams is between 0.005%~0.070% and the maximum value of single point carburizing (0.085%) is less than 0.1%. This is due to the fact that the molecular formula of EPS is C8H8, and the carbon content is as high as 92%. More elemental carbon is generated during high temperature pyrolysis, which increases the probability of elemental carbon being absorbed by molten steel, so the carburization is serious. The STMMA foam material is a copolymer of EPS and PMMA (molecular formula C5O2H8). The carbon content is only 69.6%, and the molecular formula contains oxygen atoms. At high temperature, it can react with single carbon to form CO gas, which greatly reduces the chance of carbon absorption by molten steel. Therefore, the use of STMMA copolymer can effectively solve the problem of surface carbon carburization of steel castings.
In addition, comparing the data of foam materials and different sampling locations, it can be seen that the carbon content of the four sampling locations is very different, but the overall trend of change is that the internal gate begins to increase gradually along the soft liquid direction of the molten metal, and the larger the distance from the inner gate is, the greater the carbon content will be. This is because the front of the molten steel always contacts with the foam pattern when pouring. With the increasing contact area, the amount of elemental carbon generated by gasification is more and more, and the carbon absorbed on the coating wall is also increasing. Therefore, the farther the distance from the inner gate, the longer the soft moving distance of the molten steel is, the more serious the carbon increase on the surface of the casting. For the same casting, the distance between the sampling parts C and D and the inner gate is basically increased, but the carburization amount of the final solidification Part D is higher than that of the earlier solidification position C. This indicates that the longer the contact time between molten steel and pyrolysis residue during solidification, the greater the extent of carburization.