The exhaust system of large castings mainly considers the exhaust of mold cavity and sand core. It is difficult to exhaust because the side of the body is upward. Because the main side of the body is plane, there is no need to use riser feeding. The design idea of large exhaust is mainly adopted. Through the design of large exhaust channel, the filling capacity of molten iron is improved, and the supercooled molten iron and scum that enter into the mold cavity first are eliminated, and the casting defects such as insufficient pouring, porosity and shrinkage porosity are prevented. According to the structural characteristics of the casting, the gas in the casting cavity is mainly discharged from the top surface of the large side of the casting. There are many flanges, boss, plane and many screw hole laps on the side of the body. The exhaust area is large, which can form an ideal exhaust channel. Therefore, the exhaust needle is mainly set in these places. The air exhausting needle adopts the open air exhaust needle, which is directly connected to the top surface of the sand box, and can quickly remove the gas in the mold.
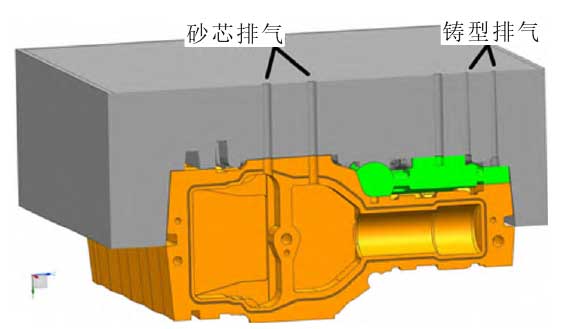
The exhaust design of sand core mainly includes the main sand core, tappet chamber sand core and waterway sand core. The molding process of the machine body adopts resin self hardening sand. The characteristics of the resin sand process are that the gas generation is larger than that of the clay sand, and the volume shrinkage of the resin adhesive film is severe above 600 ℃, and the density is increased, so the air permeability of the sand mold is greatly reduced [8]. Therefore, a separate exhaust channel should be set up for the exhaust of the main sand core. The exhaust channel of the main core is designed by using the space of the side observation window of the body. The exhaust channel directly passes through the upper mold and is connected with the atmosphere, which can effectively eliminate the gas generated by high temperature in the main sand core, as shown in Fig. 1.
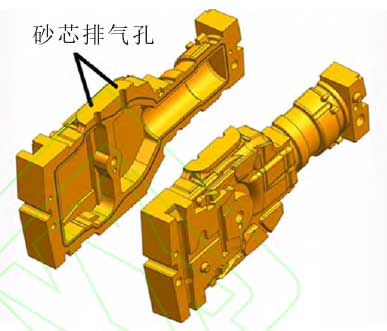
When the sand core is large, the gas generation of sand core is also large. The sand core of the main body of the casting is thick and bulky, and the weight of a single sand core is about 110kg. According to the requirements of core assembly, eight main sand cores and the front and rear sand cores are penetrated through the sand core group through three long bolts. After fastening, the special fixture is used to lower the core. The overall weight of the sand core group is about 1000kg, and the sand core group has large weight and gas generation. Therefore, in the design of the main sand core, the idea of reducing weight and adding exhaust passage is adopted. As shown in Figure 2, the main sand core can be divided into two parts, and the back of the sand core can be hollowed out with the mold. In order to ensure the strength of the sand core, the inner cavity exhaust channel of the sand core can be designed at the window space of the observation room. The lb65 cold core box is used for core making to ensure the dimensional accuracy, and finally the core making process of glue bonding is used.