(1) Preservation of casting coatings
Prevent drying; Prevent freezing; No entry of mold and miscellaneous bacteria; After use, it shall be covered and cannot be placed open.
(2) Mixing of casting coating
Adequate and uniform mixing is the key to the casting coating tank, and the rotary casting coating tank is the best; Bubbles shall not be involved during mixing. The entrapped bubbles will remain in the dry coating, and the molten metal will enter the bubbles during pouring to form cold bean defects; If the mixing is sufficient, the refractory aggregate will settle slowly and operate well.
(3) Application of casting coating
The application of casting coatings mainly includes brush coating, dip coating, spray coating and flow coating.
Brush coating is the simplest and most widely used method. It is widely used in single room and small batch production. When brushing, the coating thickness is generally between 0.3-2mm. If the required thickness cannot be guaranteed at one time, it can be brushed for 2-3 times. The disadvantages of brush coating method are high labor intensity and low production efficiency.
Dip coating method is mainly used for coating sand cores. Dip coating has high production efficiency, easy to obtain smooth coating surface and easy to realize mechanization. There are two main dip coating methods: one is sand core movement and casting coating tank is fixed, which requires manual operation and is suitable for single room small batch production. The other is that the sand core is fixed and the casting coating tank moves, which can realize mechanized continuous operation and is suitable for mass production. The viscosity characteristic during dip coating is pseudoplastic fluid. Under the action of shear force, the viscosity of the casting coating drops sharply, and the casting coating will be covered on the surface of the sand core. Then the sand core is taken out, the shear force disappears, and the viscosity rises and recovers, so that the dripping of the casting coating stops and the drip marks are avoided. It is applicable to the casting coating with high viscosity, wettability and thixotropy. During dip coating, attention shall be paid to prevent the casting coating from immersing in the exhaust duct of the sand core, so as not to affect the exhaust effect of the core. At the same time, it shall also avoid the core from adhering to the casting coating, so as to prevent the core from becoming thicker and making it difficult to lower the core.
Spraying method is applicable to large area sand mold (core). The method has high production efficiency, meets the needs of mechanized flow production, and has uniform coating thickness and no brush marks. There are three types of spraying methods, namely, air spraying, low-pressure hot air spraying and high-pressure airless spraying. The main equipment of air spraying method is air compressor and spray gun. The spray gun has two types: suction type and pressure type, which are respectively suitable for small amount of spraying and large amount of continuous spraying. The characteristics of low-pressure hot air spraying are that the air is preheated to over 20 ℃ higher than the room temperature and the air pressure is as low as 0.35-0.7kg/cm2. In addition, the casting coating is generally preheated to 50-65 ℃. The viscosity of the casting coating decreases after preheating. The casting coating particles are sprayed on the surface of the sand core at one time, eliminating the fog and the rebound of the coating drops, improving the working conditions and saving the casting coating. The high-pressure airless spraying method is to store the casting coating in a high-pressure vessel after the pressure of the casting coating rises, and spray the casting coating by using the pressure of the casting coating itself. The casting coating is dispersed into small droplets through the nozzle and sprayed onto the surface of the sand core. It has little impact on the surface of the sand core, little rebound of solid particles, easy formation of the coating, small dispersion loss of the casting coating, easy accumulation of the coating, smooth surface, and is also conducive to the application of the recess, Less loss of casting coating. Its disadvantages are complex equipment, inconvenient maintenance and high cost. In addition, during spraying, dust and carrier liquid are atomized and scattered into the air, causing serious environmental pollution and adverse to workers’ health. When spraying alcohol based casting coating, the carrier liquid is atomized and dispersed into the air, which is easy to cause fire.
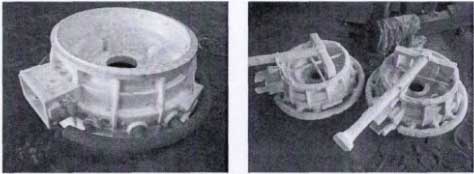
Flow coating is a low pressure spraying method. Pump out the casting coating, spray the casting coating on the large sand mold (core) surface through the flow nozzle, and the excess casting coating flows into the lower liquid collecting tank for further use. The low-pressure pump makes the casting coating in the coating barrel flow to a row of nozzles through the hose. The nozzle is a spray head composed of a plurality of small holes to form a casting coating curtain that sweeps through the mold cavity or sand core surface. High production efficiency of flow coating, suitable for batch or mass production of large sand cores without concave. The viscosity of casting coating used for flow coating is lower than that of dip coating, so as to obtain the required fluidity. The coating thickness can be adjusted by changing the viscosity of casting coating.