The causes of casting defects in the trial production of guide rail steel castings were analyzed, and the specific results are as follows:
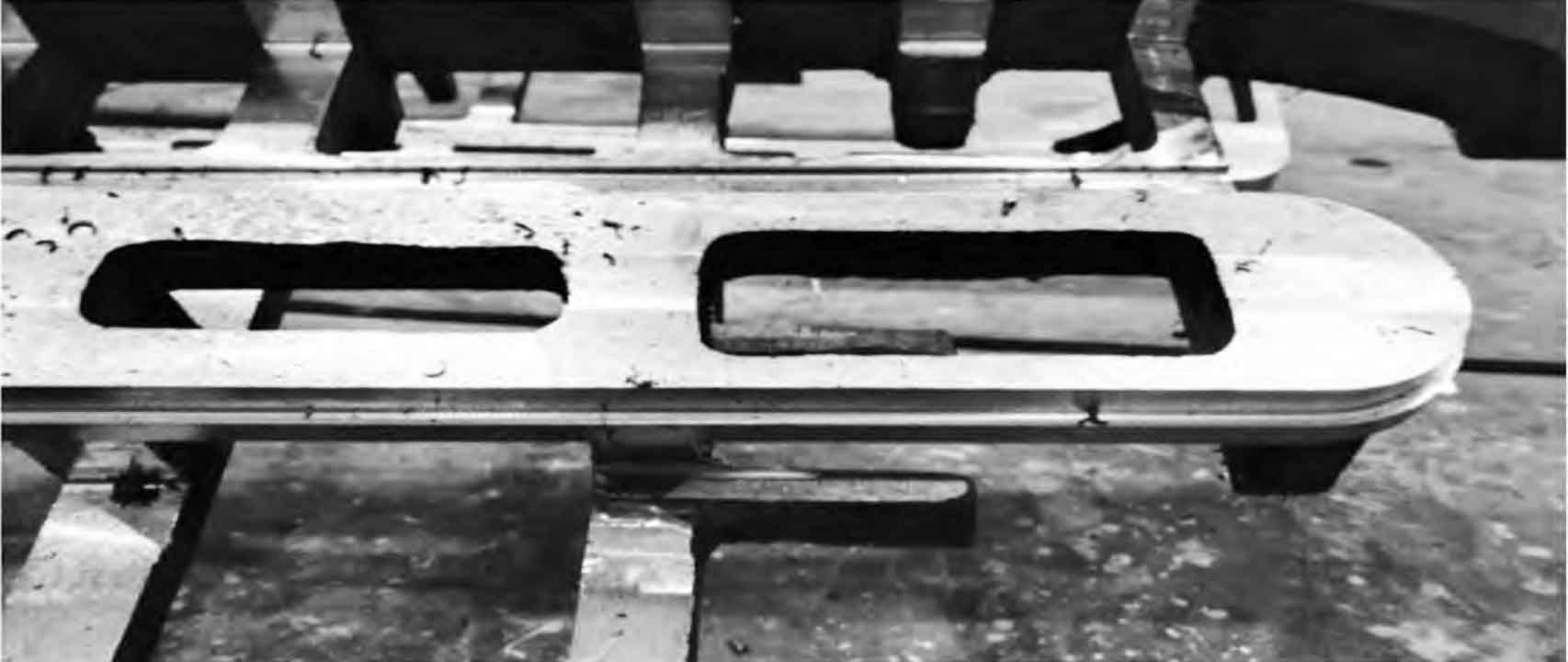
(1) There are insufficient pouring and cold shut casting defects in the middle and edge of the upper plane of the guide rail steel casting. Due to the complex structure, large wall thickness differences, and large outline dimensions of guide rail steel castings, severe heat loss at the front end of the liquid phase and high mold filling resistance occur during the filling process of liquid metal, resulting in insufficient pouring and cold shut off at the distal end.
(2) There are thermal cracks at the corners of individual connecting ribs of guide rail steel castings. The main reason for the thermal cracking of guide rail steel castings is that during the solidification and contraction process of liquid metal, the internal stress formed due to the core obstruction is greater than the corresponding yield strength of the metal material at this temperature, resulting in plastic deformation, and the feeding of liquid metal cannot be obtained.
(3) The dimension of the guide rail steel casting is out of tolerance. Due to the uneven wall thickness of various parts of the guide rail steel casting, the inner cavity is formed by sand cores, and the shrinkage resistance is increased, resulting in inconsistent linear shrinkage. The oversize of the steel casting in the length direction of the inner cavity is due to the failure of the 1.8% shrinkage rate in the initial design to ensure that the shrinkage in the length direction of the steel casting is blocked, resulting in all the oversized dimensions in the length direction of the inner cavity, resulting in oversized dimensions. At the same time, due to the fact that this steel casting belongs to the “hollow out” thin plate type steel casting, during the solidification and cooling process of the molten metal, it is subject to resistance and contraction. The resistance mainly comes from the obstruction of the sand core and the internal stress of the shrinkage of various parts of the steel casting, resulting in the initially set shrinkage rate not being consistent with the actual situation.
(4) The steel casting of the guide rail is deformed. The four trial produced guide rail steel castings all have upward warpage at the four corners of the guide rail surface, as shown in Figure 7. The main reason for the upward warpage of the steel castings is the stress caused by the solidification of the risers. After the pouring is completed, the final solidification must be the riser, and the overall riser is located in the upper box, and the larger risers are located on both sides of the guide rail length direction, so in the later stage of the riser solidification, It will form an upward tensile force on the steel castings around it, resulting in upward warping and deformation of both ends of the guide rail steel castings.