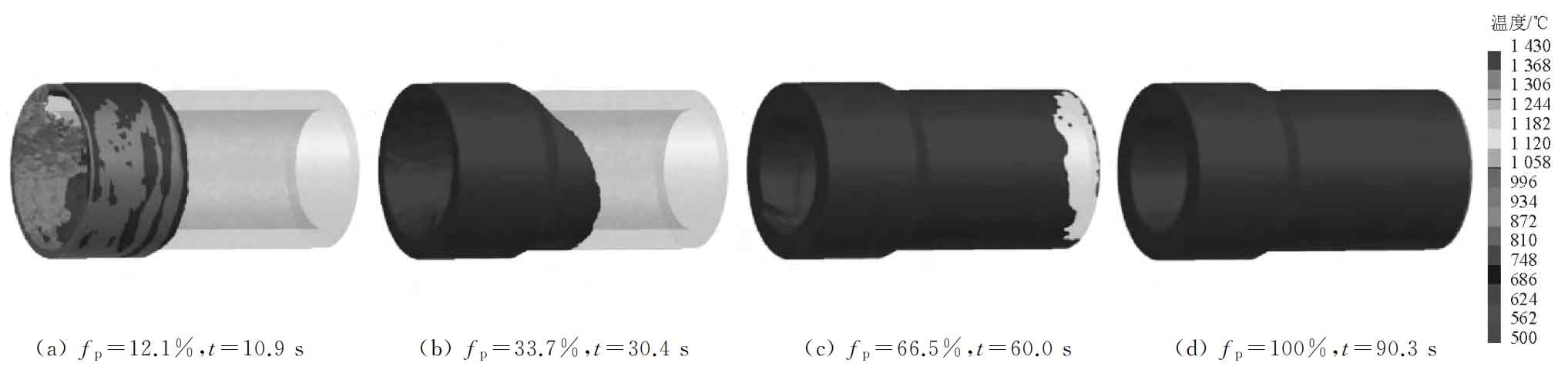
Figure 1 shows the simulation results of temperature field in the process of filling, solidification and cooling of liquid metal during horizontal centrifugal casting of super large cylinder liner. It can be seen that the liquid metal moves forward in the form of laminar flow after entering the mold, where FP is the mold filling rate of the horizontal centrifugal casting of the cylinder liner, and t is the pouring time. When the metal liquid enters the mold from the inlet, there is a discontinuity. The metal liquid just entering the mold contacts the metal mold wall and is subjected to the chilling effect. Due to the rapid cooling speed of the metal mold, the temperature of the metal liquid decreases during the rotation process, as shown in Figure 1A. The temperature of the molten metal near the left end of the mold is about 100 ℃ lower than that at the inlet. Some molten metal even solidifies, and it is easy to get a fine grain layer. At this time, the solid content is 0.4%. Subsequently, more liquid metal continued to flow into the mold, moving forward on the previous liquid metal layer, and the thickness of the liquid metal continued to increase. Later liquid metal continued to transfer heat to the liquid metal that had entered the mold, as shown in Figure 1b, so that its solid rate became 0 again. The metal liquid flowing in the back will continue to repeat this layered flow until the whole cavity is filled, and the sharing time is 90.3s.
Figure 2 shows the radial and axial temperature field distribution results of liquid metal filling in horizontal centrifugal casting. It can be seen that the temperature field of molten metal is evenly distributed in the radial direction, with the maximum temperature of 1430.0 ℃ and the minimum temperature of 1381.2 ℃, which is caused by the bidirectional heat transfer between the inner surface of molten metal and air, and between the outer surface and the mold; In the axial direction, the temperature field is low at both ends and high in the middle. The highest temperature is at the thick wall end of the horizontal centrifugal casting of the cylinder liner. As some molten metal first contacts the mold and is cooled, the temperature drops, resulting in the temperature at this place being lower than the surrounding temperature. The maximum temperature is 1430.0 ℃, the minimum temperature is 1283.5 ℃, and the temperature difference is large. In the radial direction, the temperature distribution is relatively uniform, the temperature near the mold surface is the lowest, and the maximum temperature difference with the molten metal is about 47 ℃.
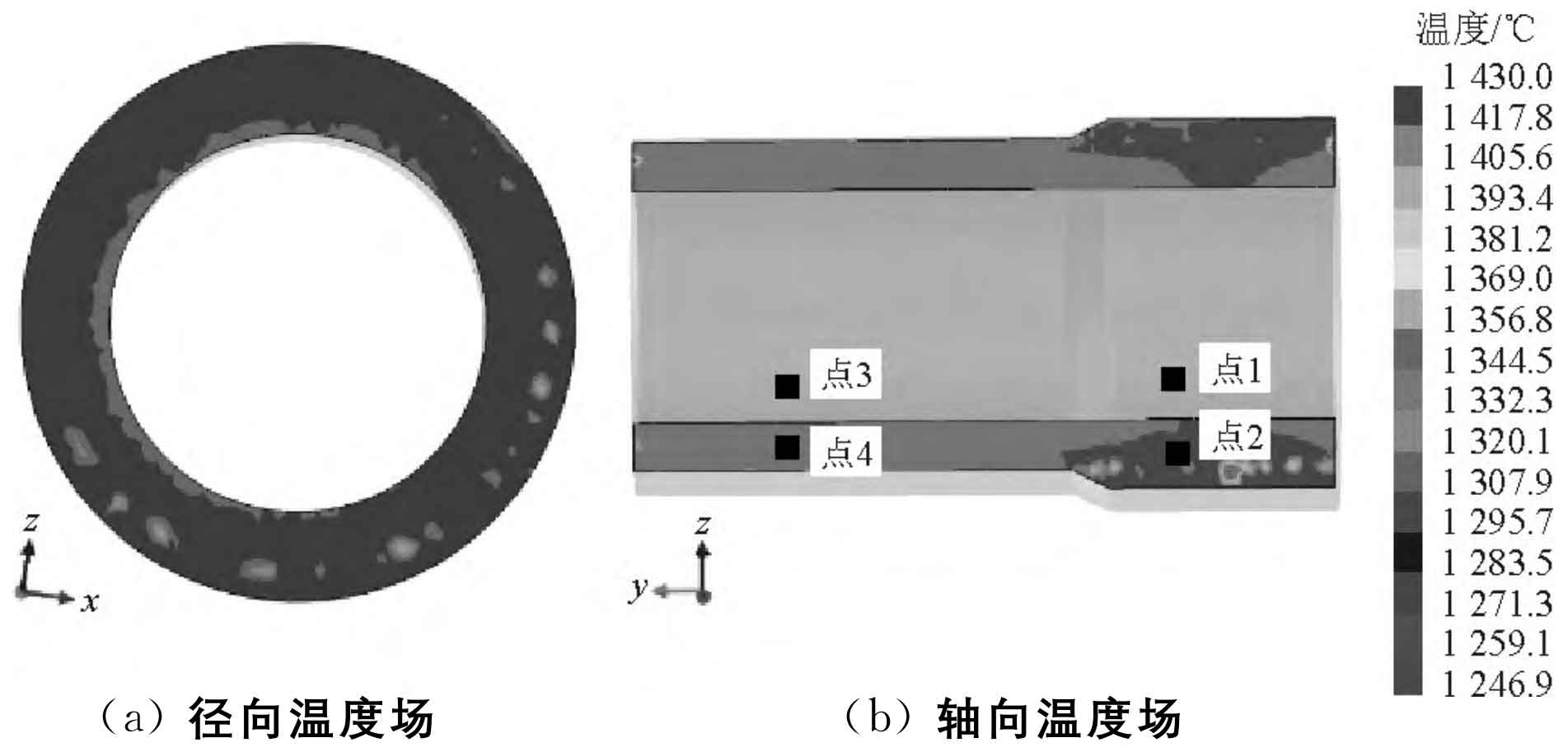
In addition, the temperature at the thick wall end of the horizontal centrifugal casting of the cylinder liner close to the inlet of the liquid metal is higher than that at the thin wall end of the horizontal centrifugal casting of the cylinder liner away from the inlet, and the temperature distribution becomes uneven, especially at the junction of the thin wall and the thick wall of the horizontal centrifugal casting of the cylinder liner, which is also related to the selection of the inlet near the thick wall end. In actual production, the uneven temperature field will lead to uneven stress and even cracking of the horizontal centrifugal casting of the cylinder liner.
After the molten metal enters the mold, take four points on the inner and outer surfaces of the horizontal centrifugal casting of the cylinder liner close to and away from the inlet, as shown in Figure 2B. Point 1 (13.25, 19.80960) and point 2 (19.4980, 19.80960) are points close to the inner and outer surfaces of the inlet position respectively, and point 3 (13.25500) and point 4 (17.6500) are points away from the inner and outer surfaces of the inlet position respectively.
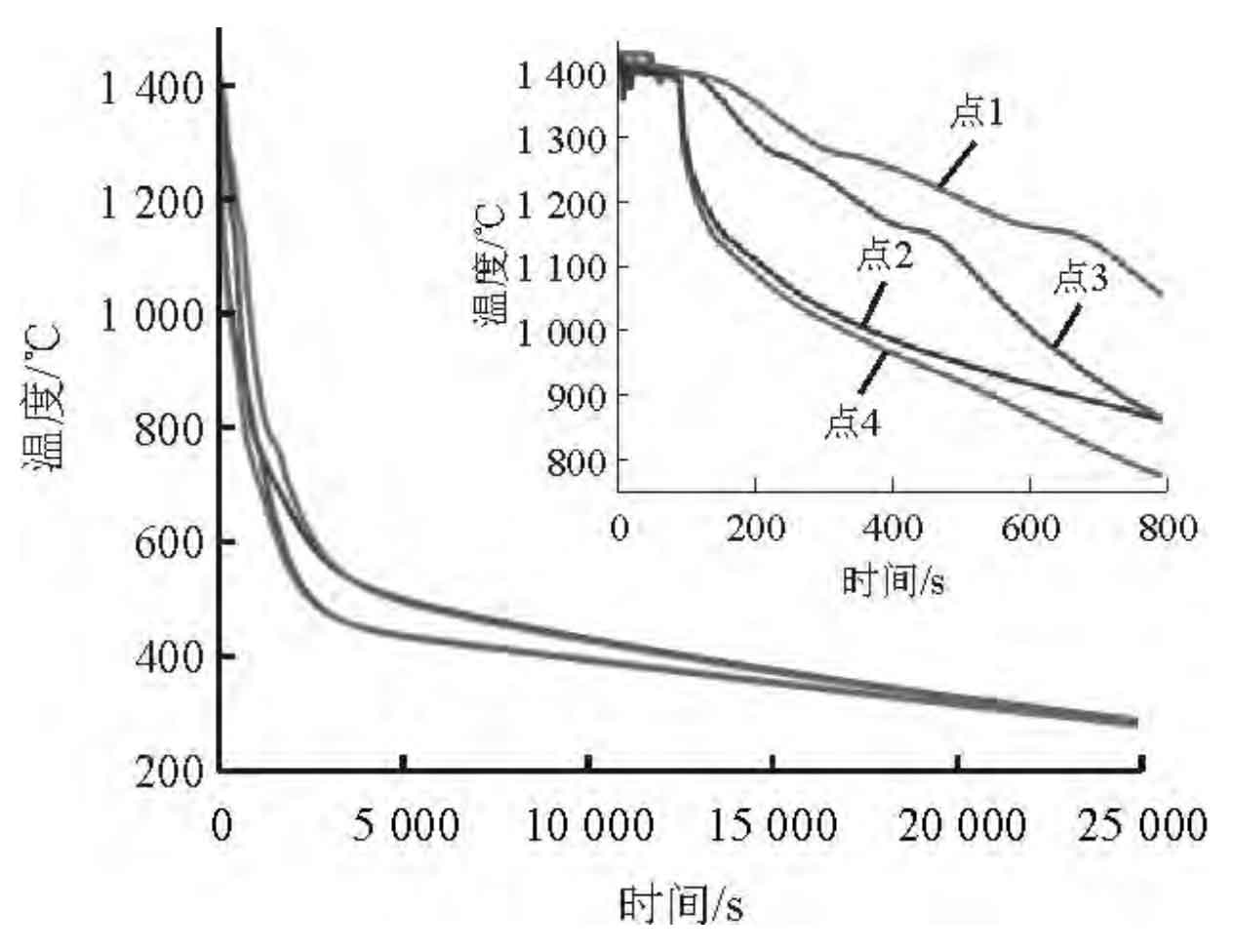
Figure 3 shows the temperature change curve with time from the beginning of mold filling to the solidification of horizontal centrifugal casting of cylinder liner. It can be seen that the cooling speed of the molten metal is fast at the beginning and slow at the end. This is because as the temperature of the molten metal decreases, the temperature gradient between the molten metal and the mold decreases, and the heat dissipation capacity of the mold decreases. The temperature of the outer surface of the horizontal centrifugal casting of the cylinder liner is always lower than that of the inner surface; The temperature of the molten metal near the inlet is high, and the temperature of the molten metal far away from the inlet is low, and the temperature difference between the inner and outer surfaces of the point near the inlet is greater than that of the point far away from the inlet; The metal liquid far away from the inlet cools faster. It can also be seen from the enlarged figure that the four curves fluctuated violently before 90s, which was caused by the continuous mold filling flow of molten metal. Within 1277 ~ 1430 ℃, the cooling rate of the liquid metal is faster, but after 1277 ℃, the cooling rate of the liquid metal slows down, and even a temperature platform appears, because the liquid metal enters the solidification stage, and the latent heat of crystallization is released during crystallization.
At the inlet of molten metal, the cooling speed is slow under the same cooling conditions due to the high temperature of molten metal. In addition, the liquid metal advances in the mold in the form of laminar flow. Because the metal mold has strong thermal conductivity and fast cooling speed, the surface of the horizontal centrifugal casting of the cylinder liner is cooled, which is conducive to the solidification of this part of liquid metal first. The inner surface of the liquid metal is air-cooled, and the cooling speed is slow, so the heat flow direction is perpendicular to the mold wall outward. The horizontal centrifugal casting of the cylinder liner has directional solidification to produce columnar crystals, and the liquid metal solidifies at the last scouring position, which is easy to produce shrinkage, cracks and other defects due to solidification shrinkage. Due to the large centrifugal speed of the mold and the increasing pressure along the radial direction, a large centrifugal force is generated, and the dendrites are constantly broken. The dendrites washed down can be used as the core of heterogeneous nucleation, achieving the effect of refining grains, and making the structure of horizontal centrifugal castings of cylinder liners dense.
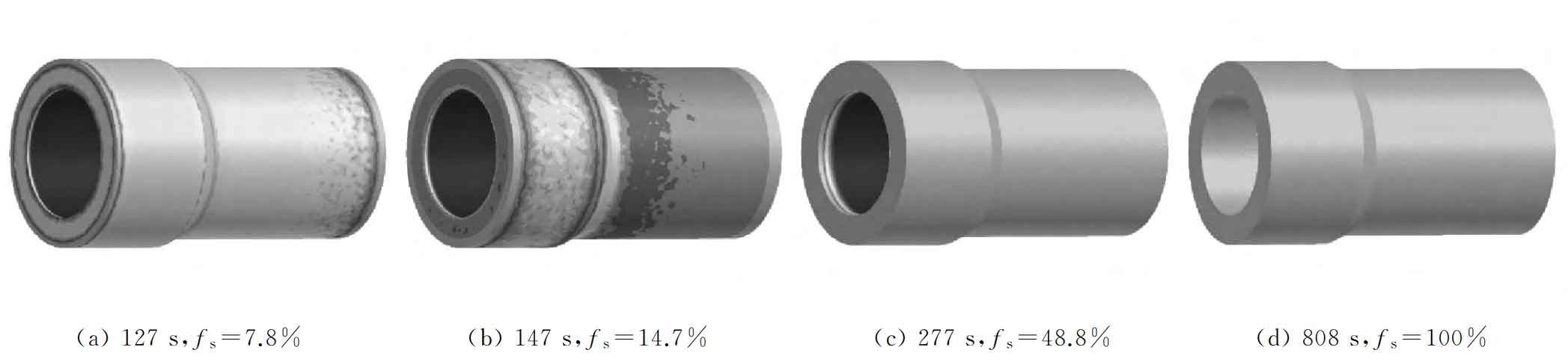
Figure 4 shows the solid fraction (FS) of horizontal centrifugal casting of cylinder liner at different times. It can be seen that the liquid metal has completely solidified at 808s. The solidification sequence of horizontal centrifugal casting of cylinder liner is as follows: solidify at both ends in the axial direction first, the liquid metal at both ends transfers heat to the mold through heat insulation materials, and solidify in the middle. The ratio of surface area to volume (specific surface area) at the thin wall is greater than that at the thick wall, so the heat dissipation is faster and the solidification is faster; In the radial direction, the solidification starts from the outer surface first, and solidifies layer by layer from the outside to the inside. This is because the outer surface of the horizontal centrifugal casting of the cylinder liner is in contact with the coating and the mold, and the temperature drops faster, which also conforms to the laminar flow law.
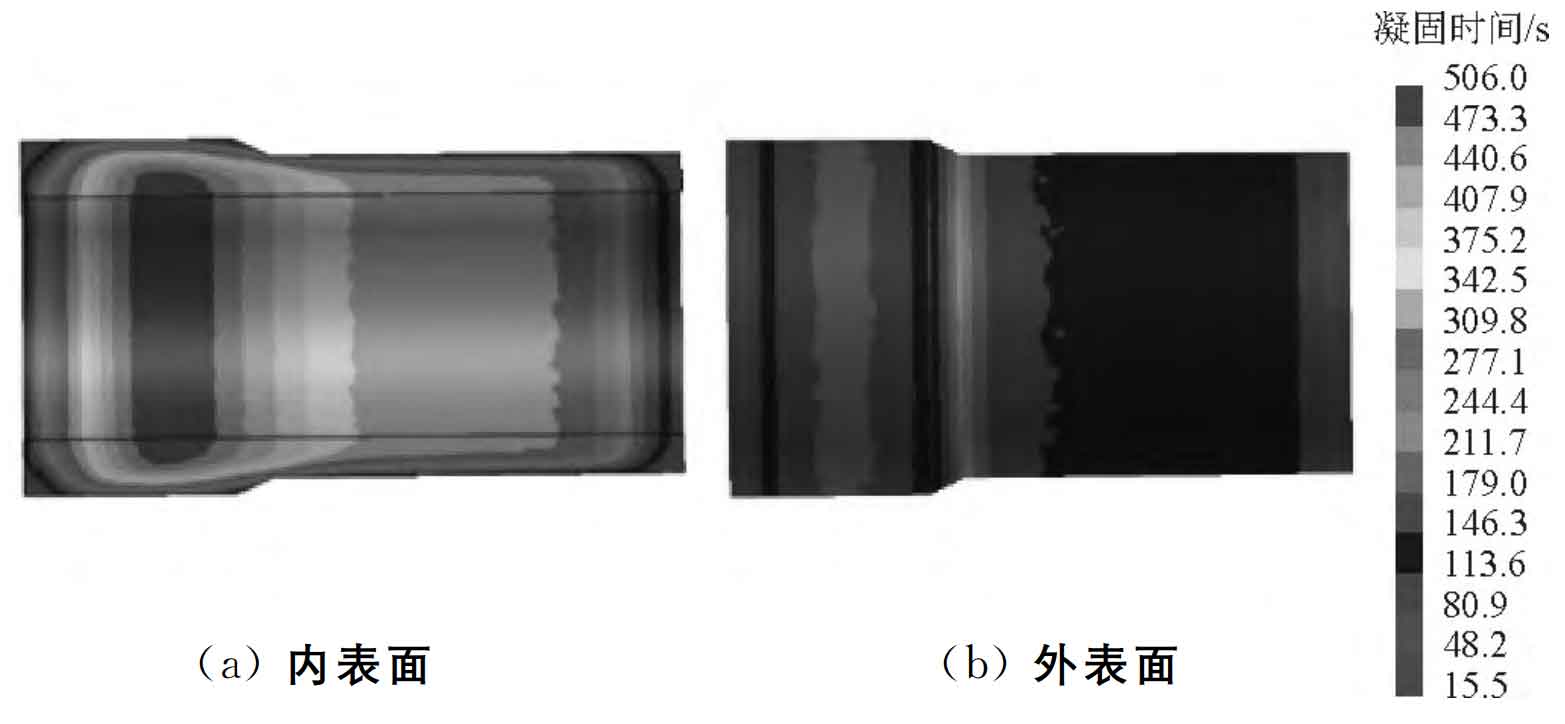
Figure 5 shows the solidification time of horizontal centrifugal casting of cylinder liner at various positions. In terms of solidification time, the middle wall thickness is at the last solidification position, which is prone to hot spots and other defects, as shown in Figure 5A. The solidification time at the junction of thick wall and thin wall on the outer surface of the horizontal centrifugal casting of the cylinder liner is the longest. In addition, the radial dimension of the horizontal centrifugal casting of the cylinder liner here changes abruptly, which is easy to produce defects such as thermal stress concentration, as shown in Figure 5B.