Automobile brake is the most important part of automobile chassis system, which bears the main responsibility of safe driving. In 2015, the global brake system market size was 20.72 billion US dollars, which is expected to reach 31.94 billion US dollars by 2021. The market share of disc brakes in passenger car market increased by 31% from 2007 to 2017. The demand for disc brakes has been driven by increased vehicle production, reduced braking distances, safety level certification, vehicle evaluation procedures, and mandatory installation of electronic brake systems.
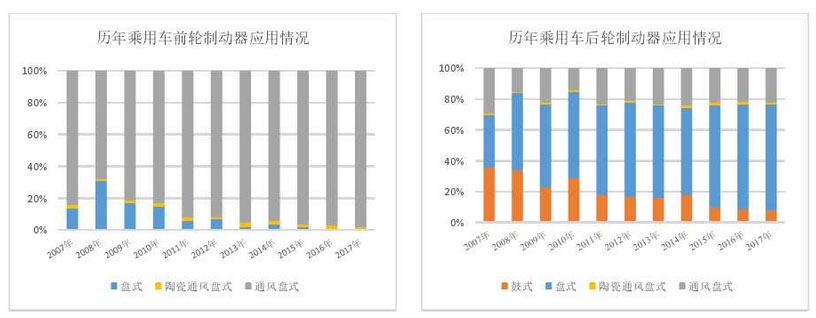
In recent years, with the rapid development of China’s automobile industry, disc brake gradually replaces the traditional drum brake and becomes the mainstream application mode of domestic passenger car market. Figure 1 shows the change trend of market share of disc brake and traditional drum brake in 11 years after 2007. Compared with drum brake, disc brake has the advantages of fast heat dissipation, light weight, simple structure and convenient adjustment. Especially under high load, it has good high temperature resistance, stable braking effect and good thermal stability.
As shown in Figure 2 The disc brake is mainly composed of brake disc, oil cylinder, oil pipe, brake caliper, bracket, friction plate and other parts. The end faces of both sides of the rotating brake disc are used as friction pairs, and the brake block composed of friction material and its metal back plate is installed on its fixed bracket. These brake blocks and their tensioning devices are installed in the clamp shaped supports across both sides of the brake disc. When the car is braked, the piston in the brake caliper cylinder is affected by the hydraulic pressure transmitted by the oil pipe, which pushes the brake pad to press the brake disc to produce friction braking, forcing the moving mechanism to stop moving. Therefore, the brake caliper plays a very important role in the disc brake system. Most brake calipers are designed as nodular iron castings. Due to the high temperature, high pressure, fatigue, sealing and corrosion tests in the braking process, high requirements are put forward for the mechanical properties, size, internal defects, natural frequency and surface quality of the brake caliper.
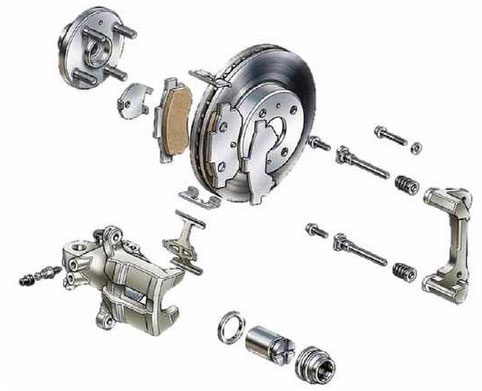
In the past decade, the automobile industry has ushered in another opportunity of rapid development, and some new concepts have been put forward. Many scientific research institutions and enterprise research and development institutions have spent a lot of resources to develop new energy vehicles, driverless technology and other emerging technologies, and have made certain progress, but all the achievements are only aimed at the innovation of the traditional driving mode and driving mode of the automobile, while the automobile industry has made some progress The impact of the chassis, especially the mechanical brake system, is not big. In addition, in order to meet the requirements of lightweight development of automobile, the material of some rear wheel brake calipers is replaced by cast aluminum alloy, but the material of front wheel brake caliper is still mainly made of nodular cast iron, because most vehicles are driven by front wheel. Due to the effect of inertia, the load of front wheel usually accounts for the total load of automobile when braking 70% – 80%, so more braking force is needed. At this point, the performance of ductile iron material is much higher than that of aluminum alloy. However, the ductile iron brake caliper is also affected. After meeting the performance design requirements of the brake system, in order to control the single weight of the brake caliper parts, the casting performance of the product can not be fully considered. As a result, the structural wall thickness of the parts is greatly different, and there are many isolated hot spots, which is easy to produce internal defects, which brings a severe test to the traditional casting industry. How to complete the production of brake caliper castings with high quality and efficiency to meet the rapid development needs of automobile manufacturing industry has become an urgent problem to be solved.