In the process of five axis machining, due to the large amount of data, the control system can not carry out a lot of inverse RTCP calculation in advance, and the motion speed can only be calculated according to the programmed coordinates. Based on this principle, when using five axis vector speed control, the time interval t between each group of command points can be calculated according to the ratio of programmed coordinates and programmed speed, as shown in formula. Where f is the programming speed, μ x, μ y, μ Z, μ B, μ C are the standard units of length or angle, which are converted into the number of pulse values.

Without restriction, the feed rate of each axis can be obtained by dividing the position increment of the inverse solution of RTCP by the time interval
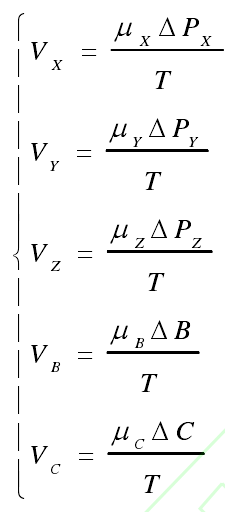
The vector speed of five axis linkage machining is the vector sum of the speeds of each axis

It can be seen from the above that in the process of five axis linkage machining, the actual operation of each axis is the inverse solution position of RTCP, while the movement time is determined according to the positive solution position, resulting in the linear axis speed greatly exceeding the programming speed, or even exceeding the maximum speed limit. When the tool length is long, the actual speed of linear axis exceeds the programming speed obviously. In the process of 5-axis high-speed forming of sand mold, if the linear axis speed is too high, it will cause equipment vibration and alarm, and the sand mold material is fragile, which will easily cause sand mold forming defects and damage the sand mold.