According to the test results of shrinkage and porosity defects, the shrinkage and porosity defects are mainly concentrated on the test blocks with thickness of 400mm and 150mm. Therefore, the change trend analysis is mainly based on the two wall thickness test blocks. The C content was used as a variable factor to analyze the defect volume detection results to determine the influence trend of C content on the shrinkage porosity tendency; the scrap addition proportion was used as the variable factor analysis table 3-5 The results show that the influence trend of the proportion of scrap steel on the shrinkage porosity tendency is determined. The difference of scrap steel proportion indicates the influence trend of different content of unknown trace alloy elements on the shrinkage porosity volume.
The volume change trend of shrinkage cavity and porosity of test block with different C content is shown in the figure.
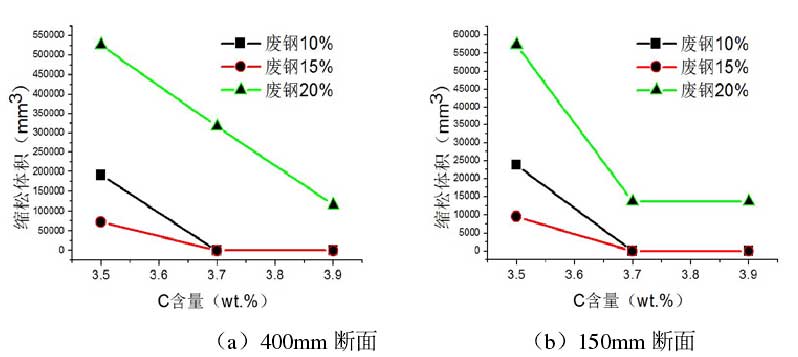
It can be seen from the figure that the shrinkage tendency of the inlet cylinder block is the minimum when the C content is ≥ 3.7 wt.%. Our company has studied the effect of C content on shrinkage cavity and porosity in a ductile iron product. The solidification curve of different C content shows that the eutectic platform of low carbon is obviously smaller than that of high carbon, and the liquid shrinkage is large. When the carbon equivalent is about eutectic composition, the fluidity of molten iron is the best and the density of casting structure is the highest. C. Si is one of the most important elements affecting the graphite precipitation in nodular cast iron. Reynolds et al. Proposed a long time ago on the basis of statistical analysis to obtain the conditions of wt. (c)% + wt. (SI)% / 7 > 3.9wt.%. These results also fully demonstrate the minimum shrinkage tendency when the C content is more than 3.7 wt.%.
According to the diagram, the optimum scrap adding proportion is 15%. With the increase of scrap steel ratio from 10% to 20%, the tendency of shrinkage cavity and porosity increases, and the volume of shrinkage cavity and porosity also increases. The research results of the influence of interference elements on the microstructure and properties of ductile iron by cast iron Association of China show that at present, various steels have tended to be thin-walled and lightweight, which leads to the wide application of low-alloy steels. When these scrap steels are used in the furnace, a variety of trace alloying elements have a serious and thorny negative impact on ductile iron, but they are faced with the requirement of low-cost market competition, Scrap steel must be used as a substitute. The research results of Japan’s Mitsui Institute of technology show that with the increase of the content of trace elements Ti and Al, the fluidity of molten iron becomes worse, and the tendency of shrinkage cavity increases. The increase of WT (AL)% from 0.02 wt.% to 0.4 wt.% in ductile iron will lead to the increase of shrinkage defects. In daily production, the matching batching process and high purity pig iron correction are usually used to control the composition of molten iron and eliminate the influence of interference factors.